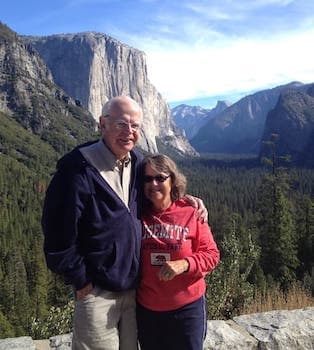
Curated with aloha by
Ted Mooney, P.E. RET
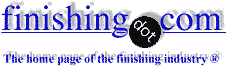
The authoritative public forum
for Metal Finishing 1989-2025
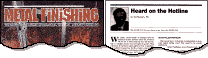
Thread 415/78
Hydrogen Embrittlement Failure. Details for Chromium Plating Baking
Q. Hello, please could someone explain more about the hydrogen embrittlement test for chromium. Is it possible that the specimen of notch ASTM F519 for chromium fails or broken at a load less than the 75% of the ultimate load Stress? For example the material of the specimen has about 16,000 psi ultimate load Stress and the ASTM requires to test at 75% of this load for 200 hours but what happen if the specimens break While you are loading to reach the proper load I mean at a time equal zero.
Additionally, what happen when you have a bath with a concentration of chromic acid 241 g/L and sulphates 3.4 g/l. I mean a ratio about 70. Could this composition cause hydrogen embrittlement?
- Peru
July 14, 2023
publicly reply to K Cho
A. 70:1 Cr to sulfate ratio is not ideal. I try to maintain as close to 100:1 for peak efficiency. However, I don't believe a 70:1 ratio would be a contributing factor to embrittlement.
The only time I've seen a failure on loading (0 hour) was when the called out hydrogen embrittlement relief bake was inadvertently missed. We implemented a second set of eyes required for signing off on embrittlement relief bake time in/out of oven, bake soak duration and temperature. Haven't had a failure since.
Chemical Processing Team Leader - Mesa, Arizona
publicly reply to Brian Bynum
⇩ Related postings, oldest first ⇩
Q. We have a T shaped small component called a Choke Block. This block rotates in a steel fork bore & works in an abrasive environment like dust, carbon soot, and dampness. Presently it is carburised & hardened. However I want it Chrome plated to improve wear resistance & prevent rusting/corrosion. My questions pertain to this situation & need the clarification on the same.
What is the threshold thickness value for hard chrome plating & decorative chrome plating ? Does component needs to be hardened before hard chrome plating ? What is the advantage of hardening a component before hard chrome plating ? Does hard chrome layer of 15 micron work well in abrasive condition? What is mean by chrome flash ? What test is used to detect Hydrogen Embrittlement?
Rajesh TalathiQuality Engineer - Pune, Maharashtra, India
2004
publicly reply to Rajesh Talathi
for Engineers, Specifiers, and Shops
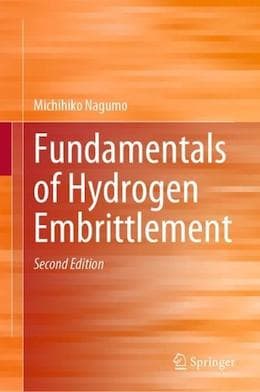
avail from eBay, AbeBooks, or Amazon
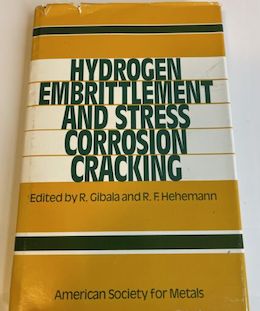
avail from eBay, AbeBooks, or Amazon
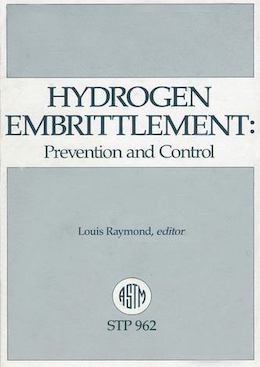
avail from eBay, AbeBooks, or Amazon
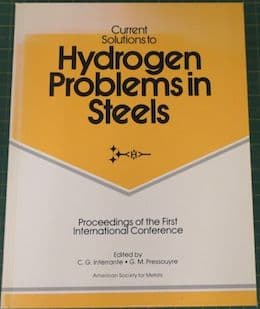
avail from Amazon
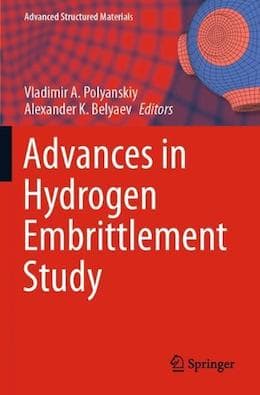
avail from eBay, AbeBooks, or Amazon
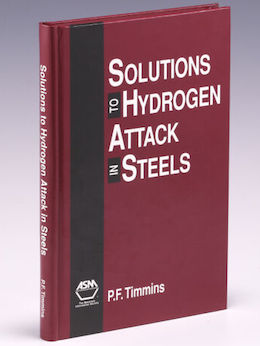
avail from eBay, AbeBooks, or Amazon
(as an Amazon Associate & eBay Partner, we earn from qualifying purchases)
A. Dear Mr. Talathi,
I hope someone else will answer your questions. I can only give you some informations about our use of chrome (we use chrome in abrasive environmental too: chrome vs melt glass). The thickness value for hard chrome is usually 6-8 micron but we can work without problems with 15 micron too. I know that an hardening of components before hard chrome planting can give a bad adherence of chrome.
Q. Finally I've got a question for you: Do you think that Hydrogen, occluded into hard chrome, is able to influence layer's hardness or wear resistance?
Best regards,
- Fidenza, Parma, Italy
publicly reply to Luca Tosini
A. Mr. Tosini,
Lab research has demonstrated that not only Hydrogen but also Oxygen dissolved in the chrome layer have the highest influence on hardness. Vacuum treated Chrome to eliminate these "impurities" has a hardness of only 400-500HV instead of 1000-1100HV.
Guillermo MarrufoMonterrey, NL, Mexico
publicly reply to Guillermo Marrufo
Q. Thank you Mr. Marrufo
Do you think that a simple thermal treatment at 500-550°C could help me to increase wear resistance? (at about 500-550°C Hydrogen leaves Chrome that passes from hexagonal to cubic structure).
Best regards
Tosini Luca- Fidenza, Parma, Italy
publicly reply to Tosini Luca
A. Generally, chrome with hardness above 1,000Kg/mm2 is BCC, whereas hexagonal structure is found in softer plates. Your proposed heat treatment of chrome above 400 °C will eliminate Hydrogen but very little Oxygen. With this treatment hardness may drop up to 30% due to recrystallization, stress relieve and grain growth. Now, it is important to say that hardness is not a linear function to wear resistance.
Guillermo MarrufoMonterrey, NL, Mexico
publicly reply to Guillermo Marrufo
A. Why are you baking the part at such a high temp? "Normal" bake temp is 375 to 450 °F, not °C. Why do you think that you have a hydrogen embrittlement problem? You can prevent most of any hydrogen embrittlement by simply not etching or pickling it as long. Also, you can avoid sharp corners by employing generous radius on all corners. You can also shot peen before plate. You can also pre-bake. You can extend the length of the bake. You can get it into the bake oven quicker after it comes out of the final rinse.Far too many people have heard of hydrogen embrittlement, so blame every failure on it. It is not Cyanide or Cancer, but far too many people are finding goblins under their bed at night when there are none. In short, make sure that you have a problem before you waste time, money and energy trying to fix it. PS , notch bar testing is the common way to check for a problem. Destructive loading of a part is wonderful if it physically lends itself to the testing.
James Watts- Navarre, Florida
publicly reply to James Watts
A. Mr Talathi,
I suggest the following sequence:
1) Clean in an alkaline soak cleaner at 70 °C for 4-6 minutes.
2) Anodic clean at 75 c for 2 Minutes
3) Rinse well twice
4) Check if Rust is present . Anodic de rust in a de-rusting solution. This is alkaline and runs 75 centigrade anodically and is available domestically.
5) rinse twice plain city water
6) neutralise in 5 % dilute sulfuric for 30 secs.
7) Plate Sulfur Free Semi Bright Nickel.. 6 to 10 Microns Dragout + two rinses. ( NOT BRIGHT NICKEL please NOTE)
8) Dilute Chromic dip or dip in Chrome dragout.
9) plate Chrome as usual to regular thickness.
10) drag-out and two rinses
11) Hot Deionised water rinse at 90 °C for 1 Min immersion.
Air dry and replace the DI water daily. The Hydrogen Embrittlement will be present for academic purposes in the part. The Nickel will eliminate corrosion failure.
Best for performance.. Good Luck
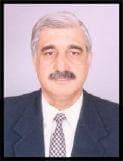
Asif Nurie [deceased] [deceased]
- New Delhi, India
With deep sadness we acknowledge the passing of Asif on Jan 24, 2016
publicly reply to Asif Nurie [deceased]
Multiple threads merged: please forgive chronology errors and repetition 🙂
Q. I am Design engineer dealing in defense-related product design & development. I use a product which is Cadmium plated and that is failing during tensile load. My customer is asking to perform hydrogen de-embrittlement. I would like to know what is hydrogen de-embrittlement? Why this needs to be conducted and how? After which are the process / treatments this process to be conducted?
Viswanath RDesign Engineer - Bangalore, Karnataka, India
2004
publicly reply to Viswanath R
A. The only de-embrittlement I've heard of consists of baking the part for up to 23 hours at roughly 375 °F within a few hours of the operation that caused the embrittlement. This is necessary for hardened steels that have been subjected to any processing which generates atomic hydrogen; that processing would include not only the cadmium plating itself, but cathodic pre-cleaning processes and acid activation processes as well. It may be best to blast the components rather than chemically cleaning them.
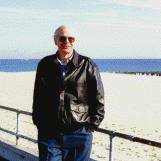
Ted Mooney, P.E.
Striving to live Aloha
finishing.com - Pine Beach, New Jersey
publicly reply to Ted Mooney
A. The first question to ask is does an unplated part fail the load test. If so, plating has nothing to do with it! Since this is defense related, the specifications should mandate the post plate bake. Now for the practical side of the problem, most hydrogen embrittlement is caused by an excessive etch cycle prior to the plate. For post plate bake, the secret is to get it into the bake oven as soon as possible after the final rinse in the plate cycle. I insisted on under 15 minutes if it was a critical or complex geometry or very hard part. Some parts only require 4 hours at 375 ° F. Some parts require a preplate heat treat. Some parts require a shot peen step to a given and verified intensity prior to plate.
James Watts- Navarre, Florida
publicly reply to James Watts
A. As Mr. Watts stated, this information should already be in your plating specifications. If not, download AMSQQP416 F PLATING, CADMIUM (ELECTRODEPOSITED).
Ken Vlach [deceased]- Goleta, California

Rest in peace, Ken. Thank you for your hard work which the finishing world, and we at finishing.com, continue to benefit from.
publicly reply to Ken Vlach [deceased]
A. Dear Sir,
With worldwide rejection of Cadmium, and a move toward alloy plating, it would be worthwhile if you could get the spec changed to zinc-iron plating.
Best regards,
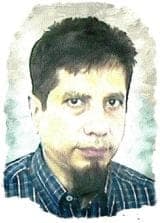
Khozem Vahaanwala
Saify Ind

Bengaluru, Karnataka, India
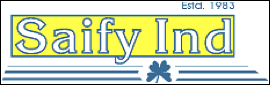
publicly reply to Khozem Vahaanwala
A. Hydrogen de- embrittlement is the release of trapped hydrogen under hard chrome plating. The hydrogen is a by-product of the chrome plating process. To remove, place into a continuous furnace @ 300 °C for 2.5 hours and water quench to room temp. If hydrogen is not removed, potential for parent material substrate to fail under extreme circumstances.
Andrew Private- Adelaide South Australia, australia
September 20, 2012
publicly reply to Andrew Private
Multiple threads merged: please forgive chronology errors and repetition 🙂
Q. I work in a chemistry lab responsible for analysis of chromium plating baths. We also have a lab in-house that performs hydrogen embrittlement for process checks. Recently, we had a failure in the hydrogen embrittlement test, and yet our chemical analyses (Hex. Cr, Trivalent Cr, sulphates, surface tension and chlorides) show that it is within specification. One thing we have noticed is that the colour of the bath has changed. It is now almost black and you cannot see through it anymore.
Would anyone know a reason that would cause such a failure?
chemistry lab tech - Winnipeg, Canada
2006
publicly reply to Jennifer Friesen
![]() |
A. Hydrogen embrittlement from chrome plating has little to do with the bath composition. High strength steels will always embrittle to some extent during hard chrome plating. Are you baking after plating? Bake should start within one hour of plating and continue 4 hours @ 375 °F. ![]() Jeffrey Holmes, CEF Spartanburg, South Carolina publicly reply to Jeffrey Holmes, CEF A. Possibly related, but not guaranteed. I strongly feel that more embrittlement is caused by the etch cycle than the plating cycle. - Navarre, Florida publicly reply to James Watts A. Dear Jennifer ![]() Vikram Dogra Irusha India - Chandigarh, India publicly reply to Vikram Dogra A. Hi Jennifer, - Mexico City, Mexico publicly reply to Dominik Michalek |
Thank you all for your responses.
I think there is consensus (from this page and from our discussions in the lab) that it is most likely metal contamination. We currently do not have a method for the analysis of Cu and/or Fe in chromium solutions, however do have an ICP-OES that I believe would be capable of handling the testing. Does anyone have any other suggestions?
Chem Lab Tech - Winnipeg, Canada
publicly reply to Jennifer Friesen
A. Jennifer,
what also will be helpful is to measure the conductivity of the chrome solution, it should be above > 350 mS/cm, is just a quality test.
Regards,
- Mexico City, Mexico
publicly reply to Dominik Michalek
Multiple threads merged: please forgive chronology errors and repetition 🙂
Hydrogen De-embrittlement after hard chrome plating
Q. We hard chrome plate bearing diameters approx. 35-55 mm dia. both in bore and on OD to restore oversize/undersize bearing diameters. Finished thickness after final grinding is approx. 40-100 microns.Now my questions are:
1. Is there any suggested / recommended limit to the thickness of chrome plating for salvaging such worn out bearing diameters? The bearings and their seats have no relative motion once they are pressed into/onto their seats.
2. What is suggested/ recommended surface finish for such bearing seats. Pl quote any standard if it exist.
3. These bearing seats are of material 30 KH GA SA ( as my customer puts it ) and claims it to be a high tensile alloy. They are rings pressed into aluminium housings.
Is it desirable to do Hydrogen De-embrittlement? If yes at what temp and how much time? Will it not effect or distort the outer housing. (The rings are pressed and a pin punched in, hence it cannot be removed from housing). Since there is no direct tensile / twisting load onto the bearing surface, is Hydrogen De-embrittlement still recommended. We have been restoring such bearing surfaces without any failure(In use) for quite some time now, but my customer has suddenly asked me to meet this requirement. So I wish to seek expert opinion.
These are air borne components and I would myself not like to risk human life for a small cost.
THANKS FOR YOUR VALUABLE ADVISE AND TIME IN ADVANCE...
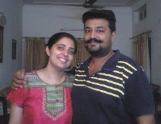
Vikram Dogra
Irusha India - Chandigarh, India
December 8, 2011
publicly reply to Vikram Dogra
A. After chrome plating, in 2 hrs, you can go to oven for 190&plmn;10 °C for 2 hrs if the hardness is 42 Rc
regards
- Istanbul, Turkey
publicly reply to Dr. Halim Polat
A. I agree with Dr. Polat, although I have seen (and written) specifications that require baking after plating for parts that are Rockwell C 35 and above.
Among the specifications that address baking after electroplating are AMS2759/9 and ASTM B850-98. Those documents also agree with Dr. Polat, calling out 190 °C or 375 °F for an hour.

Lee Gearhart
metallurgist - E. Aurora, New York
publicly reply to Lee Gearhart
A. Dr. Polat is right in his recommendations.
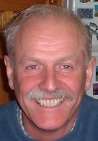
Trevor Crichton
R&D practical scientist
Chesham, Bucks, UK
publicly reply to Trevor Crichton
A. BAKING AFTER PLATING:- PLATED PARTS WHICH HAVE HARDNESS OF 40HRC OR ABOVE SHOULD BE BAKED AT 190 ± 14 DEGREE C FOR 4H . PROCESS SHOULD BE STARTED IMMEDIATELY AFTER PLATING.
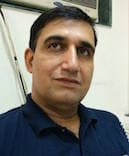
Ajay Raina
Ludhiana, Punjab, India
publicly reply to Ajay Raina
Q. Thanks friends for your valuable information on hyd. emb. but my other questions still remain unanswered....
Any expert opinion ???
THANKS
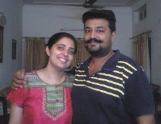
Vikram Dogra
Irusha India - Chandigarh, India
January 7, 2012
publicly reply to Vikram Dogra
Multiple threads merged: please forgive chronology errors and repetition 🙂
Q. Hi, I am trying to find out what kind of times/ temperatures for de-embrittling, as well as general input/feedback about the process would be great.
The material is EN8 steel, finish: Zinc plated (between 5-8 microns) on a housing component around 50 x 50 cm.
Some say don't bother some boil it for a century for this material!
Any thoughts?
- Manchester, UK
April 4, 2014
publicly reply to Jem Mosley
A. Embrittlement relief is normally specified by the spec or the company you are doing it for.
Normally, it is dependent on the hardness.
Boiling is nowhere a high enough temperature to effect a de-embrittlement.
The proof is verified by doing notch bar testing.
- Navarre, Florida
publicly reply to James Watts
A. I believe that the information you seek is in ASTM B850-98-98(2009) "Standard Guide for Post-Coating Treatments for Steel for Reducing the Risk of Hydrogen Embrittlement." They advisedly use the term 'reducing' rather than 'eliminating' for reasons discussed in the standard. There are also non-embrittling processes such as phosphate and oil and phosphate and paint, and, for those who require sacrificial protection, mechanical plating and zinc-rich paints.
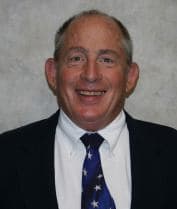
Tom Rochester
CTO - Jackson, Michigan, USA
Plating Systems & Technologies, Inc.

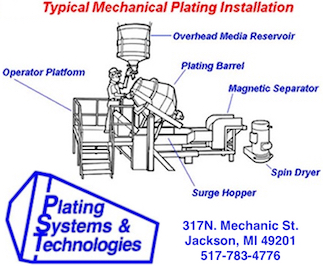
publicly reply to Tom Rochester
A. Hi Jem,
De-embrittlement requirements are usually dependent on either the hardness or the ultimate tensile strength (UTS) of the material.
Pretty much everyone has their own take on what the times and temperatures are for various hardnesses and UTS. If it isn't being specified by your customer you could use AMS2759/9 as a guide.
Aerospace - Yeovil, Somerset, UK
publicly reply to Brian Terry
Q. I am doing hydrogen de-embrittlement baking after chrome plating as per BAC 5709. When baking is under process for this part, oven door is opened multiple times to load and unload another parts. At that time the temperature of oven falls by nearly 150 °C. In such cases, whether the baking time of previous parts is to be increased for that particular time? Is there any reference from any specification regarding this. If anyone has any reference on this kindly suggest.
Shreyashkumar Zingade- Bangalore Karnataka
December 6, 2022
publicly reply to Shreyashkumar Zingade

Q, A, or Comment on THIS thread -or- Start a NEW Thread