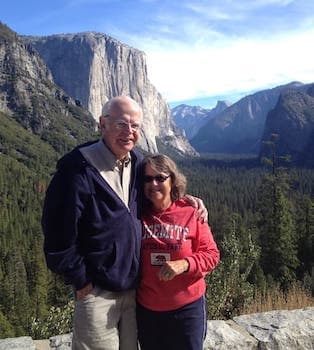
Curated with aloha by
Ted Mooney, P.E. RET
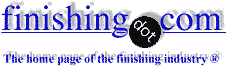
The authoritative public forum
for Metal Finishing 1989-2025
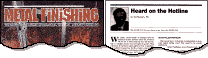
-----
Corrosion Resistance of Alodine Treated Aluminum
Q. I am building a home built airplane constructed primarily of 2024 T3 Alclad. Most of the parts get an acid wash (Alumiprep 33 ⇦ this on eBay or Amazon [affil links] ) followed by a dip in Alodine (Iridite?) ⇦ this on eBay or Amazon [affil links] and finally a coat of primer. My question is: What happens to the corrosion resistance of the alclad if some of the parts don't get a good coat of primer? Does the Alodine increase or decrease the rate of corrosion?
Patrick Armstrong- El Granada, California
1999
A. Chromate conversion coatings ("Alodine") have a dual purpose. They act as a good paint base. They also protect the material from corrosion (theory is that a cut in the film may allow hex-chromium to 'bleed' into the scratch in a wet environment and protect the exposed material - true? I don't know). Alclad is much more corrosion tolerant than bare material, in that the cladding typically contains less in the way of alloying elements. Parts inside the airplane are often left in Alodine, only. However, I would endeavor to get good primer coverage on the parts, just in case the Alodine application is not what it should be - it is a lot more difficult to do properly when you cannot immersion process the details.
Mark McGlynn- Oklahoma City, Oklahoma
1999
Q. Hi, I looking for the same info for clear Iridite.
Joseph Chow- Bayan Lepas, Penang, Malaysia
2000
A. Hi, Joseph. Alodine and Iridite are two trade names for MIL-DTL-5541 [⇦ this spec on DLA] conversion coating. So Mark's answer applies as well to Iridite and to Alodine. Good luck.
Regards,
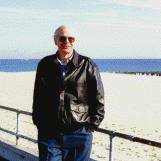
Ted Mooney, P.E.
Striving to live Aloha
finishing.com - Pine Beach, New Jersey
March 1, 2009
Q. Hi,
During application of Alodine 1200 how long we should keep the part with Alodine 1200.
Regards,
Vadivel.
- Bangalore, Karnataka, India
March 7, 2012
Q. I am building a kitplane and the outer wing spars consist of what they call cap-strips, these are various lengths of .125" thick AL 2024T3 stacked up 6 pc. thick both on the top and bottom of the spar web, then they are riveted together to form a laminate structure. The width of all the pieces at the root are 1.625 wide and taper as the go to the far end. My question is about which AL to go with due to the corrosion of bare AL, I know that Alclad does offer great corrosion resistance but with all the rivet holes that need to be drilled and the edges of each cap-strip also need to polished so there is not mill marks, there is going to be much of the area exposed with no Alclad anyway. My thoughts were to just use bare AL, do all the drilling and polishing, acid clean, dip them in Alodine for a few minutes and rivet them up! Any input would be greatly accepted! Would there be a better solution for corrosion than the Alodine? The Alodine I have is Chemfil DX503!
Dwayne AdamskiBuilder - Sycamore, Illinois, US
January 4, 2013
Q, A, or Comment on THIS thread -or- Start a NEW Thread