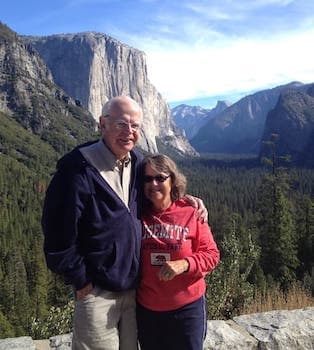
Curated with aloha by
Ted Mooney, P.E. RET
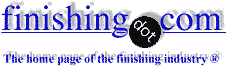
The authoritative public forum
for Metal Finishing 1989-2025
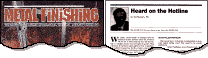
-----
Black anodised parts turn red in light
Q. Hi, my name is Michel and I'm a trainee (industrial engineer) for a lighting plan in Québec (Canada). We receive some black anodised (organic) parts from our supplier. The problem is that the parts turn red after being exposed to the light (50 watts halogen). It happens within 7 days of exposure. I would like to know which aspect I should consider first to solve this problem. Thank you for your support. Sorry for my written, English isn't my first language.
Michel Champslighting industry - Montréal, Québec, Canada
2006
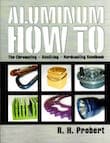
Aluminum How-To
"Chromating - Anodizing - Hardcoating"
by Robert Probert
Also available in Spanish
You'll love this book. Finishing.com has sold almost a thousand copies without a single return request :-)
Treatment &
Finishing of
Aluminium and
Its Alloys"
by Wernick, Pinner
& Sheasby
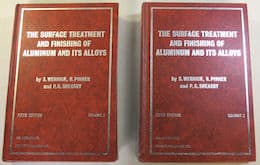
(note: this book is two volumes)
on eBay or
AbeBooks
or Amazon
(affil links)
![]() |
A. Michel, metal finishing - San Jose, California, USA A. Black dyed anodize typically turns purple from UV light, but an off red is certainly possible. The organic dyes that are sold have a variable amount of fade resistance by different manufacturers. I doubt if any will live in your use. Some might last a few weeks rather than hours, but will still fail. Hard anodize is thicker and is a grey to dark grey might be an option. Color can vary from week to week, so that might not be a viable option. Your best shot will probably to go to a two step or architectural anodize. True blacks are not easy to get, but there is a palette of colors available. James Watts- Navarre, Florida |
![]() |
A. Most black dyes have good light resistance, so the first culprit is a poor seal. After that, consider (more or less in order) the quality of the day (most, not all, black dyes are good - some are awful but cheap) and the thickness of the anodize (a thicker coating allows more dye to absorb and thereby requires more time to fade. I like 8-12 um). Compton, California, USA A. The two most important causes are sealing and dye colorfast for anodized Aluminum. Dayton, Ohio |
A. Hi, there are two ways may be helpful
A. Change your black dye to high light fastness dyes. please contact with your local dye supplier for help, Clariant (Canada) Black MLW as an example. Some of these dyes has eight plus light fastness for architecture. You can check.
B. Make a little change on your production line. Use two-step sealing can increase the light fastness dramatically. Cold sealing firstly and Mid-temperature sealing later. Although some bleeding would happen when cold sealing working.
- China
Q, A, or Comment on THIS thread -or- Start a NEW Thread