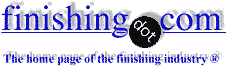
-----
NEED SUGGESTIONS ON HOW TO COST YOUR POWDERLINE OPERATION
Hi experts at Finishing.com! We're a small sheet shop in Western New York that has a powdercoating line. The process is simple...we run a chain-type system around through the wash, drying oven, over to the paint booth where a person with a powdergun applies the powdercoat, the racks hit the oven, and come out the other end. My problem is that we are not capturing the COST for this process. We have a real-time data system where our powderline people log on first thing in the morning and log off in the afternoon. All that really tells me is how long the line was running and how many racks were processed. I don't know what was on each of those racks; could be one or two chair frames or it could be some small angle brackets that hang 100 to a rack. Any suggestions on how to properly allocate that time/material to the proper jobs without going crazy or spending all day every figuring it out? I'm thinking about adding it in to my overhead figure, but there are problems with that too: not all of our jobs require powdercoating, so it wouldn't be an accurate overhead projection for those jobs. I'm not an accountant, so I could really use some real world suggestions. Thanks for your time.
Marion Olick- Cuba, New York USA
2006
Q, A, or Comment on THIS thread -or- Start a NEW Thread