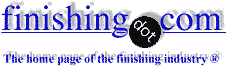
-----
Etching of Tungsten Problems & Solutions Q&A
Q. I was looking for thoriated tungsten wire for making electron emitting filaments. They are available if you are ready to pay a hefty price and buy in bulk. However thoriated tungsten rods used for Tig welding are available easily in the local market. The minimum diameter available here is one mm while I need 150 to 200 microns wire.
Why not reduce the dia by etching? Thanks to Google, I found that tungsten could be etched electrochemically in a solution of NaOH or KOH with tungsten as anode and SS or Cu as cathode. (This technique is used to produce scanning tunneling microscope probes.)
I hooked up a small table top set up with KOH as the electrolyte and SS as cathode. With about 2.5 V and about 0.2 to 0.8 amps one mm rod could be etched down to 200 microns in about 45 minutes. But there is a small problem. The current continuously falls. Stirring the solution does not help much. But a bit of shaking the anode wire leads to a sudden increase in current. This effect increases as the diameter of the anode decreases. This is perhaps caused by tungstate ions which tend to hover around the anode reducing the current flow. Shaking the anode would make them move away thus allowing more current.
Question: Is there a simple way -- say by adding some chemical to the electrolyte -- to transport the tungstate ions away from the anode at a rate equal to the rate of production and keep the current constant?
- Bangalore Karnataka India
October 30, 2022
A. Hi Prabhakara. I don't know how drawable that welding rod is, but we attached your inquiry to a thread wherein Ken Vlach made the suggestion that drawing the material down may be more practical than etching it.
It is universal to have a boundary layer which slows the reaction in applications of this sort, and chemistry may not be the best way to address it; if practical, the best way of dealing with it is perhaps via greater agitation. Some electroplating and other reactions can be speeded up by a factor of 10X by "impingement" (forcefully spraying the solution against the reacting surface).
Luck & Regards,
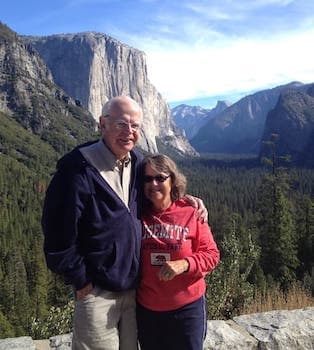
Ted Mooney, P.E. RET
Striving to live Aloha
finishing.com - Pine Beach, New Jersey
Q. Thanks Ted. It seems 150 mm long Tig welding rods are too short for drawing.
In response to a related question you had mentioned " Try anodic dissolution in an NaOH solution of 180 g/L inside a 2 mm diameter cathode of stainless steel tubing." I am afraid it would be too tricky to work with a 2 mm dia cathode without shorting the electrodes. Is the geometry particularly critical ? I tried two geometries one with a copper cathode of about 20 mm dia and another with ss cathode of about 70 mm dia. No appreciable difference was noticed.
- Bangalore Karnataka India
October 31, 2022
A. If you're running constant voltage, I would expect the current to drop as your surface area is reducing. Dissolved tungsten / free caustic is also a likely contributing factor.
Willie Alexander- Green Mountain Falls, Colorado
October 31, 2022
⇩ Related postings, oldest first ⇩
Q. I want to etch .025 mm thick tungsten wire to .2 microns. What etchant should I use? Thanks!
Sherjang singh- Cincinnati, Ohio, US
2003
A. First, look for smaller wire; I found 0.0005 inches (0.0127 mm) diameter wire of 99.95% purity at www.tungsten.com.
I have no experience with tungsten, but suspect this much etching in a highly concentrated HNO3-HF solution (normal for cleaning tungsten) will leave you with pieces of wire. Try anodic dissolution in an NaOH solution of 180 g/L inside a 2 mm diameter cathode of stainless steel tubing. See 'Electrochemical Machining' in ASM Handbook Vol. 5, Surface Engineering. See also the chapter on refractory metals.
Alternately, anneal the wire, place inside Al or Cu capillary tubing, have a wire mfr. draw it down, then etch away the outer metal. Repeat as necessary to achieve the final diameter. It may be necessary to separately draw down and anneal the capillary tubing. For the final steps, perhaps plate Cu onto the tungsten after each anneal. A similar Canning method was once used in the production of tungsten wire.
Ken Vlach [deceased]- Goleta, California

Rest in peace, Ken. Thank you for your hard work which the finishing world, and we at finishing.com, continue to benefit from.
Multiple threads merged: please forgive chronology errors and repetition 🙂
Electrochemical etching of tungsten and stainless steel
Q. In the case of electrochemical etching what etchants should I use in order to machine stainless steel and tungsten? I would like to know if I can find a non-acid etchant.
Thank you,
Mariana Pruteanu- Cedar Grove, New Jersey
2003
Multiple threads merged: please forgive chronology errors and repetition 🙂
Etch titanium/tungsten from gold plated silicon
Q. The company I'm involved with deals with fiber optic/waveguide technology in the research phase. In a clean room environment, I work with silicon substrates with two layers of metal gold and titanium/tungsten. What do you use to etch off the titanium/tungsten?
Erwin Dulaytelecom research - Columbus, Ohio
2004
A. The standard recipe of etching titanium/tungsten is hydrogen peroxide and ammonia ⇦ on eBay or Amazon [affil links] to keep the pH up. This mix does not affect silicon or gold. Take 1 part 25% ammonia solution and 10-20 parts 30% hydrogen peroxide. If necessary dilute with deionized water to lower the etch rate (about 100nm/min undiluted).
Uwe Zimmermann- Uppsala, Sweden
Multiple threads merged: please forgive chronology errors and repetition 🙂
How to remove tips of tungsten wires inside small-diameter polymer tube?
Q. We currently braid a pure tungsten wire with a 304 stainless steel wire. To make one of our products this braid is sandwiched between 2 small-diameter tubes, one made of PTFE and the other made of an Arnitel blend. Sometimes the tips of the braid wires protrude through the polymer walls surrounding the braid. These tips need to be removed so that no wire extends beyond the exposed surfaces of the tubes. We have been able to electrochemically etch away the stainless steel tips but not the tungsten ones. Is there an electrochemical etching or polishing method, or any other method, that can be used to remove the unwanted tungsten tips? Or is there some chemical that could potentially be used effectively as an etching or polishing agent to remove the unwanted tungsten? Ideally we would like to remove the tungsten and stainless steel at the same time but if necessary we can certainly do them one at a time also.
Thanks kindly for your time and any assistance you can provide.
Byron FedieBoston Scientific, medical device manufacturer - Plymouth, Minnesota, USA
2004
A. Hi Byron,
Have you thought of or tried the right 'acid' to remove the tungsten tips? You could perhaps get a pointer on that from any Assaying Company as to which is the best and fastest. Am guessing that HF + Nitric might be the answer. Maybe hitting GOOGLE and asking about W chem. resistance might give you a better idea.
I haven't got the slightest clue what the 'Arnitel blend' is. Please be generic in future. One has to be careful with some plastics but TFE is highly acid/alkali resistant.
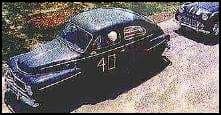
Freeman Newton [dec.]
R.I.P. old friend (It is our sad duty to
advise that Freeman passed away 4/21/12)
A. Tungsten will dissolve in a solution of sodium hydroxide and potassium_ferricyanide [affil links] (about 60 g/L NaOH and add the potassium ferricyanide until no more will dissolve / saturated solution). Although the dissolution is fairly fast, anodic current will speed the dissolution of tungsten.
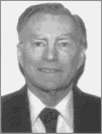
Don Baudrand
Consultant - Poulsbo, Washington
(Don is co-author of "Plating on Plastics" [on Amazon or AbeBooks affil links]
and "Plating ABS Plastics" [on Amazon or eBay or AbeBooks affil links])
Multiple threads merged: please forgive chronology errors and repetition 🙂
Titanium Tungsten Etch and Disposal
Q. We are going to be developing a program for etching a sputtered layer of TiW from our ceramic using 30% hydrogen peroxide. I had read that the H2O2 can be neutralized by dropping the concentration to 5%, then adding a 50% solution of sodium metabisulfite and water. It could then be discharged down the drain with 50 times its volume with water. Does anybody have any experience with the disposal of H2O2 that also contains TiW? Any recommendations would be greatly appreciated. Thanks!
Chris Martoranocapacitor manufacturer - West Berlin, New Jersey
2006
A. Hello, Chris. There are likely problems with this. First, your wastewater is probably categorically regulated, which means you can't dispose of it without permits from NJ DEP or your POTW even if innocuous. Second, dilution of industrial wastes as a treatment scheme is nearly always forbidden by law. I'd suggest contacting an industrial waste treatment consultant or a knowledgable waste treatment system supplier before going further.
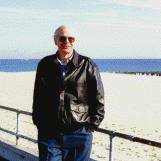
Ted Mooney, P.E.
Striving to live Aloha
finishing.com - Pine Beach, New Jersey
A. I do not remember if either Ti or W are regulated.
For peroxide, it will react with sugar. I am significantly burned from 70% peroxide with a nearly explosive reaction. It generates heat which speeds up the reaction greatly. At 30% I do not think it will react violently, but there is always the day that someone dumped a lot into the waste stream.
As Ted says, you need to talk to your local wastewater and DEP offices first!
- Navarre, Florida
A. To strip the TiW you would have something else in there which you haven't mentioned besides H2O2. As far as the peroxide goes--
H2O2 is basically unstable in the presence of many metals and in concentrations of 30% will be subject to violent exothermic decomposition, so be careful. If you notice it fizzing on its own it indicates it is decomposing by itself and will get faster and faster with more and more heat.
The cheapest way to destroy it will be to experiment at different low concentrations, say about 5%,in SMALL lots, by adding small amounts of Ferric iron which is one of H2O2's most effective "destablisers" to try to get a controlled fizzing which when it stops, you have no more H2O2.
Have a big freeboard in case it goes OFF. Be Careful.
Don't know about the other components though.
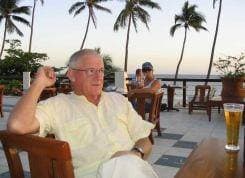
Geoffrey Whitelaw
- Port Melbourne, Australia
Multiple threads merged: please forgive chronology errors and repetition 🙂
Hydrogen peroxide / ammonia etch for tungsten
Q. Can anyone tell me what percentage of peroxide and ammonia I should use to etch tungsten.
Also, what is the base of the ammonia? Chloride or persulphate?
October 24, 2011
R & D - Evansville Indiana USA
Ed. note: Hi Debbie. We've now combined a number of threads about etching tungsten onto this one page; so follow the link to the answer by Uwe_Zimmerman :-)
Etching TiW with hydrogen peroxide
Q. My company uses 30% hydrogen peroxide for etching TiW. When using this material it seems like it's very inactive when it first comes out of the bottle and after one day of usage, maybe 20 electronic boards, the material becomes more active and fizzes and bubbles more and cleans the boards better. Is there any truth to the fact that this material is inactive when it first comes out of the bottom and becomes more active later on?
Timothy InmanAVX ceramics - Myrtle Beach South Carolina USA
November 16, 2019
Q, A, or Comment on THIS thread -or- Start a NEW Thread