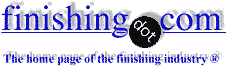
-----
Questionable Plating Practices Observed During Vendor Review
2006
Q. I've recently been asked to consider being a "plating expert" in our M&P group. I have experience plating PWBs, but lack general metal finishing knowledge. This is the first time I've used this forum, so I hope explain myself in the "correct" amount of detail.
We send our vendor small diameter (0.018" OD) 304 SS tubes. The ends of the tube are welded shut, so the vendor only plates the outside of the tube. They plate a nickel strike, followed by 0.1-0.2 mils of copper (cyanide) and then 0.5-0.9 mils of tin-lead (MSA). The tubes are strung horizontally across an an uncoated rack and manually carried from tank to tank.
We have experienced copper-to-copper separation failures on the last two lots the vendor has sent us. The vendor's corrective action was that they found out the plater was leaving the rack in either the dragout rinse or the copper bath itself (w/o amperage) while he went of to check the copper thickness on a coupon. When he came back 4-5 minutes later he was giving the tubes a short copper strike, regardless of whether they passed thickness, without doing any surface prep on the copper. In the future, he has been instructed to do a sulfuric dip and rinse prior to doing additional copper plating.
This seems like a reasonable C & CA to me. However, when we went out to observe the revised process and shop traveler, I saw a few things that I wanted to ask if they were common practices in the metal finishing industry:
1) Prior to placing the rack onto the cathode bar in the nickel tank, the plater dipped/swirled the parts in the solution for 45-60 seconds. Should the tubes see current ASAP after the SS surface has been activated, or is the practice of swirling them in the nickel solution serving some purpose? In addition, the tank has no fluid, air or bus bar agitation. Maybe this is why they pre-dip the parts prior to turning on the current, but our parts have no surfaces that would trap air. Is it normal for ambient temperature nickel baths to have no mechanical or solution movement during plating? Seems like this would be a good way to get nickel pitting.
2) I noticed half of the anode baskets in the cyanide copper bath were 1/3-1/2 low in copper balls. The explanation was that the copper in the bath was climbing, so they removed some of the copper from the baskets. If this is the reason the baskets were low, is this a common practice? It seems like it would be best to decant solution rather than mess with the current density on the anodes. Would removal of some of the baskets, while keeping the others full be a better practice?
3) Both direct and reverse cleaning are used to prep the SS surface. Is it necessary to do any baking of 304 SS tubes for H2 embrittlement reasons?
Thank you for your response.
A. Air bubbles could be present when they place the rack in the tank, possibly that is why they're manually agitating. What type of nickel bath are they using? I've used sulphate, sulfamate, sulfamate/cobalt, electroless, and Wood's strike and none are at room temp (Wood's is slightly higher at 90-93F), and the only one without agitation is electroless.
Removing copper pellets from the basket doesn't sound right to me. Unless all your tubes are below the level of the pellets, the lower tubes will have a thicker deposit.
2006
A. Randy, I can comment on the hydrogen embrittlement issue. Unless your 304 tubes are heavily cold worked, they're going to be immune to the common hydrogen embrittlement found in electroplating processes. Check them with a magnet- if they aren't ferromagnetic, you have no hydrogen embrittlement concerns, and don't need to bake. If they are magnetic, a bake is cheap insurance.

Lee Gearhart
metallurgist - E. Aurora, New York
2006
Q, A, or Comment on THIS thread -or- Start a NEW Thread