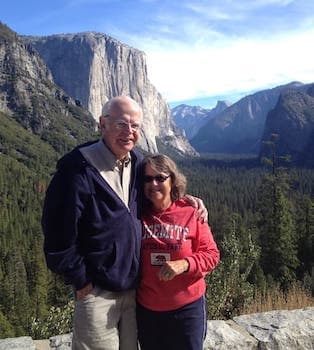
Curated with aloha by
Ted Mooney, P.E. RET
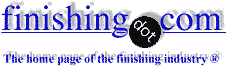
The authoritative public forum
for Metal Finishing 1989-2025
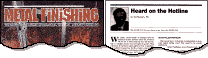
-----
Effect on surface finish of zinc phosphate coating
Q. I would like to know the reason for change in surface finish after zinc phosphate coating. Does it always increase or may it decrease?
Rajib Kumar Duttabearings - Jamshedpur, India
2006
A. The finish is bound to change once zinc phosphate is formed on the MS Surface; strip away the phosphate to get back the base steel finish. What do you mean by increase/decrease?
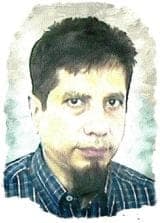
Khozem Vahaanwala
Saify Ind

Bengaluru, Karnataka, India
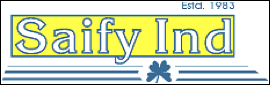
2006
A. Dear Mr. Dutta,
Zinc phosphate coating is a conversion coating. The surface finish and roughness will vary after phosphating.
The acid pickling done before phosphating might also induce some change in roughness of the substrate.
If you want to achieve a low Ra value then you have to use some grain refiners in the phosphating bath.
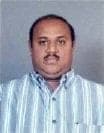
T.S.N. Sankara Narayanan
- Chennai, Tamilnadu, India
(ed.note: The good doctor offers a fascinating blog, "Advancement in Science" )
2006
A. Dear Mr. Dutta,
Variations in conditions are solely responsible for phosphate surface finish. Only thing you have to determined the suitability of various changes like acid pickling, caustic or non-caustic degreasing, pre-dip activation etc.
Thanks,
- New Delhi, India
2006
A. If you mean the increase and decrease in the phosphate layer in steel surface from time to time there are many reasons for that:
you should keep the concentration of your phosphate tank all the time in the standard values,
the degree of temperature must be limited,
the exposure time in the tank must be the same all the time,
you must analyze your tank two times during one shift; keep all points in standard limits,
your basic steel metal must be standard and from one suppler not change from time to time.
- Cairo, Egypt
2006
Phosphating make hydraulic block rough and damages O-rings
Q. Generally we make hydraulic valves, blocks, filters in company.
We have now face some coating issue in the blocks. Our requirement of bore area is Ra value 1.6. but do not achieve that Ra value after phosphate coating. And this damages O-ring areas when hydraulic valve is assembled in the bore area.
Anybody please tell how to rectify that problem?
Can you please tell me if Ra value achievable in the blackening process is better than in Phosphate?
Design Engineer - coimbatore, Tamil Nadu, India
April 8, 2014
Q. Hi,
we are carrying out zinc phosphating process for our valve manifold blocks. The material of these blocks is SG Iron made by centrifugal casting. We carry out grinding of these blocks and achieve Ra value between 0.4 to 0.8 microns. But, after phosphating, this value increases to more than 1.0 micron, leading to oil leakage from these blocks.
I want to know if I am doing something wrong with my zinc phosphating process which is leading to change in Ra value.
- Ahmedabad, Gujarat, India
April 1, 2016
A. Hi Joseph. TSN tells us, above, that a grain refiner will minimize this problem. Are you using one? Is this a proprietary zinc phosphate process you purchase, or something cobbled together in-house?
Regards,
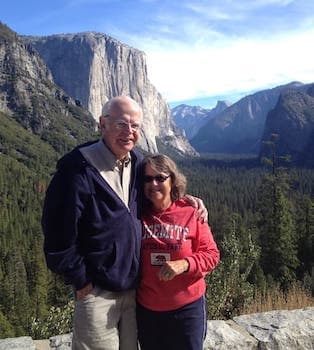
Ted Mooney, P.E. RET
Striving to live Aloha
finishing.com - Pine Beach, New Jersey
Q, A, or Comment on THIS thread -or- Start a NEW Thread