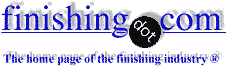
-----
Pretreatment of Steel (Hot Rolled and Cold Rolled)
2006
I would like to inquire of any possible improvements in the pretreatment of steel that we are currently employing. We are planning to scrap our existing plant and create a new one to maximize efficiency.
For hot rolled steel, our current pretreatment process include:
1. Degreasing using soap bath.
2. Rinsing with water.
3. Derusting using concentrated HCl solution.
4. Rinsing with water.
5. Conditioning to remove residual HCl solution.
6. Phosphating.
7. Rinsing with water.
8. Drying as preparation for powder coating.
9. Powder coating
10. Oven baking to set powder coat.
All these are batch processes, with uninsulated, open air vats.
Any input on improvements would be greatly appreciated, even if it means scrapping the whole process altogether.
Thanks in advance.
enclosure fabrication - Cavite, Region IV, Philippines
Ronald Lee
After soak cleaning,you can use anodic cleaner. If you need more cleaning.it is depend upon how much oil & grease in your fabrication work.if you need better cleaning try to use anodic cleaner.
- Shanghai, China
2006
2006
Hi Ronald,
Depending on the requirements of your final product once it has been painted, you may want to consider adding a final rinse stage (also called "seal rinse") after the water rinse which follows the phosphating step.
There are many types of chemistries available, which can passivate, promote paint adhesion, or both.
- Naperville, Illinois
First of two simultaneous responses --
We are currently looking into the possibility of using a brand of all-in-one cleaner to replace our existing multiple stage system. The product claims to be non-hazardous and does not produce heavy metals since it doesn't etch the metal's surface. I have been trying to find a comprehensive review of the product but have been unable to find one. Any inputs would be extremely helpful. =)
Ronald Lee- Philippines
2006
Second of two simultaneous responses -- 2006
Hello
Several notes to improve :
a. Replace Hydrochloric Acid with inhibited Phosphoric Acid , ask your local supplier for such a product.
b. Sealing after Phosphating is almost must. In case you can't , so at least your last rinse will be dionized.
c. In case you decide to remain with HCl , work at 50% concentrated and not fully concentrate HCL. You must add Inhibitor to the HCl .
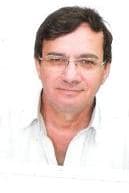
Yehuda Blau
YB Plating Engineering and Quality - Haifa Israel
2006
You line of operation is good.
All you have to do is to ensure whether your pickling is good. Then if possible add another stage in your line before phosphating called Activation. It is slight alkali.
Maintain the free alkali of the bath around 15 with 0.1N sulfuric acid. Also ensure sufficient accelerator (Hydroxyl amine) is available in the phosphating bath. This will solve the problem.
plating process supplier - Bangalore, India
2006
From your inquire I notice that your basic metal is hot and cold rolled steel and your final product is powder coating and you degreasing line is soak ( immersed) method so let us took about the good pretreatment and phosphate line for your conditions
first the stages of the line as following:-
hot chemical degreasing
hot chemical degreasing
hot water rinsing
cold water rinsing
pickling (derusting) HCl 40% with inhibitor use this stage with rusting steel only
cold water rinsing
cold water rinsing
activation before zinc phosphate
phosphate tank
cold water rinsing
di water rinsing
- Cairo, Egypt
Q, A, or Comment on THIS thread -or- Start a NEW Thread