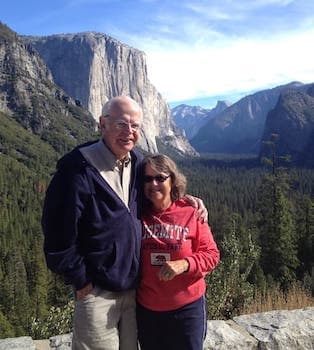
Curated with aloha by
Ted Mooney, P.E. RET
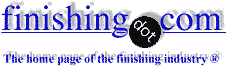
The authoritative public forum
for Metal Finishing 1989-2025
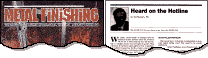
Thread 310/59
Effect of substrate on Electroless Nickel Plating hardness

Q. I am looking for information on applying electroless nickel plating over 17-4PH stainless steel. The 17-4PH part will be heat treated at 900 °F for approximately one hour after the plating is applied. Will the electroless nickel withstand the 900 °F heat treatment? If so, what will the approximate hardness of the electroless nickel be?
Thanks!
Craig Geyer- Sartell, Minnesota, United States
2002
publicly reply to Craig Geyer
A. Craig,
The 900 °F are well within EN safe melting point of around 1,800 °F. So, theoretically it will withstand it.
But, if you happen to have other frequent problems associated with substrate processing, such as insufficient adhesion, entrapped gasses, etc., it may blister or spall, if it doesn't you will end up getting better adhesion due to a little diffusion of both materials. In both cases there will be a slight hardening of the plate, a lost in corrosion properties and other superficial and internal mechanic and magnetic changes due to a change from amorphous to crystalline microstructure.
Monterrey, NL, Mexico
2002
publicly reply to Guillermo Marrufo
A. The EN will easily withstand that temperature. The hardness of your coating will be 64-70 Rc.
Todd Osmolski- Charlotte, North Carolina, USA
2002
publicly reply to Todd Osmolski
Multiple threads merged: please forgive chronology errors and repetition 🙂
Q. We are testing high phosphorus electroless nickel coating for a 4340 shaft (about 1ã long). According to the literature for hardening we should use 400 °C (750 °F) for 2.5hr, for best results. Would this effect the 4340 shaft measurements? At what time is it preferred to perform the heating: before or after grinding?
Thanks,
Arik Ring- Yavne, Israel, Israel
2003
publicly reply to Arik Ring
A. 400 °C is rather hot for 4340 steel. This will lower your Rc by several points compared to a typical 400 °F draw temp after hardening. Yes, the size will change unless the original draw was at 400 °C. It will still change dimensions minorly with a second heat to 400 °C. Also I would expect that your hardness would also drop another couple of points. With all of this in mind, I would probably do a skim grind after plate. Remember, your EN is not terribly thick, so you must run some test parts to see what your changes are.
James Watts- Navarre, Florida
2003
publicly reply to James Watts
A. I agree with James if the part was heat treated before. If not, a slow cool down and a proper positioning inside the oven will not appreciably modify any microstructure or dimension. Also, about grinding EN does not normally require it after plating. Grind it before. G. Marrufo-Mexico
Guillermo MarrufoMonterrey, NL, Mexico
2003
publicly reply to Guillermo Marrufo
Q. Thanks for the input. Currently after machining the 4340 shaft is subjected to stress relaxation at over 500 °C. Please advise.
I was advised that: "Tempering should be avoided if possible within the range 250 °C - 450 °C due to temper brittleness". Could we be risking the shaft mechanical properties when hardening the EN at 400°C?
Thanks,
Arik Ring [returning]- Yavne, Israel
2003
publicly reply to Arik Ring
A. Hardening of EN is an "aging" process. Tempering of steel is also more dependent of time and temperature. On the other hand, quenching is mostly a process where quick temperature changes play the predominant role. Probably you were advised about brittleness meaning that after the EN aging took place, the part must be cooled slowly to avoid re-quenching it.
Guillermo MarrufoMonterrey, NL, Mexico
2003
publicly reply to Guillermo Marrufo
A. I probably never should have replied to this thread as there is so much that I do not understand, Like why use a high carbon steel if you are going to "draw" it at 500 °C? All of the tool steel that I hardened for 4 years had a draw temp of 400-500 °F. My foggy memory (no books anymore) would have a 900 °F draw back to quite nearly the starting hardness.
Hopefully Lee will chip in with the metallurgy of 4330 with an EN cure of a 400 °C . Also, if I remember correctly, EN cure is a time vs temperature tradeoff. Foggy memory had 300 °C as an optimum cure for max hardness. Your trade off of using a lower temperature is an extension of time. Seems to me that 250 °C for 4 hours had an EN hardness of nearly the same as a 500 °C for one hour. The difference would be at max 2 or 3 Rc. Your EN formulation and age of the bath will affect it that much or more. Your EN vendor can bury you in information if you ask for it.
- Navarre, Florida
2003
publicly reply to James Watts
Multiple threads merged: please forgive chronology errors and repetition 🙂
Q. We are using Roller Dies of "High Carbon High Chromium" tool steel of very intricate shapes. The same is heat treated to 50-55 Rc hardness. We got it (High Phosphorous) Electroless nickel plated of 20~25 microns thickness . During the entire stage the distortion in geometries/ profile of the job remained within acceptable range. Further my platers have advised to heat treat the job at 400 °C for 1 Hour. This they say would increase the hardness to 66 ~70 Rc.
My questions:
1. Is the job allowed to air cool after one hour of heating.What is the exact procedure for heating the job.
2. Does the increase in hardness of coating also increase the wear resistance and life of job.
3. Will the heat treatment affect the hardness of the substrate material. Or it may cause distortion in the size of substrate material.If yes, then what temperature and time will be advisable?
Manufacturer - N.Delhi, India
2004
publicly reply to Gaurav Garg
![]() |
A. Gaurav, the one hour is long enough for this precipitation hardening reaction to take place. The reaction doesn't depend on cooling rate, so you want that sufficiently slow so as not to give you any thermal expansion gradients. Air cooling should be fine. For question 2, well, it might. I can't tell from here, as I don't know what kind of service the parts will see, nor the environment the dies must endure. If a hardened nickel layer will help the dies resist problems, then it seems like a good idea. Another reason for doing it is that when you get wear, you can strip off the coating and recoat, for far less money than you can rework a die. For question 3, it depends on the tempering temperature of the particular grade of die steel you're using. ALL of the D grades (AISI designation) have tempering temperatures greater than the 400C called for by your plater. You can find out the tempering temperature used by your heat treater by asking them, can you not? One problem you may see with the aging treatment of the EN, is that like all precipitation hardening reactions, there will be a slight shrinkage of the electroless nickel coating. This means that if you have ID's coated, the coating may want to peel off. I'd suggest trying it on only one die first, after getting the plater to agree to strip and replate if the coating flakes off. Good luck! ![]() Lee Gearhart metallurgist - E. Aurora, New York 2004 publicly reply to Lee Gearhart 2004 A. Depending on why you EN coated this part will effect whether you want to heat treat it. If you coated the part for improved corrosion resistance, do not heat treat it. Heat treatment will severely reduce corrosion resistance. ![]() Ron Duncan [deceased] - LaVergne, Tennessee It is our sad duty to note Ron's passing on Dec. 15, 2006. A brief obituary opens Episode 13 of our Podcast. publicly reply to Ron Duncan |
Multiple threads merged: please forgive chronology errors and repetition 🙂
Electroless nickel plating of heat treated steel and steel hardness relationship
Q. We EN plate heat treated steel and use the parts in an application that exposes the plate to friction use in some areas. We use several hardness ranges for the steel, and have experienced more failures (in the form of flaking nickel that had otherwise passed adhesion tests) with the steel in the 55-60 Rc hardness range. Parts plated that are less hard seem to plate without this problem. Is there a hardness threshold where this becomes more likely to occur, or is it simply a function of the conditions created by the heat treating process and entirely dependent on cleaning on activation? I realize that a nickel strike, with Woods nickel for example, would greatly improve our chances of success; I am simply wondering if the integrity of the nickel can be directly related to the hardness, and if so, what is the range where this occurs?
Allen Clague- Waynesboro Virginia USA
2006
publicly reply to Allen Clague
![]() |
A. Mechanically speaking, the harder the substrate, the better for a hard plate such as EN, for it gives it a better support. Thus, the problem, as reported, seems to be totally dependent on the prep cycle and a Woods strike is one of the surest ways to deal with it. Guillermo MarrufoMonterrey, NL, Mexico 2006 publicly reply to Guillermo Marrufo A. Several possibilities. Heat treatment forms an oxide layer on the steel, thin in some cases. Are you sure that you are getting all of it off? Navarre, Florida 2006 publicly reply to James Watts |
2006
Generally, increasing the hardness of a steel means increasing its carbide content, which in turn makes it more and more difficult to completely clean. There is no relationship between steel hardness and adhesion. And if you are passing your adhesion tests, your shear bond to steel must be fairly good, only not good enough to survive the friction rubbing in service.
I would try to improve cleaning first. A nickel strike may or may not help.
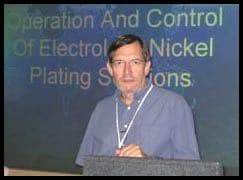
Ron Duncan [deceased]
- LaVergne, Tennessee
It is our sad duty to note Ron's passing on Dec. 15, 2006. A brief obituary opens Episode 13 of our Podcast.
publicly reply to Ron Duncan
Q, A, or Comment on THIS thread -or- Start a NEW Thread