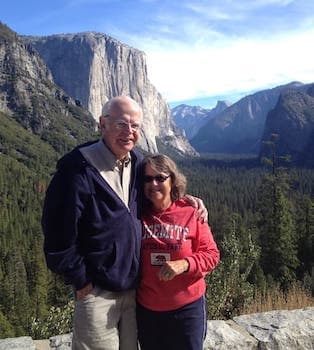
Curated with aloha by
Ted Mooney, P.E. RET
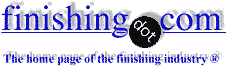
The authoritative public forum
for Metal Finishing 1989-2025
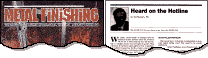
-----
Grey colour in Natural Anodized Aluminum
1999
Recently, we had rejected a batch of anodized aluminium (natural anodized colour). The reason why we rejected that batch was because one end of the profiles was grey in colour. After examining the film thickness at the grey side, we found that the film thickness at grey side was 14 micron whereas at normal natural anodized colour side was 8 micron. We also noticed that the hardness along the profile was also different, approximate 5 units (measured with Webster Hardness Instrument). Does anybody knows the actual problem of this phenomenon. Please reply.
T.Q
Abbe Lim- Selangor, Malaysia
1999
Reference, Canning Handbook 1989, E & F.N. Spon Ltd, London, p. 798, "the anodic film is electrically resistive, therefore, if a variation of coating thickness occurs, there is a redistribution of the current flow over the surface. This results in an increase in the current density at the area of thin coating or low resistance, and a corresponding fall in current density at the area of thick coating or high resistance."
I would guess that there is a problem of stratification of the anodizing solution, and the parts are racked vertically in this solution, or there is a really bad arrangement of cathodes in the tank.
Best regards,
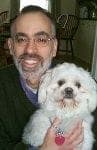

Tom Pullizzi
Falls Township, Pennsylvania
In the aerospace business, we always look with suspicion upon an area of a part that anodizes more darkly than the rest. This can be caused by areas of differing hardness along the part due to an improper heat treat. You might want to evaluate the material in different areas of the part using Rockwell hardness, conductivity and perhaps even running a tensile test or two, if the component is structural.
Mark McGlynnOklahoma City, Oklahoma
1999
Q, A, or Comment on THIS thread -or- Start a NEW Thread