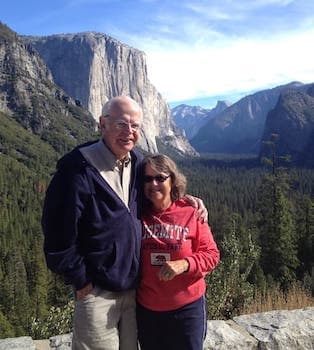
Curated with aloha by
Ted Mooney, P.E. RET
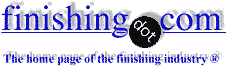
The authoritative public forum
for Metal Finishing 1989-2025
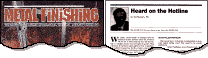
-----
Tin plated parts turn yellowish

this text gets replaced with bannerText
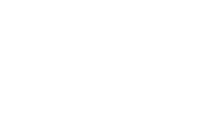
-- this entry appended to this thread by editor in lieu of spawning a duplicative thread
Q. Water patches and yellow color appearing on tin plating done over copper base and Ni coat. How to get rid of this decolorization and water patches?
- Bangalore. Karnataka, India
December 6, 2022
A. Alkaline tin solution is difficult to rinse off. Go back into the cleaner tank and then back thru acetic acid ⇦ this on eBay or Amazon [affil links] .
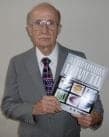
Robert H Probert
Robert H Probert Technical Services

Garner, North Carolina
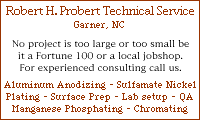
⇩ Related postings, oldest first ⇩
Q. I am barrel plating tin on copper plated aluminum. I have a problem of yellowish spots on the tin plate that later turns grey. I have a cascading final water rinse. The rinse is city water that is 8 grain hardness. I am a novice, so I would like someone to explain the proper steps from the raw aluminum to the copper to the tin to the final rinse. Is a corrosion inhibitor needed, and if so, what kind?
James C. Young- Cincinnati, Ohio, USA
2001
A. Are you plating bright acid tin? If so, you may be having a problem with the organics from the brightener. After the tin bath, you might try rinsing followed by a real mild alkaline rinse (or something like Lea Ronal's Neutra Rinse), then another cold rinse followed by a hot final rinse.
Phil Pace- Tulsa, Oklahoma
Q. Hello,
I'm a Quality Manager for metal stamping company. We produce an automotive part made from CDA194 that is hot tin dipped (97.5 % pure) and hot air leveled to 100-350 micro inches before stamping. The finished stamping is heated through three different process (molding, epoxy cure etc.)with the highest temperature at 300 degree F for twenty minutes. The product has been made for years but material from a single plater has turned yellow at the heating process.
Lab tests suggest that 1) The plating is oxidizing and turning yellow - normal for tin. 2)The copper is migrating through the plating. 3) The plating was not properly cleaned and should have had an aqueous wash and rinse as part of the process. Could you review the hot dip tin process and suggest what you feel could be the cause of the yellowing.
Thanks for your help.
Thomas Coles- Attleboro, Massachusetts
2002
A. Any of the above are possibilities, especially point 1, but since the problem seems related to one plater I would also suggest investigating if he may be using a bright acid tin instead of a matte tin. I am not a hands-on guy on this particular problem, but I would take a wild guess that this yellowing may be organic brighteners decomposing under heat, and that point 3 will not prove adequate to remove them.
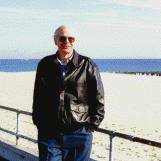
Ted Mooney, P.E.
Striving to live Aloha
finishing.com - Pine Beach, New Jersey
Tin coating is yellowing in steam
Q. Dear knowledgeable finishers:
I wonder what causes tin coating over brass to yellow after exposure to water steam for few hours. Different parts show various degree of yellowing. Does anyone have any means to prevent such yellowing? In the form of post-treatment, or polarization pulse(s)?
Thanks,
Alexander Scheglov- New Milford, Connecticut
2003
A. Plated tin coatings do tend to yellow as they age. This is an oxidation of the surface. Steam speeds up the process. It can be reduced by treating the tin coating with a post dip after plating to passivate the surface.
Gene Packmanprocess supplier - Great Neck, New York
Q. Material Base : - Brass
1st Layer before tin : - Copper base 1~2µm for resistant
Finishing : - Tin Plating (3~6µm)
Question is : -
My customer is complaint the part become yellowish in colour? The volume for this part is low maybe the shelf-life or maybe the chemical concern during plating? Please advise what is the main root cause and how it going to prevent.
manufacturer - Penang, Malaysia
2006
![]() |
A. Hello Asuad, process engineer - Malone, New York A. Tin plating electrolytes will not rinse off. Later they turn the surface yellow. Dip the finished tin plate back in the alkaline cleaner for about 30 seconds. The finish then will not turn yellow. ![]() Robert H Probert Robert H Probert Technical Services ![]() Garner, North Carolina ![]() |
A. Your problem is insufficiency rinse after plating, if you use post treatment by tri-sodium phosphate, you will try use chemical name Neutralizer TL (Enthron OEM).
Warawut prachasirisakul- Thailand
Q. We are a manufacturer of copper lugs and connectors. For corrosion resistance, we plate our lugs with a layer of tin which is 7-10 microns thick. Right now we are facing major quality issues with the plating, wherein the lugs are getting tarnished (patches/streaks brownish yellow in color) a few hours after plating.
Our plating process is acid tin plating, and the bath is made up of sulfuric, stannous sulphate, brightening agent, additive/booster.
manufacturer of cable lugs - Mumbai, Maharashtra, India
2007
A. Hi Chirag,
Too high of brightener will end up with the problem as you described. If you cannot balance the additive, dilute the bath.
Eng - Singapore
Q. I am looking for a technical document which will describe how tin plating reacts in a hot, humid environment. Here's my situation.
My company is using an alkaline tin process to barrel plate copper lugs. Some of our product is shipped to an uncontrolled warehouse in Singapore, where conditions can easily reach a temperature of 85F and relative humidity of 85%. I am unsurprised to hear that our tin plated product turns yellowish in this environment, especially since we do not use any post plating anti-tarnish treatments. This is a purely cosmetic change which does not affect the performance of the lugs. Recently our Asian customers have been rejecting our product based on appearance. I have explained that this is a natural phenomenon when tin is stored in hot, humid conditions. The customers want more reassurance, namely a third party technical document confirming what I said. I am having no luck finding an ASTM, MIL-SPEC, or other technical document confirming something that I know to be true. ASTM B545 does not address this. Any suggestions would be greatly appreciated.
PS: I am not looking for solutions to the yellowing issue, as I am already investigating several options. I'm just looking for a document which addresses how tin reacts in a humid environment. Thank you in advance for any help.
Plating Engineer - Orland Park, Illinois USA
January 20, 2009
Q. I have received some material that supplier confirms has passed Hot Tin dip process which's made surface finished to be white slough around there. I have little experience in this process and it's hard to explain by wording, but please let me know your e-mail to send picture to review.
It's deviated from the previous parts I got, that's the reason of this problem. May someone drop your advise about white slough from Hot Tin dipped process, Please?
supplier quality engineer - Chonburi, Thailand
February 12, 2009
Ed. note: email the photos to mooney@finishing.com, Ariya
Why did pure tin plate discolor after aging?
Q. We have similar issues with discoloration (Yellow and gold stains) on parts that Tin is plated on nickel surface after aging (155°C 16 hours).
Michael Melamudengineer plating process - Israel
March 25, 2010
A. Hi,
Tell us which tin plating solution you have -- is it alkali or acid? The maintenance is difference between these. Do you use brightener in it?
Regards
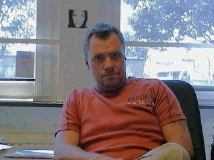
Anders Sundman
4th Generation Surface Engineering
Consultant - Arvika,
Sweden
Try rinsing better and use less brightener.
James Watts- Navarre, Florida
Q. WE TIN PLATE 110 COPPER STRIP COILS IN A TIN BATH AND ROLL IT BACK UP. LATER, WE SEE WHEN IT GOES TO BE SLIT THAT THERE IS YELLOWING TINT/GOLD DISCOLORING TO IT. BRASS AND BRONZE NO PROBLEMS ONLY ON 110 COPPER ALLOY. WE USE 99.99 HP TIN INGOTS IN OUR TIN BATH. RUNNING TEMP ABOUT 520 °F. WE USE AIR COOLING AFTER IT COMES OUT OF THE TIN BATH AND THROUGH SOME ROLLERS BEFORE IT WINDS ONTO A TAKE-UP. WHAT TO DO TO PREVENT THIS FROM HAPPENING?
THANKS
MIKE
SHOP EMPLOYEE - NORTHBROOK, Illinois USA
March 21, 2019
Yellowing in electroplated tin on aluminum
Q. Good afternoon,
I need your help so that we can solve the problem of yellowing / oxidation in various locations outside the bushings after applying acid tin with the following composition:
Bath Tin methane sulphonate = methane sulfonic acid + + Additive Plutino
Analysis 23/02/10 Sn = 37.2 g / l Acidity = 259.0 g / l Sn control Range = 30 to 40 g / l Acidity = 250 to 300 g / l
Following the automatic tinning line:
Recipe for alloy aluminum alloy Recipe for Bronze
Chemical degreasing degreasing chemical
Electrolytic electrolytic degreasing Degreasing
3 washes 3 washes
Methane sulfonic acid activation = activation = 10% Sulfuric Acid 20%
3 washes 3 washes
Activation = methane sulfonic acid 1% xxxxxxxxxxxx
Tin Tin Bath Bath
3 washes 3 washes
Hot Water Hot Water
Oven drying oven drying
Important notes:
1 - The yellowing occurs in bushings (aluminum alloy) in the recipe for tinned aluminum alloy, because when these same tin bushings bronze in revenue this yellowing does not occur (where the outside of the sleeve is steel and the inner aluminum or bronze) .
2 - Parts tinned bronze in revenue yellowing does not occur.
3 - We are applying a aperagemamperage at least twice the normal amperage, because the rectifier coseguirem not rectify the corrente.Jácurrent. We are buying filters for rectifiers to remedy the problem.
4 - In the bathroom is not being made to organic (Resorcinol 1.5 Kg / Shift + Additive Plutino 600 ml / Shift ANTAROX and 100 g 1 time / week) as was being done to the bath base fluoborate Tin + Fluoboric Acid. Please check what the possible problems that would have to do is go back to organic in the bath today.
5 - Note that at the point where the yellowing, almost no deposition estanhotin. The pictures attached (Ok = layer normal and po = Points where almost no tin deposition and oxidation possible points).
First 2 pictures "Okay"
Last 2 pictures "PO"
6 - There was also need to increase the flow of water washes.
7 - What are the possible problems if the two tin alloys in a single recipe (bronze alloy), since for now we are not having problems.
chemical technician - São Paulo, Brasil
February 26, 2010
A. I did not understand your use of revenue and a word that was aspergem (or something).
I ran a MSA tin line for a couple of years and it would yellow in a few weeks if it was not rinsed in DI water.
- Navarre, Florida
Q. Hello, I am a quality inspector for a company who who makes busway and switchgear from tin plated copper. We receive our busbars plated from a few different plating companies. However, we have noticed that copper bars that are sitting out exposed for a long amount of time are starting to turn a yellowish color. If the bar is flipped over, the other side is the normal "silver" colored side. Some of our customers are rejecting these parts due to cosmetic issues. what is causing the yellow color? Does it have to do with how it was plated or is it something in the air that the bars are exposed to?
Brandon L.- Cincinnati, Ohio
November 3, 2020
A. Hi "Mr. L". Tin turning yellow is the subject of this thread which we appended your question to, and other threads here including thread 44518; but in brief, tin turns yellowish over time due to a combination of simple oxidation in the air, and/or diffusion of copper through thin tin plating.
An underlayer of nickel plating reduces the diffusion and reputedly reduces the yellowing but may not be practical. It may be possible to apply a proprietary tarnish-ban chromate-based corrosion inhibitor to slow the tarnishing.
Surely you've been supplying tin plated bus bar for a while though, Mr. L. If I'm not mistaken we have inquires from your plant on other issues here going back 5 years or so. That motivates the question: "What changed?" Is it a case solely of your Luck & Regards,
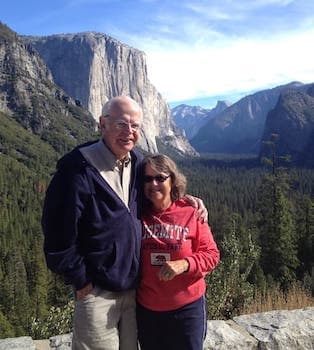
Ted Mooney, P.E. RET
Striving to live Aloha
finishing.com - Pine Beach, New Jersey
A. As a post treatment, dip the tin coated parts in a diluted
alkaline solution.


Sara Michaeli
Tel-Aviv-Yafo, Israel
Q, A, or Comment on THIS thread -or- Start a NEW Thread