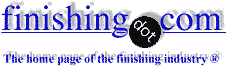
-----
Problem of part impingement on centrifugal barrel finishing machine
Q. Dear sir,
I am entrusted with the task of rectifying part impingement and consequent damage while processing compressor valve reeds on centrifugal barrel finishing machine. The valve reeds are made of spring steel, 55 hrc, 0.4 mm thick fine blanked of various sizes, viz., 100 mm dia, 30 mm square, etc. Quantity processed per barrel is 10 and 40 respectively. The media used for deburring is 5x5 high abrasive triangle angle cut. The process time is 4 hours. The quantity required to be processed per month is 3,00,000. The problem is so acute that we are unable to process at all. We will be very much thankful if anyone can suggest a suitable remedy.
employee - Coimbatore, Tamil Nadu, India
2006
A. Saw your problem before I went on vacation. I had and maybe others had problems trying to figure out exactly what the problem is or was. I think you are trying to deburr some small thin and hard parts which also sounds like they are basically flat parts in a high energy centrifugal mass finishing system. If this is the case, you should consider a dry organic abrasive media process. Media should be smaller than the part. There was no mention of the final surface finish; however, that does not seem to be your problem.
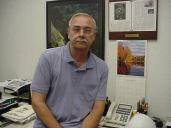
AF Kenton
retired business owner - Hatboro, Pennsylvania
2006
Q. Dear sir,
Thank you for your response. As you have rightly understood the parts are flat thin sheet metal one. Finish required is 0.2 Ra. As suggested by you kindly let me know the details of the media and the process.
regards,
mass finishing - Coimbatore, Tamil Nadu, India
2006
A. If your 5x5 media does improve the finish, stay with it, but for that smooth of a surface finish you need a second and third processing step using dry organic media. For the second step, I suggest primarily a wood sawdust impregnated with pumice ⇦ on eBay or Amazon [affil links] and a binder. Third step, use a treated corn cob mix.
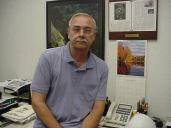
AF Kenton
retired business owner - Hatboro, Pennsylvania
2006
Q. Thank you Mr. AF Kenton,for your reply.
I would like to know the details and procedure of impregnating sawdust with pumice and binder and also for the third process the method of treating corncob is required.
with kind regards,
mass finishing - Coimbatore, Tamil Nadu, India
2006
A. Sorry to say that I cannot tell you what you want to know. I do not make the materials that I use. I make equipment and buy the supplies I mentioned previously. I cannot provide the technical info to create them.
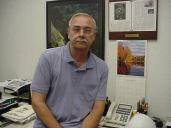
AF Kenton
retired business owner - Hatboro, Pennsylvania
2006
Hi Francis & Anthony. We're speaking of proprietary abrasive products which might involve trade secrets. Due to the anonymity of the internet we must all be watchful to not accidentally crowd-source industrial espionage, so we can't post undocumented info about how to make those products anyway :-)
But if anyone can post a link to published information about it we'd appreciate it. Regards,
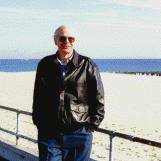
Ted Mooney, P.E.
Striving to live Aloha
finishing.com - Pine Beach, New Jersey
A. I would rather suggest to use cutting and polishing pastes along with saw dust and corn cob, which will give faster and better results and will not damage the components.
Dharmendrasinh. Mahedu- Jamnagar, Gujarat, India
January 24, 2012
A. One way of finishing these thin valve plates is using Vibratory Finishing using special dry media. Being a dry process you can load more parts and there would not be any marks on surface due to the high G force.
Prasad Gogate- Thane, Maharashtra, India
January 8, 2018
Q, A, or Comment on THIS thread -or- Start a NEW Thread