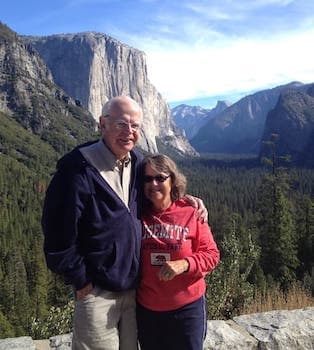
Curated with aloha by
Ted Mooney, P.E. RET
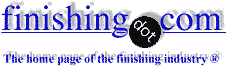
The authoritative public forum
for Metal Finishing 1989-2025
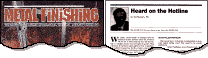
-----
How to know metal is oil free. Water-break test Q&A
Q. Hello,
We paint military aircraft and have come across a problem. We have thoroughly prepared an aircraft for painting and have run all the tests for PH and cleanliness. Our problem is that we cannot get the substrate to pass the water break test. Could this possibly be caused by the anodized coating on the aluminium?
Kirt E. Petron- Richmond, Kentucky
2002
A. Possibly. I cannot vouch for all types of anodizing but with Phosphoric the anodized part will be water break free but once primed (which is pretty much essential after Phosphoric Acid Anodizing) the part will not be water break free.
Ciaron Murphy- Great Britain
A. Most of the time when you are failing the water-break test, it has to do with the precleaning or cleaning steps. You must make sure you are getting a water-break free surface after each cleaning step. What precleaning solutions are you using?
Randy A. MattsonSkills Inc. - Seattle, Washington
Multiple threads merged: please forgive chronology errors and repetition 🙂
How to know metal surface is oil free
Q. Hi,
Can anybody tell me how do I know whether my metal part after pretreatment is really free from oil? any method to confirm? can suggest any titration method or chemical to check on this?
Thank You
ced system - Malaysia
2006
A. The "water-break test" is very simple and has long been used. If after dipping the part in water, the water remains on the as a continuous sheet, it's a good indication of cleanliness. If it beads up at all,in the manner of water on a newly waxed car, it's not clean.
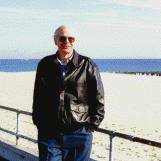
Ted Mooney, P.E.
Striving to live Aloha
finishing.com - Pine Beach, New Jersey
A. You can use a solvent like acetone
⇦ this on
eBay
or
Amazon
[affil links] Warning! highly Flammable!
as a swab to 'clean' half of the part. If you see a difference between the pre-treated area and the acetone cleaned area then you know the part is not cleaned efficiently.
Water break tests often fail as I have seen parts coming out of.
- Halesowen, West Midlands, UK
A. water-break test is widely used to detect any presence of hydrophobic (nonwetting) films and the presence of hydrophobic organic materials in processing ambients.
ASTM F22 is a standard test method for hydrophobic surface films by the water-break test.
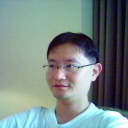
David Shiu
- Singapore
A. The water break test, the common method is to test the surface of steel after treatment stages by noticing the motion of water in the surface of steel from up to down if it is go in stable direction without any round area so there is not any oils on your steel surface.
Ali Gomaa- Cairo, Egypt
2006
Recommendations/requirements for water-break inspection lighting
Q. The company I work for is Nadcap certified for chemical processing. One of our processes is the cleaning and etching of titanium in preparation for penetrant inspection. During a recent audit we had a finding concerning inadequate lighting over the tank line to perform the water break free surface inspection. In an effort to properly address this finding I am looking for the lighting requirements for this type of inspection. Please provide reference to an industry standard or best practice that relates the amount of foot-candles or lumens required when performing this operation.
Kathleen Knechtsurface treatment quality specialist - St. Louis, Missouri
2007
![]() |
A. Kathleen - Colorado Springs, Colorado A. I do not believe you will find an industry standard for water break inspection lighting, so you'll have to write your own procedure. ![]() Jeffrey Holmes, CEF Spartanburg, South Carolina |
A. I agree with the previous responses except to say that the general lighting in plating shops is virtually always inadequate (not just for water-break inspection, but for everything else as well).
Years ago I wrote an article "Plating Shops for the Nineties" for Plating and Surface Finishing magazine. Of the kind comments about it that I received over the years, this one is pretty typical:
"I came upon an article of yours on plating plants for today, and took some of it to heart (plating plants must be bright). Anyhow, I installed six 400W mercury vapor lamps in my shop, holy sh*t! I could not believe the difference. For the past twenty years I had thought my plant to be well lit, but now I can see that I was working in the dark (light as well as ages). It was the best info that you could have given."
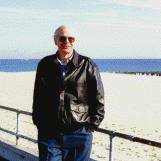
Ted Mooney, P.E.
Striving to live Aloha
finishing.com - Pine Beach, New Jersey
A. Lighting for a water break test can be picky and not follow the norms for lights. I would not rate mercury vapor lamps as great because of the frequency of the light tends to not discriminate well on a polished or smooth surface. It might be great, but try several different types of small lamps to see which one works best.
I know that our shop had good lighting in QC, but a local customer had a different K range than our fluorescent bulbs and could see stuff that we could not. We changed bulbs.
- Navarre, Florida
Multiple threads merged: please forgive chronology errors and repetition 🙂
Standards or tests for 'How clean is clean'?
Q. Hi,
we have recently had an issue of component cleanliness at one of our plants.
The components are small tin plated stampings intended for use on circuit boards with part of the stamping being soldered to the board.
The parts must be free from grease and any processing fluids that may have been used during the forming process and so should go through a cleaning process before being shipped from the supplier.
My question is - what specifications or testing procedures exist that would determine the state of cleanliness of these metal parts ?
Thanks
Mechanical engineer - UK
January 20, 2009
A. Kevin
In the metal finishing world, we use the water break test, ASTM F22 (Standard Test...by the Water Break Test) as a means of ensuring that the parts we are cleaning are free from materials that could interfere with subsequent operations. This may or may not be applicable to your situation.
- Colorado Springs, Colorado
A. The water break-free surface test is probably the easiest and quickest method of verifying cleanliness, but does not allow you to quantify level of cleanliness. Water break can be determined by using only DI/distilled water and a stopwatch. Simply watch for a continuous film of water on your part surface. Any beading or runoff indicates presence of a hydrophobic substance.
Contact angle test is a more sophisticated method, but is much more time consuming and cannot be used on some materials. This test is also non-quantitative. It consists of measuring the angle of contact a drop of water assumes on a part surface.
OSEE (Optically Stimulated Electron Emission) is quantitative, but associated equipment can be QUITE pricey. OSEE uses UV light to stimulate electron emission which is measured as current.
There are more methods available, but we use water break for our production processes. Quick, easy, and we get clean/unclean indication in 30 seconds.
Aerospace - Dayton, Ohio, USA
A. Kevin
First you must clarify the question. Parts for tin plating must be cleaned. This is verified by the water break test as described by the previous answers. This should be routine plating practice unless the parts are small and/or are barrel plated when the test becomes impractical. If parts are not clean at this stage, they may fail during soldering (since the tin is effectively dissolved in the solder) or the plating adhesion can be poor leading to blistering, etc.
On the other hand, if the surface of the plated tin is contaminated it may also fail solder tests. This could be due to poor rinsing after plating, poor packaging, storage conditions, etc. Testing for a clean surface will not help here - a rosin fluxed surface will always fail water-break but can be perfectly solderable.
Solderability tests are often specified for PC components and range from a simple dip test to a 'Meniscograph'
Hope this helps,
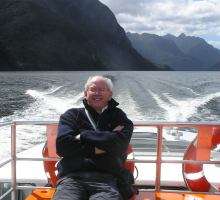
Geoff Smith
Hampshire, England
Multiple threads merged: please forgive chronology errors and repetition 🙂
Test to monitor cleanliness in electroplating
Q. Our company runs a nickel-chrome electroplating line. We encounter plating problems traced back to cleaning, but currently we don't conduct any test on the cleanliness of our parts prior to plating. Is there any std test that we can conduct? Is this test supposed to be incorporated in the process, without affecting the quality of plating? or should it be done on interval basis only?
Thank you very much.
industrial engineer - Cavite, Philippines
May 14, 2009
![]() |
A. There are a lot of different opinions about this. I do not know of a simple practical check other than a water break test. Typically, you find a cleaning process that gives the desired water break check and then stay with that process till something fails. It can be a quick check on frequent parts IF the process is compatible. An example-A highly silicated caustic cleaner forms a very difficult film on the part if allowed to dry. - Navarre, Florida A. Probably the easiest test is the water-break test. Essentially, after the cleaning process is completed you inspect the surface of the parts after final rinsing, before plating for a surface where the water stays in a continuous film for about 15-30 seconds. If the film remains unbroken then continue with the process, if the film breaks or forms droplets on the surface there is still surface contamination and you need to repeat the cleaning operations. Brian TerryAerospace - Yeovil, Somerset, UK |
Parts pass at first, then fail days later
Q. I am a manufacturing engineer for a company that makes sensors for the aerospace industry. We ultrasonic clean and 2 stage rinse the parts to achieve the clean surfaces we need. After the rinse steps, the parts pass a water break test, but if the parts are retested a few days later, they will fail. The parts are just being stored in bins and are not being handled or processed in any way. I cannot account for this. Any ideas?
Mike MellingerEngineer - Moorpark, California, USA
September 27, 2010
![]() |
A. Cleanliness does not last indefinitely. Parts may get dirty, passivated or oxidized later on. Unless they are immediately stored under vacuum and no-touch conditions the environment will certainly count. G. Marrufo-Mexico Guillermo MarrufoMonterrey, NL, Mexico A. Guess number 1 is the water break water is contaminated. - Navarre, Florida A. Common problem to old time platers. On the first water-break test the surfactant from the cleaner is still on the parts, days later it has dried and causes the water break. You must get the surfactant completely off before you "water-break test", try hot water rinse, try an acid dip, and then another rinse, talk to the cleaner supplier about how to get the surfactant off. ![]() Robert H Probert Robert H Probert Technical Services ![]() Garner, North Carolina ![]() |
A. The type of part to be cleaned could be an issue as well. Typically cast iron or aluminum parts tend to hold soils deep within the pores of the substrate. Over time and with varying temperatures these soils can seep out of the metal pores.
Joseph Beckley- Bloomington, Indiana USA
October 27, 2010
Q. How are you~~
I'm doing university research on hydrophobic surfaces.
My first question is what is the difference between superhydrophobic and hydrophobic?
and
How are superhydrophobic and hydrophobic contact angle on surface measured?
- Norman, Oklahoma, USA
December 5, 2012
Q, A, or Comment on THIS thread -or- Start a NEW Thread