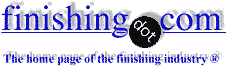
-----
High Precision Optics by Electroforming
Q. Looking for information on method/materials to electroform very high precision optical components/systems.
Required is replication of optics matching SPDT capability- Shape accuracy.
The standard electroforming has the "snap" effect upon release from the mandrel.
What are the known materials and methods to control the unwanted shape accuracy change?
Is it possible to control the shape accuracy down to 10nm from nominal for optics sizes up to 600 mm?
Market research - Pleasanton, California, USA
2006
A. I don't think I agree that this 'snap' effect is implicit in the process. If the stress is near zero and the thickness of the electroform is sufficient, and the adhesion to the mother is optimally controlled, and the elastic stress limit is not exceeded during removal from the mother, I don't see why there would necessarily be any 'snap' whatsoever.
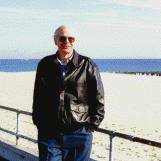
Ted Mooney, P.E.
Striving to live Aloha
finishing.com - Pine Beach, New Jersey
A. As Ted pointed, controlling for near zero stress and sufficient thickness is crucial, as is mandrel surface preparation. Most optical electroforms I've seen that are that big are at least 1/2" thick. How thick are you plating? What are your mandrels made of?
Guillermo MarrufoMonterrey, NL, Mexico
Q. Controlling stress of as electroformed is crucial- I agree, but does not provide the accuracy of shape replication to the required.
Unfortunately, the challenge is in thickness of electroformed optics (for example Wolter- type shells) is approx. 2 millimeters- limited by requirement. (and up to 600 mm diameter sizes)
Is the NiCobalt or NiMn? or ? or other electroforming materials better in the shape accuracy (Stress) replication than just Nickel?
Is for example the Ni+Fe (Invar) possible by electroforming?
- Pleasanton, California, USA
2006
A. We're still not quite understanding each other, so to expand the question into other electroforming alloys may make comprehension muddier rather than clearer; but yes it is certainly possible to do nickel-cobalt electroforming and it may be possible to do Invar. But we're still confusing fidelity, and stress, and probably others issues. It is possible to produce very large (substantially bigger in diameter than 600 mm) very thin (in the range of 2 mm) nickel shells with zero stress; they are used on telescopes to be launched into space (I believe infrared rather than x-ray). I don't know that the required accuracy is 10nm though; they are probably not that accurate due to their size and their inherent flimsiness.
But I don't believe 'snap' to be one of the limitations.
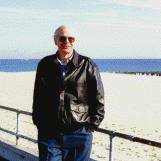
Ted Mooney, P.E.
Striving to live Aloha
finishing.com - Pine Beach, New Jersey
2006
Q. OK- How to truly control + produce Nickel shells optics (600 mm diameter 2 mm thickness) with "ZERO" stress, during electroforming, and during/after separation.
FYI--Currently use Nickel-Kanigen mandrels polished to < 1nm RMS etc
HELP!
Who/were is/are the true EXPERT (or specific information/instructions) on that or Consulting, etc.
- Pleasanton, California, USA
A. The principle is that you formulate a nickel sulphamate bath that deposits at nearly zero stress, but which can be made slightly tensile by increasing the current density, or slightly compressive by decreasing the current density. Then you start plating and you use an instrument to measure the stress, and you continuously adjust the current density upward or downward to maintain zero stress.
I am sure that there are more than two true experts in the world. But two gentlemen whose facilities I have visited and who impress me as world class electroforming experts are:
1. Berl Stein who is president of NiCoForm [a finishing.com supporting advertiser], Rochester, NY and
2. Darell Engelhaupt, who when I met him was with Marshall Space Flight Center in Huntsville, AL (see wwwastro.msfc.nasa.gov/xray/research/papers/SPIE_5168_p129.pdf ⇩).
Dynatronix has supplied the pulse plating rectifiers used in some of these applications and may also be able to help.
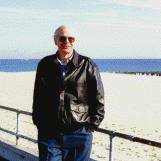
Ted Mooney, P.E.
Striving to live Aloha
finishing.com - Pine Beach, New Jersey
Ed. update Jan 2025: The above link is broken. Thankfully, the Internet Archive preserved a copy here
Please consider a donation to The Internet Archive. Don't follow abandoned links, old URLs are sought out by hackers!
A. I couldn't agree more to Ted. Several years ago I attended a course where both Mr. Stein and Mr. Engelhaupt gave two of the most interesting lectures. May I suggest that you also contact the Nickel Development Institute or Mr. George DiBari, one of the organizers of that course and himself a well recognized expert in nickel electroforming. He used to work there.
Guillermo MarrufoMonterrey, NL, Mexico
A. You can't really have a zero stress deposit. Different current densities at different locations will change the stress, as will small changes in temp and chemical composition. This sort of distortion is normally taken care up by backing up the electroform, for example with a reinforced epoxy structure, before removing from the mandrel.
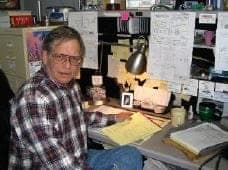
Jeffrey Holmes, CEF
Spartanburg, South Carolina
Thanks, Jeffrey, the reinforced backing sounds very useful. Although there is no such thing as exactly a pound of coffee, neither more nor less, nor exactly a yard of fabric, nor zero stress, stress can be controlled so close to zero that we can build amazing things. Stress can be controlled far closer than even most industry experts realize.
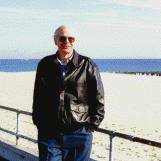
Ted Mooney, P.E.
Striving to live Aloha
finishing.com - Pine Beach, New Jersey
Q, A, or Comment on THIS thread -or- Start a NEW Thread