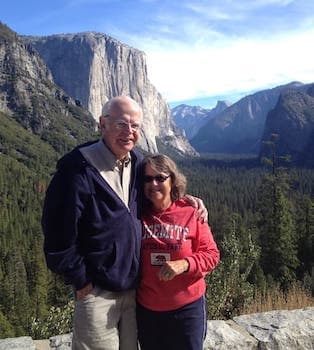
Curated with aloha by
Ted Mooney, P.E. RET
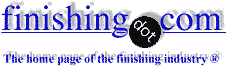
The authoritative public forum
for Metal Finishing 1989-2025
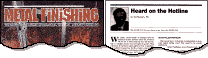
-----
Rusting after powder coating
WE ARE MANUFACTURERS OF FURNITURE AND GET OUR PAINT JOB DONE BY A POWDER COATER. AFTER THE POWDER COATING IS DONE THE RUST BEGINS TO DEVELOP BETWEEN METAL AND COATING AND BUBBLE LIKE THINGS APPEAR WHICH CAN BE EASILY SCRATCHED AND RUST IS VISIBLE. CAN ANY ONE HELP WHAT IS THE CAUSE AND HOW IT CAN BE SOLVED?
SAJJAD MOHAMMADMETAL FURNITURE - KARACHI, PAKISTAN
2006
Hi, Sajjad. You must find a more capable powder coating shop!
It is probable that the shop's pretreatment sequence is completely unsatisfactory. But the shop is supposed to be skilled in this science and to have acquired some years of experience in this art. It is unrealistic to expect that a reader on the internet can, based on a few words of description, advise what that shop with its years of experience has missed. Find a better shop. Good luck, and regards,
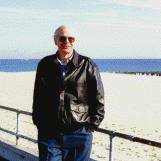
Ted Mooney, P.E.
Striving to live Aloha
finishing.com - Pine Beach, New Jersey
2006
2006
Ted has said it already, but this is a case of inappropriate (or non-existent) pretreatment.
In powdercoating, its far more important what happens before the powder goes on than during or after.
In many cases though, some shops just spray over any surface hoping for the best.
Unfortunately for the unwary, on day one its hard to tell the difference. After a few weeks the difference shows.
An easy test is to ask "what pretreatment will you do?". If you get answers that mention a cotton cloth, or a solvent wash, or pressure washer, or suchlike, find another applicator.
If you hear "iron phosphate" that's good. If "Zinc phosphate", or
"Chromate" that's even better. "Silane" is another good one. If they talk about stages, the more the better up to about 12, but more than
3.
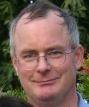
Geoff Crowley
Crithwood Ltd.
Westfield, Scotland, UK
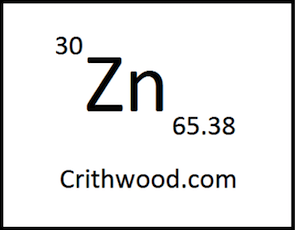
It sounds to me like the coater just pressure washes and lets the parts sit outside to dry. Definitely not a good thing.
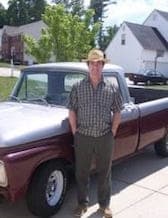
Sheldon Taylor
supply chain electronics
Wake Forest, North Carolina
2006
Dear Sir, I have gone through the letter with problem, actually in making metal furniture there is welding joints in which acid is trapped while rust is removed, in this case the job coater is not properly neutralizing the acid on coating parts before Zinc phosphating, the acid which is trapped inside joints and surface will react with metal and remove the coating from surface and rusted metal is visualized, I suggest after acid treatment they must wash the parts with water at least below 250 TDS mixed with some sodium nitride powder in small quantity.
Zainuddin- Karachi, Pakistan
2006
We are custom metal fabricators and powder coating is called out with increasing frequency. We have a client which represents the lion's share of our powder coating which is a national retail chain in high-end malls. We fabricate their store fronts and sometimes their doors. They like clear powdercoat so the raw steel is visible. For this reason, no blasting or grinding can be visible. The store fronts are different combinations of mild steel square and rectangular tube, flat bar and angle. Sometimes we get some bubbles as described above. I have been given a number of explanations. Outgassing due to residual mill scale seems to be a common theme. We clean all parts with Xylene ⇦ this on eBay or Amazon [affil links] prior to sending them out and individual coaters use a variety of preparation methods. Since blasting is not an option, are there in fact preparation methods which will mitigate or eliminate the bubbling? We aren't comfortable with a single source for anything we outsource but at the same time I need a fairly consistent result from several different powder coaters. If I know what methods will give a consistent result, I can include that process as a specification for the job.
Bruce J. Garwood- Cedar Hill, Texas
2006
Bruce, it really is the responsibility of the coater to do the R&D of the process to eliminate bubbles in the clearcoat if you tell them it's a quality issue and you don't want them there. They shouldn't be raising prices or anything to eliminate the problem because the idea is to make you happy and keep you as a customer.
1). If the problem is the substrate (Base material) the fix for out-gassing is to preheat the parts to a higher temperature than the cure cycle at a longer time period, let the parts cool, and then apply the paint. Any trapped air should have escaped so when the paint is applied and the part is cycled again, there shouldn't be any bubbles.
2). Curing the paint too fast can cause bubbles in clear coat. The lowest temp at the slowest line speed should be used so the bubbles can escape before the paint gels. Cycle times like 450* at 5 minutes sets the paint too fast and trapped air doesn't have time to escape.
3). If one of your coaters finds a paint and/or process that doesn't develop bubbles specify to all of your suppliers that they use the same paint manufacturer and their recommended cycle times.
It usually just takes finding someone willing to put in a little effort to solve this type of problem. "It's residual mill scale" is kind of like saying "I don't want to mess with the problem".
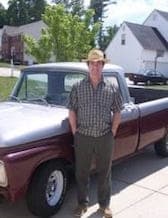
Sheldon Taylor
supply chain electronics
Wake Forest, North Carolina
2006
Sheldon -
I appreciate your information. It confirms what I suspected all along.
Be well,
- Cedar Hill, Texas
Thanks for the helpful response, Sheldon, with a lot of good technical info. But I don't think you'll find many shops that agree with your premise that it is their obligation to develop a workable process (per your intro) and then give it to the customer so he can give it to their competitors (per your point 3).
Rather, I think I would say it's the coater's obligation to both comply with the designer's spec and to deliver a good coating, but that it is not their obligation to reveal what they had to do to deliver that good coating but which was not covered by the designer's specs.
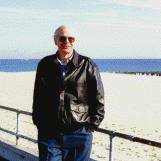
Ted Mooney, P.E.
Striving to live Aloha
finishing.com - Pine Beach, New Jersey
2006
Ted, I guess I was in a "spirit of cooperation" mood with that response. When I was jobbing and a customer asked me why I could run a process that nobody else could I always gave the patented -answer without info- answer, so, guilty as charged. Funny the things you forget when you're away from it for a few years.
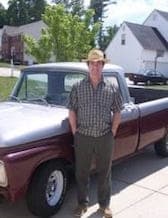
Sheldon Taylor
supply chain electronics
Wake Forest, North Carolina
2006
Dear Sajjad your system needs to be checked. how you are applying the powder?
Jamshaid Asif- Chakwal, Pakistan
November 16, 2009
Dear Zainuddin,
Pretreatment of Items fabricated with pipes should be done with some holes on different appropriate positions of pipes structure to remove all of chemicals when items are drawn out of Baths of each PT Stage (in case of immersion type Phosphatization). These holes will ensure the removal of chemicals from pipe inner spaces. your job coater select any of the PT ( Pretreatment ) system like Iron-Phosphate or Calcium modified Zinc Phosphate. Secondly you can also use an Iron Phosphating system containing molybdate accelerator and a binder like epoxy in it as the active components.
Wish you good luck.
Your Friend....!
powder coating - Lahore Pakistan
May 19, 2011
Q, A, or Comment on THIS thread -or- Start a NEW Thread