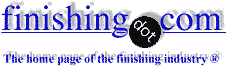
-----
Nickel concentration in bright nickel plating
2006
Over the last 40 years or so all bright nickel solution data sheets have specified a basic makeup of NiSO4 300 g/l 60 g/l NiCl2 H3BO3 40 g/l or thereabouts.
Over the years I have noticed many baths coming in for analysis with much lower nickel concentrations which are still producing seemingly perfect results.
As with zinc plating which changed to a lower metal content years ago, is there a reason for maintaining such a high nickel content in the standard bath?
Unless very high CD is being used or parts have sharp protrusions encouraging burning, I don't see the need for this nickel concentration.
My feeling is that in most cases, a lower metal could be used with no problems and this would lower dragout and therefore waste treatment treatment costs, etc.
My suggestions would be for platers to lower their NiSO4 concentrations by 10% while maintaining their NiCl2 and H3BO3 concentrations and operate for say one month and if they did not suffer burning then lower by a further 5% etc, to find your optimum concentration. If burning occurs on a small percentage of parts decide to either increase the NiSO4 or lower the current on that particular job. Maybe raise the H3BO3 and/or also or the temperature.
Will be interested in the experts discussion on this proposal and encourage experiments in this area.
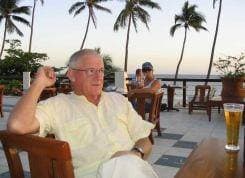
Geoffrey Whitelaw
- Port Melbourne, Australia
It's more complicated than just chemical concentrations. Sure, there are plenty of times when one can operate at a considerably lower concentration. It all depends on temperature, agitation, current density, part shape, etc. The basic formulation as you cite is going to be good for nearly all applications, but is only a general formula, to be modified as appropriate for different installations and parameters.
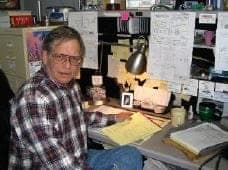
Jeffrey Holmes, CEF
Spartanburg, South Carolina
2006
Q, A, or Comment on THIS thread -or- Start a NEW Thread