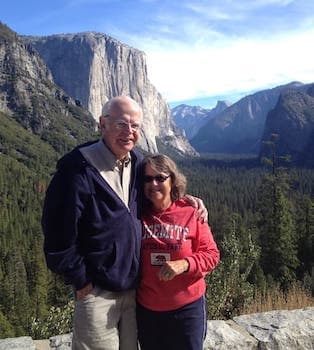
Curated with aloha by
Ted Mooney, P.E. RET
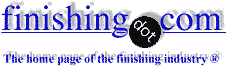
The authoritative public forum
for Metal Finishing 1989-2025
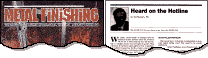
-----
Iron contamination / buildup problem in acid zinc plating

Q. We currently use 1 quart of 25% peroxide to our zinc barrel chloride bath a day and are having problems with our Filter plugging up with non-iron contaminants (we use diatomaceous earth). What does peroxide attack if there is no iron to attack?
Joshua M Voightssupervisor - Reedsburg, Wisconsin
March 17, 2022
A. Hi Joshua. I'm not an acid zinc plater, and don't know the exact amount of peroxide you are supposed to add (and you haven't told us the size of your tank yet anyway). But peroxide is also used to remove stubborn organics like worn-out brighteners, so it sounds like it's possible to overdo it and plug your filters with oxidized brighteners and addition agents.
Luck & Regards,
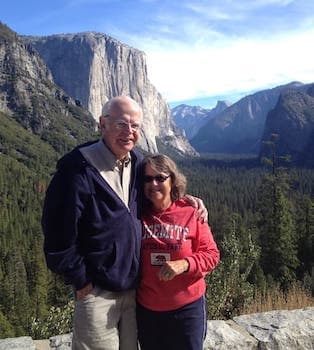
Ted Mooney, P.E. RET
Striving to live Aloha
finishing.com - Pine Beach, New Jersey
A. Ted is correct with his provided information. Treatments of peroxide and potassium permanganate will result in more than just the iron to after treatment. Changing the filters after peroxide and potassium permanganate treatments is pretty standard.
Thomas SwanLab Technician - Portland, Oregon
⇩ Related postings, oldest first ⇩
Q. We are plating automobile components by acid zinc process.
Iron inside the solution is generated very much. How much iron is tolerable? Can we use any iron chelating agent to trap soluble iron? Will the chelated iron create problem in plating or in post treatment?
DIPANKAR SEN- Calcutta, INDIA
1999
![]() |
A. Dear Mr. Sen, I have not seen many problems caused by excess Iron in Acid Zinc as long as the Iron is in the ferric (+3) state and the pH of the bath is above 5.2 - Just make sure that you check that by means of a test strip and that the Fe+2 is way below 3 ppm, If it's higher, make sure to oxidize w/ Hydrogen peroxide or Potassium permanganate (1 g/L of Fe+2 requires approx. 1 g/L of Permanganate or 1.2 g/l of Peroxide 30%) Run lab tests to determine the exact necessary quantities first. "Continuous filtration" helps to remove the Iron build up. Forget about Chelating agents! Domingos J C Spinelli- Brazil A. Hey Dipankar Sen, A little iron is ok, but too much iron can cause problems. Iron plates out in the high current density areas and chromates much darker than does zinc (iron causes the black spots in zinc barrel plating). The iron can be controlled by using hydrogen peroxide. Use about 500 mls per 370 liters (35% hydrogen peroxide mixed about 50/50 with water to protect the brighteners)to oxidize the iron +2 to iron +3 and repeat as needed. The iron +3 precipitates and will muddy the solution. The precipitate must be filtered (filtering this gel is a real problem) out of the solution (the iron +3 will be reduced at the anode back into iron +2, if not removed, to start the problems all over again). Use a Hull cell to check the solution for iron by chromating the panel after plating. You can also check for iron by using a dropper to add peroxide in a breaker and measure the response. Turn the bath over about three to five times (or more) in an hour with lots and lots of filter surface area!. The best control is prevention. Do everything you can to keep the iron out of the solution. Fish parts out of solution often, control the pH (solution too acid speeds the iron build-up), go into the solution hot (if you can)and use the right part placement. Be very careful to follow the data sheet directions with the hydrogen peroxide. Always wear the proper protective equipment (rubber gloves ⇦ this on eBay or Amazon [affil links] , goggles ⇦ this on eBay or Amazon [affil links] , face shield ⇦ this on eBay or Amazon [affil links] , apron ⇦ this on eBay or Amazon [affil links] , sleeves, etc.). Regards, Fred Mueller, CEFRoyersford, Pennsylvania |
![]() |
A. Dear Mr. Sen, In complement of the very pertinent responses of Mr.Spinelli and Mr.Mueller, I would add that a simple way to get rid of the iron in an acid zinc plating bath is to use air agitation (with a blower, not a compressor) together with good continuous filtration. The oxygen of the air will have the same action as hydrogen peroxide, but much slower and without destroying certain components of the brighteners. Even in a barrel plating bath, the use of a small air sparger is very efficient. Obviously, this method requires the use of low foaming wetting agents in the bath formulation. Best regards, Emmanuel Popesco- France A. Hello Dipankar Sen : both answers are good. At 0-25 ppm, iron not a problem. 25-50 ppm could see problem. 51-100 ppm probably see a problem after clear chromate. I have seen barrel chloride zinc plate o.k. at up to 190 ppm. We use an A.A. machine to check our customers baths to monitor iron. Some tips: Many times the acid pickle before plate as well as water rinses become contaminated with iron, will contribute to iron being dragged into the plater. Be sure and put a fresh filter on the zinc solution before peroxide or permanganate. May have to change after each treatment as well. Expect to make an adjustment add of carrier/wetter and brightener after each treatment ... a small portion will be removed along with the iron. Bill Hemptech svc. w/ chemical supplier - Grand Rapids, Michigan |
A. Dear Mr Sen.
We are similar platers like yourselves and what we do with the quality of filters available in India is not use them at all. All the responses are absolutely perfect provided of course that one is able to filter out the sludges caused by H2O2 treatments.
What works for us is to let the sludge lie and take care during racking that we leave at least 12 - 18 inches from the bottom of the tank till the lowermost component to ensure that the muddy sludge isn't stirred up during plating. obviously Air agitation is ruled out and we resort to cathode movement instead which also gives us a roughness free deposit.
The sludge is periodically decanted out where the beautiful filters come in use for transfer filtration only. I don't recommend filtration nor air agitation whilst the plating is going on. There is a gold mine of information on the above responses, which I wonder if any of your suppliers (or mine) have ever given us which by all means one can use for calculation of exact amount of peroxide or permanganate, but do use this only prior to blend ready to decant / clean or transfer filter the bath and not during production times.
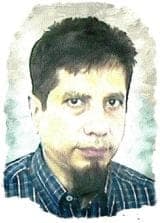
Khozem Vahaanwala
Saify Ind

Bengaluru, Karnataka, India
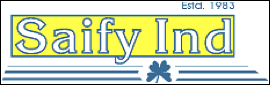
A. Generally add 1 quart 35% H202 per 1,000 gal./bath.
Best not to add while plating.
If you run a continuous filter 24 hours, will help prevent sludges in the tank. Air agitation is required in rack plating to prevent burning due to higher current densities. If the wetter/carrier level is maintained at 4%-6% foaming should not be a problem.
Bill Hemptech svc. w/ chemical supplier - Grand Rapids, Michigan
A. Hi, Dipankar. We have an article in our on-line library which may be helpful: Steve Schneider's "Improving Your Chloride Zinc Plating Operation". Good luck
Regards,
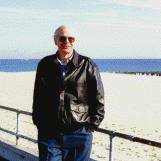
Ted Mooney, P.E.
Striving to live Aloha
finishing.com - Pine Beach, New Jersey
Thank you so much with good experiences.
- Bangkok, Thailand
June 23, 2009
Multiple threads merged: please forgive chronology errors and repetition 🙂
Allowable level of iron in Zinc Plating
Q. I am interested in what Fe (iron) levels can be tolerated by the majority of zinc electro-plating processes delivered from the zinc raw/start material? i.e., Fe at 1.0%, 0.1%, 0.01% etc. Are there particular electro-plating processes that are Fe sensitive and what %Fe maximums should be set for such processes.
Thank you in advance,
Ian Forrest- Walsall, United Kingdom
2001
A. There are three systems to plate zinc:
Cyanide Zinc baths: These do not contain any Fe when new, and tolerate dissolved zinc quite well by complexing dissolved iron into ferrocyanide complexes and perform quite well, except that cyanide is on the Environmental hit list and possibly on its way out in the UK.
Acid Zinc baths: These too do not contain iron when new, but when run, on account of the low pH values of 4.5 and chloride levels of 120 or plus that and the presence of Hydrochloric acid to adjust pH tend to dissolve iron wherever a bare surface is present, such as in a barrel during its first few minutes when zinc has barely started covering the HCD part of the articles . Iron comes in via the pickle too if poor post pickle rinsing is the practice. Tolerance to Iron is possibly best answered by the supplier of the proprietary bath as all acid zinc baths have some dissolved iron tolerance Built in. Black spots and haze and poor chromate receptivity are the main effects of iron Contamination. Hydrogen peroxide is added almost daily to precipitate dissolved iron.
Alkaline Zinc baths: These are composed of and zinc as metal, do not dissolve iron being alkaline, hence favor the non-dissolution of iron during the first few minutes of Plating and have additives that delete the negative effects of iron dragged in from the Pickle.
All things being equal, a good pretreatment line is essential for good plating.
The Iron tolerance property of Cyanide baths is the best, followed by the Alkaline baths and Acid Zinc baths have the poorest tolerance to iron. Proprietary manufacturers are the best place to get numbers to attach to the general aspects I have stated here. An alkaline bath is usually the best for plating steel.
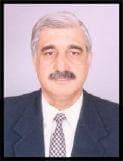
Asif Nurie [deceased] [deceased]
- New Delhi, India
With deep sadness we acknowledge the passing of Asif on Jan 24, 2016
Q. I am aware that HCD burning, and barrel spots arise due to iron contamination in an acid zinc bath. My question is (I am really curious), What is really behind this effect?
Why does it burn the surface? Why does it get black? How does iron affects the bath?
Is this effect just dependent on Iron quantity or does current density combined with iron influences this effect? Is there reference literature in order to understand more about this?
Gracias Y saludos.
Jobshop - San Luis Potosí, Mexico
2006
A. Per the article by Stephen Schneider in our Library section (which was mentioned in the thread we appended your inquiry to), if a part is pressed tight up against the wall of the barrel during plating, all of the current to that area of the barrel will be directed solely to the metal touching and blocking the hole. The current density will be very high, and it will cause the iron dissolved in the solution to plate out right there, turning the deposit black.
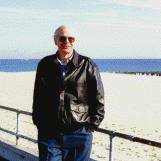
Ted Mooney, P.E.
Striving to live Aloha
finishing.com - Pine Beach, New Jersey
2006
Ted, thanks a lot for the answer. So if the problem arises quite a lot in certain kind of parts, besides using peroxide and/or pumped air; the way I can control it is by reducing the current density by diverse ways, like using a barrel with bigger holes, reducing the overall amperage of the barrel.
Thanks again. Mil gracias!
- San Luis Potosí, Mexico
Q. Dear all,
I have Two Acid Zinc Baths 2000 lit each. Output 8 MT per day. I often get Iron Contamination in only one Zinc Bath. Other Bath is free from Iron Contamination. I am doing hydrogen Peroxide treatment daily but still problem is not yet rectified. What is the source of Iron? I am using both the baths equally but still only one bath gets Iron contaminated I do not know Why? If anyone suggest me?
- Tamil nadu, India.
February 25, 2014
A. Hello Srinivasin,
I would look for parts on the bottom of the tank and / or the equipment used for this tank.
process engineer - Malone, New York
A. Hello Srinivasan ,
Baker answer is right; iron contamination in the bath is due to:
- plated parts falling into the bath during operation is at the bottom of the tank .
- one more cause for iron contamination is from the container or tank.
Root Cause:
Using magnet steel parts can easily be removed from the bath. Daily observation is more important.
Use Polypropylene container or tank for bath.
While iron treatment is done iron hydroxide is precipitated.
Then it should be filtered from the bath .
Regards,
Process Engineer - Tumkur , Karnataka , INDIA
Q. Hello,
I HAVE A ZINC AMMONIUM PLATING TANK. AT THE END OF WEEK I HAVE IRON CONTAMINATION (80 PPM). FOR REMOVING OF IRON WITH POTASSIUM PERMANGANATE, HOW MUCH KMNO4 (gr) FOR 1600 LITERS SOLUTION MUST BE USED?
AFTER KMNO4 WHAT MUST I DO (DUMMYING OR NOT)?
WHEN I USED HYDROGEN PEROXIDE, BRIGHTENER WAS REMOVED (SIMILAR OIL).
FOR 80 PPM IRON HOW MUCH HYDROGEN PEROXIDE IS USED (1600 LITERS)?
CROUSE CO - TEHRAN.IRAN
July 1, 2017
Q. How to check iron content in acid zinc plating process?
Jay dineshbhai ladaniFine thread form industry - Rajkot, gujrat, India
February 17, 2020
Q, A, or Comment on THIS thread -or- Start a NEW Thread