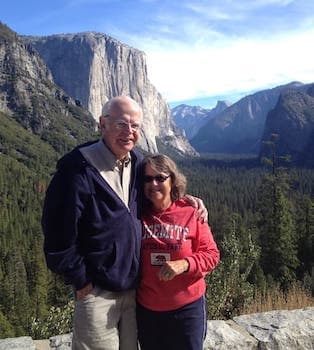
Curated with aloha by
Ted Mooney, P.E. RET
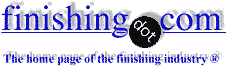
The authoritative public forum
for Metal Finishing 1989-2025
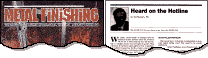
-----
Blister Problems in Cu-Ni-Cr on Diecastings
We are in locks mfg. business. We are using Zinc Diecastng material for Copper-Nickel-Chrome Plating of locks components. Recently we are facing the problem of heavy blisters on Zinc Diecasting components. In bare material casting blisters or porosity is not visible. Kindly help in this matter.
Thanks,
- India
2006
My telepathic skills are severely lacking today and I can't visualise what process you are using. Neither can I see your parts in my mind, so I don't know what magnification you use to inspect for porosity. Nevertheless, the most common reason for blistering is porosity, so I suggest you go through the cleaning process and take a sample before the diecast would be plated and look for porosity then. I will wager you will see some porosity now.
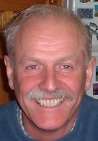
Trevor Crichton
R&D practical scientist
Chesham, Bucks, UK
2006
2006
Dear Mr. Rajendrakumar Mudholkar,
You have not mentioned the stage at which blistering occurs.
Mostly it occurs either at the cleaning stage or in cyanide copper bath.First of all check your cleaning system. There should not be any trace of oil/dirt before your articles enter into a Cyanide Copper bath.
Secondly, zinc die casting parts require a heavy thick coating of Copper, make sure that you are using a Rochelle Copper bath which increases the speed and gives thick deposits. This is a two stage step - A strike copper bath and the next to main Copper bath. Check for anode corrosion at both the stages - and that the anodes are clear and that they do not have a greenish/ black film at the time of plating. If this occurs check for free cyanide. Also check copper metal content. Temp. should be around 50 degrees C. and not more than this. If this happens install cooling coils. pH also plays an important part in this bath. Adjust the pH between 9.5-10.5. Lastly but not leastly you can check for all the connections starting from rectifier till the bath and remove carbon if found. This bath also requires continuous filtration.
All the above rectifications shall help to seal porosity if any.
After this stage rinse thoroughly in D.M. water and give an Acid dip rinse again thoroughly before entering into Acid Copper/Nickel Bath.
Check for traces of oil in nickel bath and run carbon continuously.
I hope this will eliminate your blistering problems.
Best of Luck,
- New Delhi, India
2006
Good Day,
these parts getting mechanically polished before they get plated?
Regards,
- Mexico City, Mexico

Q, A, or Comment on THIS thread -or- Start a NEW Thread