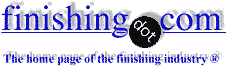
-----
Sealing Process for Hard Anodize MIL-A-8625
Q. MIL-A-8625 / MIL-PRF-8625
[⇦ this spec on DLA]Type III, Class 2
After Humidity test (Five 48-hour cycles), the black dye appeared to be leaching out from the black hard anodize (Type III). The parts were sealed in a dichromate medium instead of boiling deionized water. Other parts that were sealed in boiling deionized water do not exhibit this leaching appearance.
What surface transformation happens during the dichromate and boiling deionized water sealing process?
Thanks,
2006
A. It was not completely sealed. Strictly speaking, "hardcoat" should not be sealed because it softens the coating in that hydrated aluminum oxide is softer than regular anodic aluminum oxide. Also, properly defined "hardcoat" has a pore so small that sealing compounds cannot get deep enough into the pores to clog them up.
However, it is also probable that the sealing solutions your anodizer used were contaminated, or too high in calcium, or the pH was incorrect. Sealing solutions in job shops are notoriously neglected. Sealing solutions are so very dilute that only a small amount of contamination will knock them out, consequently the anodizer lets them go on well past dump time.
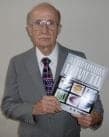
Robert H Probert
Robert H Probert Technical Services

Garner, North Carolina
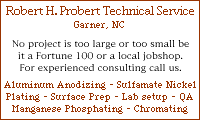
2006
A. When dichromate sealing is required for dyed hard anodize, I suggest 'duplex sealing.' Partially seal in nickel acetate solution or hot DI for 5 minutes, then dichromate seal to completion. This avoids dye contamination of the dichromate solution and a reaction between the dichromate (oxidizer) and the dye.
Check the dichromate solution maintenance records; if none are available, all the problems mentioned by Mr. Probert likely exist. The dichromate solution should be clear, orange color.
- Goleta, California

Rest in peace, Ken. Thank you for your hard work which the finishing world, and we at finishing.com, continue to benefit from.
2006
A. If you're not required to use dichromate as seal I would try just Nickel Acetate sealer.
Chris Snyder2006
![]() |
July 9, 2020 Q. We have an aluminum extrusion that we get from a supplier with a specified dichromate seal for corrosion protection. For ten years these cases have had a light green to dark green tint. They have started coming in with no tint at all. The explanation from the supplier is that their finished says they dichromate with no coloration because that is what their customers prefer. I cannot find any supporting evidence that it's possible to seal these parts without any tint of color at all. They get flagged when they come in the door because they do not appear to have gone through the dichromate process.
July 2020
In the old days they were based on hexavalent chromium and, for the most part, the darker they were the more hexavalent chromium and the more corrosion resistant. But the world has mostly moved on to new technology trivalent chromium coatings which are thin and essentially colorless. It is true that one of the downsides is that they are very difficult to see. Please see MIL-DTL-5541 [⇦ this spec on DLA] or search the site for "TCP" for more info or a better understanding. Luck & Regards, ![]() Ted Mooney, P.E. RET Striving to live Aloha finishing.com - Pine Beach, New Jersey |
Q. So a little more background and I appreciate you taking the time to answer. The cert provided shows:
"HARDCOAT ANODIZE PER MIL-A-8625F, TYPE III, CLASS 1 WITH DICHROMATE SEAL"
The trouble that I am having is how to validate that the dichromate seal was applied if there is no visual evidence as there has been for the last ten years. Complicating matters is that there is a history of batches being shipped that were not coated in the past. It casts doubt now that batches are showing up with no visual indication.
If in fact colorless is attainable via this standard, that's fine. The difficulty comes in that this condition is an indicator of a past process failure, and taking the vendors work for it on it's face with no backup is difficult. Attempting to do some due diligence to understand if colorless is possible given this spec.
July 9, 2020
A. Hi again. Sorry, but you didn't mention anodizing the first time and I misunderstood the situation, so the discussion was put on a thread about chromate conversion coating. It's now been moved to a thread about hardcoat anodizing and my first response struck through.
MIL-A-8625 / MIL-PRF-8625 [⇦ this spec on DLA] is also available for free and you should start by downloading and reading it if you haven't yet, although it looks like you have. It does sound like your inspection criteria is valid and the supplier did not dichromate seal the parts. There may be an invisible 5% dichromate seal, but I've personally never heard of it and I think it unlikely. It sounds to me like the parts were not dichromate sealed and are in non-compliance.
Luck & Regards,
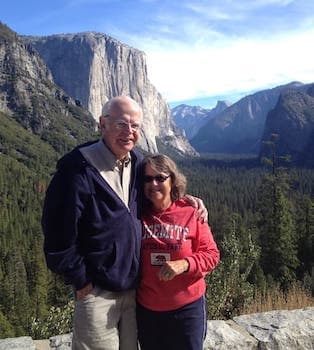
Ted Mooney, P.E. RET
Striving to live Aloha
finishing.com - Pine Beach, New Jersey
July 2020
Q. Here is the general explanation I was given as to why we see no discoloration. Essentially what I am trying to determine is if there is any validity to "no discoloration". Without that visual indicator, I don't know how to confirm that the seal has been applied.
"the plater demonstrated to us that there's a great deal of color variation resulting from the seal application, ranging from no detectable discoloration at all to a very deep green. They're set up to process parts with little or no discoloration because that's the typical preference of their customers."
July 16, 2020
A. Hi Jeremy. I'm sorry but after 3 postings I am still not clear exactly what can be said that would actually satisfy your needs...
- You can demand a cert from the plater that the parts were dichromate sealed and are in full compliance with 'MIL-A-8625F, Type III, Class 1 with Dichromate Seal', and you probably should!
- You can test the parts and determine whether they meet the test requirements, and perhaps you should.
- You can test the parts for the presence of chromate (but if you are not requiring any specific quantity, I'm not clear how verifying that there is 'some' is of much real help).
- You can require that the parts exhibit sufficient coloration that the color can be used as a quick check, especially since you say that there is a history of the seal being omitted.
I previously expressed my personal opinion that if the amount of dichromate is so low that you can see no visual trace of it it's probably not there or too low to be very effective. Some people 'leach' most of the color out of dichromates with hot water immersion, but others (and I'm among them) say that if you've leached the color out you've also out the leached the dichromate out, so what's the point.
I think what you can't do is accept the explanation as it stands and simply accept parts -- especially given the history that dichromating has been missed in the past.
Luck & Regards,
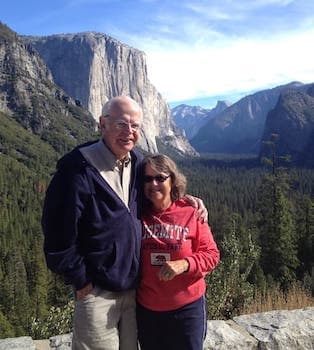
Ted Mooney, P.E. RET
Striving to live Aloha
finishing.com - Pine Beach, New Jersey

Q, A, or Comment on THIS thread -or- Start a NEW Thread