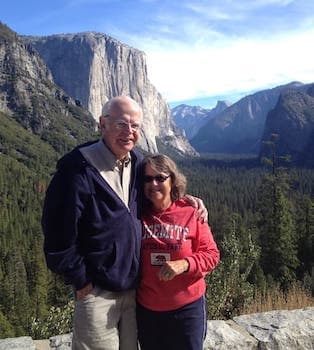
Curated with aloha by
Ted Mooney, P.E. RET
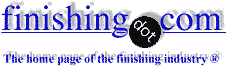
The authoritative public forum
for Metal Finishing 1989-2025
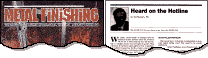
-----
Better racks/jigs to reduce plating defects
Q. Wire Selection for part wire-up for plating, electrolytic plating? Can anyone recommend some literature covering the topic of selection of wire for part wire-up for plating, especially electrolytic plating?
I'm educating myself, but it seems there can be a few reasons to choose aluminum or copper or CRES wire, including avoiding contamination of the tank, power from the rectifier going through the wire (amps? - DIA and material), cost, etc.
Thanks in advance.
- Paso Robles California
May 20, 2021
A. Hi Glenn. Production platers usually use custom-designed plastisol coated plating racks, usually made mostly of copper, but often with stainless steel spring clips or tips ... reserving 'wiring' for special situations.
There is a good chapter on the subject in the old but reliable Electroplating Engineering Handbook.
When parts are wired, copper wire is usually used because it's conductivity is 15X to 25X the conductivity of stainless steel. And aluminum wire is not much used because unreliable contact can be a problem, and it's not resistant to the strong caustics that are part of most plating cycles.
Electricians generally consider 14 gauge copper wire good for 15 Amp circuits, and 12 gauge good for 20 Amps. That's probably a rather conservative estimate for this application, but it should give you a starting point.
Luck & Regards,
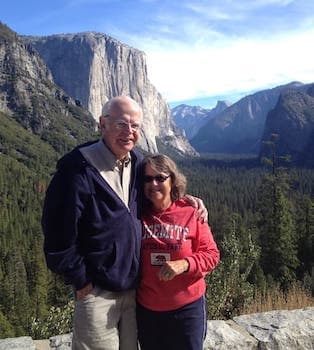
Ted Mooney, P.E. RET
Striving to live Aloha
finishing.com - Pine Beach, New Jersey
May 2021
⇩ Related postings, oldest first ⇩
Q. I was using a jig for hand tools in the nickel tank for the past 2-3 weeks. But the result is not at all satisfactory. This is because the rejection rate is very high because, where the jig holds the tool, at that spot I am repeatedly getting a yellow spot and the nickel doesn't get coated there.
So I would like help in this regard and would like suggestions on the design and the material of the jig to be used. Also please specify what are the required current, nickel requirements in the tank which uses approx. 32 jigs in one go?
if this jig is successful, it would increase the efficiency many fold.
student- engineer - Punjab, India
2006
A. You can use Teflon coated hangers for hand tools. It is definitely helpful to avoid chrome yellow mark.
Vikas Shrama- Gurgaon( haryana), India
2006
Q. I have the same problem. I used jigs that are plastisol coated. Would you give me any more about Teflon ?
Thank you
- BANGKOK, THAILAND
2006
A. Any place that the jig touches is going to leave a mark so the whole idea is to have the contact point as small as possible and still carry the load. The next way is to insulate the jig to as close as possible to the actual contact point that it does not serve as a robber or thief. It can not be so large that it shields the part or you will get very thin or no plate. Professional jig makers will use copper to carry the main load and plastisol coat it so that it does not plate. Smaller coated copper will be used to carry the feeder loads and finally very short spring clip attachments might be made of stainless steel with these using a very thin insulator coating.
The best method is to make the contact point where it will not show when the tool is assembled. The rack (jig) may be a lot harder to build, but it will save a lot of grief.
- Navarre, Florida
2006
Q. HELLO SIR,
WE ARE USING NICKEL CHROME PLATING IN HAND TOOLS, BUT WE ARE FACING PROBLEM OF YELLOWISH IN CHROME IN PLACE OF WIRE WHICH BINDS THE PRODUCT.IF WE USE JIG OR FIXTURE THE PROBLEM DOES NOT DISAPPEAR......PLEASE SOLVE THE PROBLEM
PLATING SHOP EMPLOYER - INDIA
March 21, 2011
A. Hi, Sanjay.
This happens because the chrome plating is attracted to, and deposits onto, the wire. Chrome has terribly low throwing power. The previous answers tell the sad story that you can't solve this problem of poor racking by altering the solution chemistry, only by correcting the poor racking so there are no wires on the significant surfaces. If you use racks, be sure to insulate the ends of the hooks, removing insulation only where absolutely necessary for contact. Good luck.
Regards,
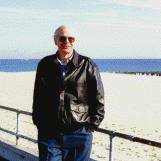
Ted Mooney, P.E.
Striving to live Aloha
finishing.com - Pine Beach, New Jersey
March 21, 2011
Q. When plating nickel/chrome on racks the plating parts have visible nickel in area where the parts are connected on racks. On that area there is no chrome plate. Does anyone knows how to minimize this?
Bojan Koren- Bovec, Slovenia
September 5, 2015
A. Bojan, sorry to know of your difficulty. This is a very common concern and there are no easy answers. Two solutions that I have used in the past: 1. Rack the parts "loosely" so that they can move a bit but not too much to cause damage. The rack tips may need to be dulled or adjusted to allow for this. 2. Process the given items "halfway" or so then pull the parts out, adjust the positioning on the rack so that the parts are moved from their original positions and then continue. Obviously, #2 is not a preferred solution but it can be quite effective.
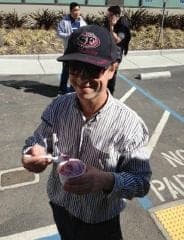
Blake Kneedler
Feather Hollow Eng. - Stockton, California
October 28, 2015
Preventing damage to plating racks
Q. My question is what are the possible reasons of damage of jigs during electroplating and how can I minimize it?
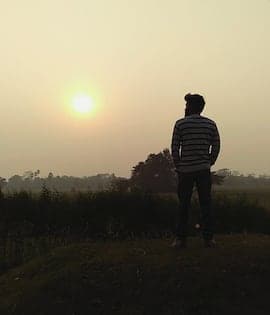
Piyush Kumar
- Chennai, India
May 19, 2019
A. Hi Piyush. There are 1001 things that can damage plating racks, but from many years of visiting plating shops where racks were well maintained vs. poorly maintained, I'd say the single most important thing you can do is issue an order that plating racks must always hang from their hooks, never be allowed to rest on the floor. The concrete floor will damage the plastisol coating and cause "trees", the weight will bend the hooks near the bottom, people will allow them to get entangled and then damage them when separating, they'll lean against each other and against corners to get further bent and scraped, a whole stack will fall over ...
Regards,
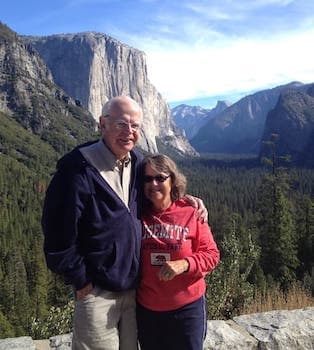
Ted Mooney, P.E. RET
Striving to live Aloha
finishing.com - Pine Beach, New Jersey
May 2019
Q. Sir,
I'm Varun from Om Enterprise Rajkot. I search more about jig fixture coatings like "plastisol". What is proper technology for coatings? We don't know how to coat plastisol on jigs. Give solutions for this and where we can buy this.
- Rajkot, Gujarat
February 17, 2021
A. Hi Varun. Generally, plating shops do not do plastisol coating of their racks. This is a service generally done by rack manufacturers and plating equipment suppliers. I worked at a plating equipment manufacturer who did it, but never did it personally so I don't know all the fine details -- but it was generally as follows:
All loose plastisol that could be removed was cut off with box cutters, etc., and pulled off. What was too adherent would be burned off in an oven. Then the component would be solvent cleaned, then a primer / adhesion promoter was brushed on, then the component was dipped in a vat full of plastisol, then it was baked.
I'm sure there are rack manufacturers and equipment suppliers who can offer he service to you. Touch-up can be done with air-dry plastisol formulations but it is not nearly as satisfactory as bake-cured.
Luck & Regards,
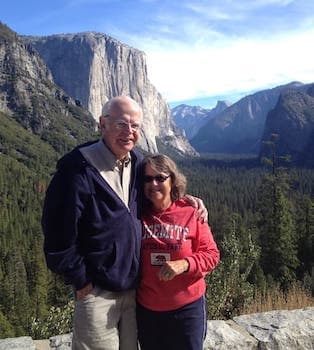
Ted Mooney, P.E. RET
Striving to live Aloha
finishing.com - Pine Beach, New Jersey
February 2021
Q, A, or Comment on THIS thread -or- Start a NEW Thread