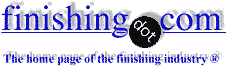
-----
Solutions to Problems in Copper Plating of Printed Circuit Boards (PCBs)
Q. We are using sulfuric acid copper electroplating bath with additives during manufacture of printed wiring board for high-rel application. We want to deposit high ductile copper (more than 18% ductility) with thickness up to 30 microns inside the drilled holes. How to improve the ductility of plated copper during electroplating process itself. Please suggest.
SHRIRAM BHATScientist @ ISRO - Bangalore,KARNATAK, India
January 13, 2022
A. Hello Shriram,
Improving a ductile deposit requires good tank and chemical maintenance. After years of adhering to mil specs for acid copper plating I found that scheduled carbon treatments, tight control of bath chemical analysis, use of DI water only and periodic dummy plating at low current densities enabled us to pass monthly independent lab elongation / ductility tests. You will also want to contact your supplier to make sure the bath you are using meets the requirements you want to acheive.
Retired - WINSTON SALEM, NC
January 18, 2022
Thanks for reply.
Q. What is the frequency schedule of charcoal treatment of bath. Is it depends on total ampherehours or number of processed panels or other else. As per IPC minimum elongation requirement of electroplated copper is 18%.
SHRIRAM BHAT [returning]Scientist @ ISRO - Bangalore,KARNATAK, India
January 21, 2022
⇩ Related postings, oldest first ⇩
Q. Hi,
I would like to ask you about plating the copper to printed circuit board. What kind of solution do I have to use and what condition shall I fulfill. I look forward to your reply as soon as possible. Thank you.
With best regards,
- Bandung, Jawa Barat, Indonesia
2003
A. Hi, Rid. You might start with trying to find a copy of Coombs' Printed Circuits Handbook ⇦[this on Amazon affil links] -- it's the classic for anyone working with printed circuit boards. Good luck
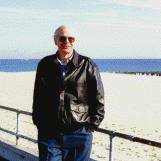
Ted Mooney, P.E.
Striving to live Aloha
finishing.com - Pine Beach, New Jersey
2003
A. RID,
YOU NEED ELECTROLESS COPPER AND ELECTROLYTE COPPER FOR PCB OPERATION. THERE ARE TOO MANY CHEMISTRY IN THE WORLD FOR ELECTROLESS AND ELECTROLYTE BATH [to describe them in detail here].
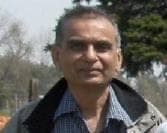
Popatbhai B. Patel
electroplating consultant - Roseville, Michigan
2003
A. Acid copper electroplating bath with organic additives is used in printed circuit board manufacturing.
SHRIRAM BHAT- Bangalore,KARNATAK, India
January 21, 2022
Q. What is the most economical way to measure the thickness of the copper on a two sided PC laminate? Meaning how can you be sure if the thickness is 1 oz or 2 oz copper?
Thanks,
Protek Automotive Products, Inc - Cavite City, Philippines
2005
A. Hi,
You can buy copper thickness meter from your copper laminate supplier. you can check 1/2 oz,1 oz,2 oz.
- Toronto, ON, CANADA
2005
2006
Q. Hi,
I am using a copper electrodeposition bath to make multilayer prototype
PCBs in my university. This bath is a very common bath based on H2SO4, CuSO4,
HCl and Copper Gleam PCM+. The bath has a volume of about 80 l and is used to
metallize 408mm*355mm boards @ about 75 amps (total for the 2 sides).
The bath has been operating normally for two years until I noticed voids in
the copper inner coverage of the holes. I analyzed the different components of
the bath and came to these conclusions:
- Cl- is at 35ppm which is a bit too low but I am not convinced after a
test in the Hull Cell
⇦ huh?
with a corrected bath sample that this is the cause
of my problem
- Hull cell tests gives a shiny deposit over a very wide i/cm2 range. Larger
that with a fresh solution
- Cu++, H+ ions concentrations look OK
- the bath copper is not blue like a fresh solution but turned to bumps
something much greener (turquoise).
As an additional hint, I was not operating my bath on a regular basis
and had to add some PCM+ after each period without operation.
Does anybody know the cause of the reduced throwing power of my solution
and why the solution turned blue-green?
Best regards.
University of Liege - Liege, Belgium
----
Ed. note: Although it won't fully answer your questions, we think our on-line article "A Review Of Copper Plating High Aspect Ratio Plated Through Hole Papers", contributed by Paul Stransky, will be interesting to you.
A. Hi Christian,
The voids you see are more likely due to the electroless copper or direct metallization process (whichever is used). If you don't have complete coverage on the hole wall you can't expect the electrolytic copper to adhere to it. You could examine the hole walls with an O-Scope (oscilloscope) after electroless copper, or DM. If the copper is tarnished dip in 10% sulfuric dip, rinse, anti-tarnish, rinse and dry. The voids are much easier to see with clean copper.
As far as the chloride level, most acid copper solutions should be 80-85 ppm. The chloride level will not influence hull cell tests. The greenish color you are seeing in the bath is due to brightener byproduct breakdown. A hot peroxide carbon batch treatment will bring the bath back close to the original color and remove harmful organics. If you are using the bath periodically, you should be dummy plating at low current densities before running production. I like to start at 3 asf for 30 min then increase to 5,then 8 asf for the same time period. If you are concerned about throwing power, run a plating test in the lab with a test board and check your thickness. Another tip with high aspect ratio boards is the low and slow approach. I've plated as low as 10 asf for 100 minutes to achieve .001" copper thickness in the hole wall with aspect ratios of 12:1 and a surface to hole ratio of 1.2:1. If I can be of more help to you let me know. Good Luck!
process engineer - Malone, New York
2006
2006
Q. Thank you for your answer, Mark. I am very happy to know that the green color comes from the decomposition of the additive. I take note that the Cl- concentration does not play in the brightening aspects but does it play a role in the throwing power?
I am very puzzled because my problems in hole coverage started one day and remained up to now. I was first using conductive ink from T&T; and had perfect coverage of the hole surface if I could get rid of the air trapped in the holes. This proved, at least in my case, to be a real hard problem since this ink looked very non-wetting (but also very conductive). I was using a wery strong mechanical agitation to expel the air from small holes(10cm/s).
I made a few multilayer boards with this ink but switched to a "single step" solution because T&T; said that this ink should only be used for dual layer boards. (My experience is that thermal shock may disconnect inner layers from the hole, this may be why it is not useable for this purpose).
With this ink, my once perfect holes became once randomly uncovered; even some very large holes could have uncovered areas and this was not symmetrical around the hole axis.
The single step solution I am using now is claimed to need only one PCB dip in this solution and may go immediately in the electrocopper bath. I made a small "pollution" test with a tiny plate and was not convinced at all by the way this carbon solution would mix with the bath. It makes small droplets at the bottom of the electrodeposition bath that I suppose will float anywhere with the agitation. It may also interfere with the chemistry of this bath.
So now, I am using the same method as for the T&T; ink (filling the holes, empty them and dry the board) but I dry at a lower temperature and do the work twice since my Hull cell tests showed that one pass was not giving sufficient conductivity but two were right. Hull cell tests showed 100% covered holes when made with a double pass inking/drying.
Test for comparison with T&T; ink gave the same uncovered patches as usual albeit conductivity between sides of a double layer PCB treated with T&T; ink was 1.5ohms before metallization compared to 4500 ohms for a double carbon treatment. (So, there may be some surface passivation with T&T; ink)
However, when used in the real scale bath, the carbon method gave mostly covered holes except for some of the smaller ones that showed an uncovered ring in the middle of the hole (carbon black colored).
If it is not a question of throwing power, my only explanation is that the carbon on the hole surface is getting dissolved in the copper bath and insufficient conductivity results. Agitation in the large bath, albeit reduced compared to T&T; ink is perhaps too much.
But why is the problem located at the middle of the hole?
Do you have any experience of this type of carbon treatment?
BTW, what is your explanation for the need of a conditioning of the bath when it has been idle? Recreate the black layer on the anodes?
Best regards and thanks for helping.
University of Liege - Liege, Belgium
A. Hi Christian,
Sorry it took so long to get back to you. The chloride level can affect throwing power in respect to proper anode dissolution, introduction of fresh copper ions for the cathode, and replenishment of copper metal to the copper bath. So the lower the chloride level the slower the anode will dissolve. As far as carbon treatment, I put activated granular carbon inside a polypro bag, put the bag inside a carbulator and pump the solution through that. I did this once every 2 months. This is better known as a "carbon polishing" of the solution. This method does not allow carbon granules to get into the plating tank. If organic contamination of the solution is at high levels then a hot peroxide carbon treatment is necessary. This is usually done in a auxiliary tank with a good chemical mixer. After the treatment is complete the solution is filtered back to the plating tank using a filter aid such as DE. I am not familiar with conductive inks. Most shops I have worked with use electroless copper or direct metallization. It seems to me that you should concentrate on the ink process, examine holes before plating to make sure you have complete coverage. If you have cross sectioning capabilities, measure the copper thickness in the center of the hole wall. This will tell you if you have good plating distribution. Cathodic agitation helps. I prefer front to back, 1.5 inch stroke each way, if possible. Dummy plating after idle periods tightens up the film on the anodes to prevent suspended matter in the solution, and nodule formation on the part. Good luck and regards,
Process Engineer - Syracuse, New York
2006
A. Throwing power in a copper electrolyte is related to Sulfuric acid and copper content. To have a good throwing power sulfuric acid should be above 220 g/l, copper should be below 30 g/l.
Marcus Hahn- Lucerne, Switzerland
2006
2006
Hi Mark and Marcus,
Thank you very much for your answers. I was away for a few weeks but I am now back with my problems. It looks like I should solve different problems or at least find a way to verify if they are linked together. I should first test the bleaching of the solution but I am in a hurry and decided to store the old solution and make a new one in the cleaned tank/electrodes/nuggets.
I will immediately see what is the effect of a new bath on the hole coverage and throwing power. If the solution has an effect on hole coverage for the two inks, I will implement a filtering circuit and bleach the old bath later + recheck bath composition. Otherwise, I will have to understand what has changed in the hole activation processes - carbon or ink based.
Best regards.
University of Liege - Liege, Belgium
Larger grains around PTH in acid copper plating of PCB
Q. WE HAVE AN ACID COPPER PLATING FOR MAKING PCBs.
RECENTLY WE ARE EXPERIENCING LARGER GRANULAR APPEARANCE OF COPPER AROUND PTH HOLES. THE LARGER GRAINS ARE VERY LOOSE AND CAN BE REMOVED BY USING A KNIFE. IN THE PCB TRACKS THERE IS NO LARGE GRANULAR APPEARANCE. IT IS CONCENTRATED AROUND THE HOLES.
THE CURRENT DENSITY IS 30 ma/Sq cm. KINDLY ADVISE.
PRODUCT DESIGNER - TRIVANDRUM, KERALA, India
September 28, 2010
A. Hi Saravanan,
The problem may be due to too much organic additive and/or contaminants inside plating bath. You may do carbon treatment to see if any improvement.
Regards,
David
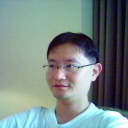
David Shiu
- Singapore
October 1, 2010
Q. We have carried out carbon treatment, The things become worse now. The copper deposit is dull and powdery. We are adding additives after every carbon treatment. Is it possibly due to excessive additives? If so how to correct the problem.
Saravanan R [returning]PCB FABRICATION - Trivandrum, Kerala, India
October 8, 2010
Bumps on the copper plating of a soft PCB
Q. Hi We have received pc boards that have been copper plated and they have small bumps or spheres about .001 to .002 in diameter scattered around the surface. These create an issue in a close fitting assembly. Could anyone tell me why this is happening so I know what could cause this when I talk to the vendor.
Bud OsthausProcess Engineer - Souderton, Pennsylvania
November 10, 2010
A. Hi, Bud. Unfortunately, the symbol you used for the units of measure did not survive the encoding hardships of email and webpages. Could you spell it out? But it sounds to me like the copper is blistered (no adhesion to the substrate), which is a prelude to it flaking off and doing who knows what. If they are scrap parts, try to remove the bump with a razor blade and see if it is indeed a blister.
Regards,
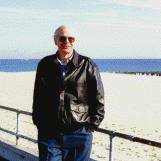
Ted Mooney, P.E.
Striving to live Aloha
finishing.com - Pine Beach, New Jersey
November 10, 2010
A. Clearly, the vendor has a problem. If he (she) cannot fix the problem, find another vendor. The threat of leaving will get most platers' attention.
James Watts- Navarre, Florida
November 11, 2010
Problems in copper direct plating processFebruary 20, 2014Q. Hi: Hull cell test gives OK picture. All contacts are cleaned, the rectifier is also tested -- it's OK. Anodes are not passivated, anode vs. cathode area ratio is 2:1. - Saint-Petersburg, Russia |
|
A. Hello Dmitry,
You mentioned your hull cells were good, and all the connections, rectifier, and bath chemistry checks out. First, I would employ the "old process of elimination" to zero in on the problem. If you could obtain a few panels of some Cu clad material the same size as your part seen in the picture. They don't have to have holes drilled in the panel, or go through the metallization process. A local PCB shop in your area would have some of these they would probably give you. Scrub, clean and activate the panel. Cu flash the panel at the same current density and time as you normally would. If the panel does not show any sign of problems, then you have to concentrate on the Direct metallization process. If you continue to see the problem, your acid Cu bath may be contaminated. I have seen panels that resemble this that came off an Electroless Cu plating line for PC boards. The culprit was a failing replenisher pump resulting in an unstable Electroless bath. You will also want to do an adhesion tape test to be sure you have good adhesion after your direct metal process. Let us know how you make out.
process engineer - Malone, New York
February 21, 2014
February 25, 2014
A. Dear Dmitry Kolesnichenko,
Here the following will help to solve the issue.
1) The sulfuric Acid Content is very high. Reduce to 100ml/l
2) Current Density is also very high. Reduce to 1 A/Dm2
3) High organic Contamination - Do the activated carbon treatment to the bath.
4) Ensure the electrical contacts to the substrate.
Thanking you,
- Bangalore, Karnataka, India
Q, A, or Comment on THIS thread -or- Start a NEW Thread