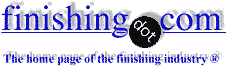
-----
Problems and Issues Hard Anodizing of 7075 Aluminum
Quickstart:
Readers wanting a quick one-page intro to anodizing before joining this dialog, please see "Aluminum Anodizing (Anodic Oxidation of Aluminium): Intro & FAQs".
Q. Hi everyone,
We're experiencing an issue when anodizing 7075 alloy to 30 microns (semi-hard) in black. Some batches anodize perfectly, while others develop gold spots. It doesn't appear to be corrosion, as there's no bloom or other signs of surface oxidation.
To note, batches of alloy from different mills seem to be more prone to this than others.
Our Process:
Degrease
Caustic etch - 60 seconds
Rinse
Rinse
Desmut
Rinse
Rinse
Anodizing (Sulfuric Acid, 11 °C)
Ramp: 0-8V (90 sec)
Hold: 8V (90 sec)
Ramp: 8-16V (90 sec)
Hold: 16V (4 min)
Full Amps: 50 min at 1.85A per 100 cm2 (30-micron thickness)
Rinse
Rinse
Rinse
Dye - 30 min in Clariant Sanodal Deep Black MLW
Rinse - 40 °C for 5 sec
Seal - 45 min in 85 °C nickel acetate
Warm rinse - DI water
Blow dry
Has anyone else encountered this issue? Any suggestions on how to mitigate these gold spots? The fact that it only happens with certain batches of 7075 makes us suspect alloy inconsistencies, but we are getting this same issue from alloy from more than one mill.
Thanks in advance
- Hamilton, Waikato, New Zealand
February 12, 2025
Tip: This forum was established to build camaraderie among enthusiasts through sharing tips, opinions, pics & personality.
The curator & some readers who publicly share their info will be less likely to engage with those who don't.
A. I thought I'd update our progress in the hope it may help someone else.
We have tested multiple process adjustments (especially extending rinse times and double dipping etc) without much success until recently. The parts are typically dyed for 20 minutes, but when we reduced the dye time to 15 minutes, the spots worsened. However, extending the dye time to 30 minutes has nearly eliminated the issue.
Before we noticed the dye time improvements, we noticed that larger runs had less of a problem, a run of the same material at 250 amps, vs the same material but double the surface area at 500 amps seemed to reduce the spotting.
We are trying to understand why increasing the dye time has had such a significant impact. One possibility we considered is that the gold spots could be caused by trapped acid within the pores, and the extended dye time may be allowing it to fully bleed out, enabling better dye absorption.
Cheers
- Hamilton, Waikato. , New Zealand
March 7, 2025
A. Thanks Darren
Luck & Regards,
Ted Mooney, P.E. RET
Striving to live Aloha
finishing.com - Pine Beach, New Jersey
⇩ Related postings, oldest first ⇩
Q. Does anyone have any advice on hardcoating 7075 alloy aluminum? We hardcoat 1" dia rings at 40 F, 18% sulfuric acid, with a proprietary hardcoat additive. Occasionally the parts will burn in the hardcoat tank ( applying .002 thick hardcoat dyed black. I suspect the alloy is the problem since we have little problem with other customers parts of other alloys. The parts are being racked on 6000 series fixtures. Have tried ramping up the current slowly at the beginning of the hardcoat cycle with some success. Would a rack made of the same alloy as the parts help? Any other ideas? Thank you.
Keith RosenblumMinneapolis Minnesota
1998
Treatment &
Finishing of
Aluminium and
Its Alloys"
by Wernick, Pinner
& Sheasby
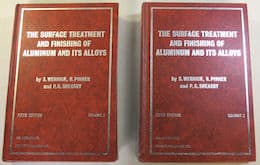
on eBay or Amazon
or AbeBooks
(affil link)
A. Keith
Contrary to what you may have heard, 7075 alloy is not that difficult to hardcoat.
Charlie GrubbsAlpharetta, Georgia
A. To hardcoat 7075, try running the bath colder (we run at 14 °F). Also, make sure you have adequate agitation in the tank. After ramp, your voltage should be approx. 21V (not to exceed 30V).
Henry WolffBritish Columbia
A. Keith. Parts I worked with in industry the anodizer said about.001" per side. Most of what I worked on had to be post finished or polished. The anodizing was like flat paint. It was lapped or finished as required. In effect a very expensive process due to final fit at assembly.
What little I had done on racers was bout the same. It was a very hard surface but worked well. At least the coater or anodizing company was consistent. You could machine parts undersize to allow for it and use as is if possible. There are other durable coatings now that are just about as wear resistant and hard. Ace pistons have this and it takes some bad things happening in the motors to see scuffing now days.
Bentwings Byron NelsonDecember 9, 2021
Multiple threads merged: please forgive chronology errors and repetition 🙂
Hardcoating 7075 Aluminum Alloy
Q. I have a problem with coating hard anodizing on aluminum alloy 7075: the coating looks good when the anodizing is complete. The problem was when the coating needed to be machined down to blueprint size the coating started to peel off as if the coating didn't bond to the aluminum. I need to know if aluminum alloy 7075 can be hard anodized?
Albert Romero Jrphoenix, arizona
2002
A. Done all the time! One customer of ours routinely hardcoats 1/2 mil over size and post anodize hones parts to size. Cylinders are 7075 and since they're for aerospace industry, quality is paramount. They don't peel or crack!
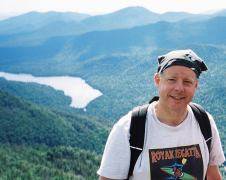
Milt Stevenson, Jr.
Syracuse, New York
Setting up hard anodizing on 7075 aluminum alloys
I'm responsible for technologies and equipment in my company. We're going to introduce and qualify in our shop the hard anodizing process (by the end of April). We need to find the right process parameters. The equipment is under installation, with aluminium cathodes. We'll start to hard anodize sliding areas of airplane structural parts machined from solid (7075). approx. dimensions 1500 * 200 * 200 mm. Parameters intended to be used for testing and qualification: T = around -2°C Max Al in solution: less than 8 g/l sulfuric acid: around 200 g/l Current: 2 to 4 amps/dm2 Oxide thickness: 50 - 100 microns. How about it?
In addition, I would get your suggestion regarding the way to "regulate" the rectifiers (current density or voltage?).
Thank you for your comments, sincerely,
Massimiliano LuraschiIndustrial engineer - Saronno, VA, Italy
2004
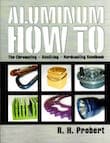
Aluminum How-To
"Chromating - Anodizing - Hardcoating"
by Robert Probert
Also available in Spanish
You'll love this book. Finishing.com has sold almost a thousand copies without a single return request :-)
A. 200 g/L is OK, would be harder at 165.3 g/L. Dissolved aluminum at 8 g/L is OK, but set up a range and decant and add to hold within that range, I generally recommend 8 to 12 gm/L. Start by looking at the voltmeter at 8 volts, 5 minutes later raise to 16 volts, 5 minutes later quit looking at the volt meter and look at the ammeter and raise to 24 Amps per square foot(2.58 amps/dm2 to you).You MUST know the working exposed surface area or use a 1 sq ft panel of 7075 thru a separate 50 amp ammeter and set 24 amps on it. Set the rectifier on automatic current and let the voltage raise itself to hold the current constant. 0.002 should take about 50 to 60 volts and 75 minutes. After that the rate of thickness will fall off as the voltage goes higher and higher, I am not prepared to predict the top amperage and time for the 0.004 (100 microns).
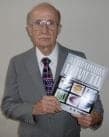
Robert H Probert
Robert H Probert Technical Services

Garner, North Carolina
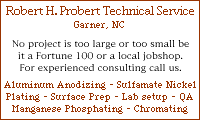
A. In response, can the voltage be ignored by using the constant current setting on the rectifier. Setting the amps per sq dm at 2,5 from the beginning and let the rectifier control the voltage.
Thanks,
John Kleynplating equipment - Cape Town, South Africa
A. I too would like to understand the reasoning behind "8V and then 16V", before anodizing at the required current density. These voltages are meaningless without specifying the current densities they represent. I'm guessing that the intent is to anodize at the beginning of the process at a lower current density, if so, what is the purpose of this? Current limiting (to prevent burning) isn't the answer, a properly designed constant current rectifier will provide ideal current limiting; it needs no help from a forced lower voltage, or from the reduction in electrolyte conductivity caused by dissolved aluminum.
Paul Yursis [deceased]- Columbia, Maryland, USA
Ed. note: it is our sad duty to advise of the passing of Paul Yursis in August 2005.
Here is a brief obituary by Mike Caswell.
Q. I have been having trouble Hard Anodizing 7075 alum, I seem to look great while the parts are wet but after drying the parts look very dusty. The temperature in the anodize tank is 45 °F, volts 25 to 30, time 60 mins.
What's my problem ?
Lynn, Massachusetts
2006
![]() |
RECOMMENDED ANODIZING & CHROMATING BOOKS
for Shops, Specifiers & Engineers ![]() avail from eBay, AbeBooks, or Amazon ![]() avail from eBay, AbeBooks, or Amazon ![]() avail from eBay, AbeBooks, or Amazon ![]() avail from eBay, AbeBooks, or Amazon ![]() avail from eBay, AbeBooks or Amazon (as an Amazon Associate & eBay Partner, we earn from qualifying purchases) A. Hardcoat is done by AMPS per SQUARE FOOT, typically 36 a.s.f. The power must be ramped slowly and the voltage steadily increased until a set voltage, usually typical thickness is achieved at a set terminal voltage - 2 mils at 70 volts, etc. The ramp and characteristic voltage/thickness relationship is highly alloy dependent and 7075 is not one of the easier alloys to hardcoat - the dustiness sounds like early onset of burning. Lastly, 45 °F is rather high for hardcoat - try to get it down to 32 °F. ![]() Milt Stevenson, Jr. Syracuse, New York A. Tell us more. Surface Prep, Free Acid, Dissolved Aluminum, racking, thickness of part, current density, ramp time to c.d... ![]() Robert H Probert Robert H Probert Technical Services ![]() Garner, North Carolina ![]() A. It's relatively easy to hard anodize 7075. These seem like Type II conditions. Perhaps too high a temperature, insufficient agitation for parts cooling, improper current density (e.g., from excessive initial & inadequate final voltages)... Please describe the following: - Goleta, California ![]() Rest in peace, Ken. Thank you for your hard work which the finishing world, and we at finishing.com, continue to benefit from. A. It is powdery,right? Singapore A. Let's See ... If the coating is of a gold-ish color and the dusty like effect is of the alloy and is correct. Remember that the color of the hardcoat is due to the alloy materials. Chris SnyderCharlottem North Carolina |
A. It is rather easy to hard coat 7075 we use a bath at 46 °F; we use 35 ASF 45 min and get 2 mil we do use an additive and lots of air agitation.
Steve Tannergarland Texas
A. Your tank is running too hot! Try at 36 degrees and high agitation. Make sure you have tight contact on racks. Also use aluminum racks not titanium racks. Sometimes you have a better finish and better contact.
James KokielBristol Connecticut
January 21, 2017
Hard anodizing of 7055 aluminum alloy
Does anyone have any experience in hard anodize on alloy 7055 ?
Thanks
WESTBROOK MAINE
August 13, 2014
A. Apparently 7055 is not as commonly anodized as 7075 :-)
We have more than a dozen threads on this site about hard anodizing of 7075, but I'm not sure if they're highly relevant or totally irrelevant to your issues with 7055. What is your situation?
Regards,
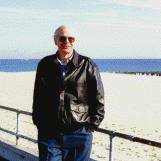
Ted Mooney, P.E.
Striving to live Aloha
finishing.com - Pine Beach, New Jersey
Sodium Sulfonate Additive for increased corrosion resistance of anodized aluminum
Q. I am undertaking a research on anodization of 7075 aluminium alloy. Actually I want to use sulfuric acid anodization with organic acid additives. I don't know which of the sodium sulfonates to use as additive. Is it also possible to use more than one additive in the anodization? The research is basically to improve corrosion resistance of the alloy.
Abdullahi MohammedNigeria
August 29, 2015
? Hi Abdullahi. What prior research or experience points to this as a possible route to improved corrosion resistance? Thanks.
Regards,
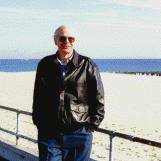
Ted Mooney, P.E.
Striving to live Aloha
finishing.com - Pine Beach, New Jersey
Q. I have anodized 7075 and it has gone green. Any ideas on why?
David CatchpoleLondon, U.K.
November 2, 2015
?? No idea on why without more information.
Was the part dyed?
Sealing medium?
Coating thickness?
Environmental conditions (lighting conditions inside?, outdoor exposure?, temperatures?, etc.) part was exposed to after anodizing, and for how long?
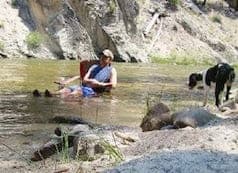
Marc Green
anodizer - Boise, Idaho
Q. HAS ANYONE HAD PROBLEMS HARD ANODIZING 7050 MATERIAL? I GET WHITE patches THROUGHOUT THE PARTS LITERALLY, white parts. ANYONE?
SONIA BALCAZARNORWALK California
September 9, 2016
A. Hello Ms. Balcazar,
Photos of the patches showing their shape, orientation relative to sharp edges or rack points, smeariness of margins, etc. would help.
When are the marks visible? What is the first process step that you can see them?
Also without any information whatsoever on your operating conditions and process steps, any answer the community might have will be no more than a guess.
Please provide some basic information to help us help you.
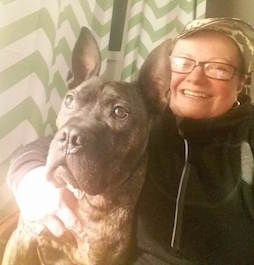
Rachel Mackintosh
lab rat - Greenfield, Vermont
Hard anodizing in minus temperature
⇦ Tip: Readers want to learn from your situation;
so some readers skip abstract questions.
Q. dear sir,
How can I hard anodize aluminium 7075 in minus temperature, and its color should be dark brown. Can you help me.
- lahore Pakistan Punjab
August 25, 2020
A. Hi cousin Nadeem. Apologies, but more words please !
Starting totally from scratch with what facilities, processing lines, accessory equipment, knowledge, chemicals, testing, etc. are required is the subject matter of the many books listed on this page. I am quite certain that we don't have to start from nothing, and that your question is far more specific than that, but there but there is no way for me to know where to start until you introduce yourself and your situation. Thanks!
(affil links)
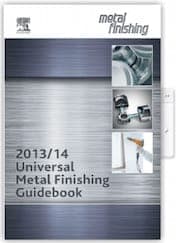
free pdf is currently available from academia.edu
However, on the off chance that you truly know nothing about the subject, please read our "Introduction to Anodizing", search this site for "hard anodize 7075", and view the Anodizing chapter of the Metal Finishing Guidebook -->
Luck & Regards,
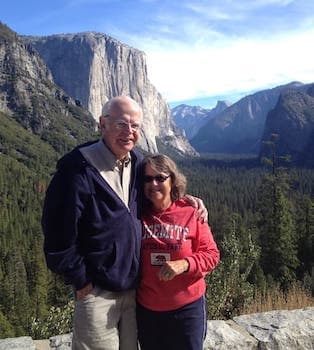
Ted Mooney, P.E. RET
Striving to live Aloha
finishing.com - Pine Beach, New Jersey

Q, A, or Comment on THIS thread -or- Start a NEW Thread