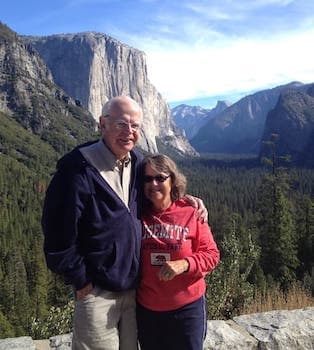
Curated with aloha by
Ted Mooney, P.E. RET
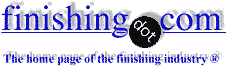
The authoritative public forum
for Metal Finishing 1989-2025
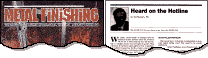
-----
Analytical Methods Needed for a Nickel-Phosphorus Electroplating Bath.
1999
I am a sixteen-year-old senior high school student in the Philippines. My friends and I are assigned a project about electroplating. Nothing really difficult, just a simple setup would do. Your site [FAQ: "How Electroplating Works"] helped a lot.
I would just like to ask where we could buy the zinc strip and what are epsom salt [affil links]s and where to buy them.
Thank you for your time.
Respectfully yours,
Ailil A [last name deleted for privacy by Editor]- Manila, Philippines
Dear Sir / Madam,
We are starting up a nickel - phosphorus electroplating bath and can use some help with the analytical methods. We are fine with the nickel and pH. (1) But, how do you check the ratio of Phosphorus to Phosphoric acids? (2) Nitric acid on the deposit changes the phosphorus to phosphate and we would love a good analytical method for the phosphate.
Any other tips on the operation of this chemistry would be most appreciated. Thanks in advance,
Fred Mueller, CEF- Royersford, Pennsylvania
1999
I am in the metal finishing business for more than twenty years and did not hear of a nickel phosphorous electroplating process yet. Are you sure you did not mean electroLESS?


Sara Michaeli
Tel-Aviv-Yafo, Israel
1999
Hello Sara,
It's nice of you to respond to my letter. The nickel - phosphorus electroplating bath is a very neat story. In 1946 Brenner and Riddell were looking to alloy Phosphorus with all kinds of different metals and had the most luck with nickel. In looking for sources of phosphorus they tried hypophosphite and got cathode efficiencies of over 100%. The rest, as they say, is history.
Bath runs 170 - 190 degrees F. is 50% efficient at the cathode (needs constant acid / nickel additions). Nickel anodes (100% efficient) make the solution grow. Bright WITH OUT additives or wetters and will not "Plate out" on the tank walls. Runs at a pH of 1 - 2, and the low pH "salts out" organics (wetters). Our interest in the bath (we are running trials now) is due to the fact that it will deposit higher percentages of phosphorus than will electroless.
Regards,
Fred Mueller, CEF- Royersford, Pennsylvania
1999
Hi Fred, you are not the only one interested in that bath these days :-)
Other people are working on it too; I can't reveal much more except to say that some of the advantages of plating nickel phosphorous compounds hold true whether it be deposited electrolessly or electrolytically.
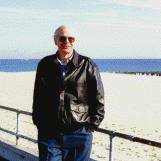
Ted Mooney, P.E.
Striving to live Aloha
finishing.com - Pine Beach, New Jersey
August 23, 2009
Fred,
Electrodeposition of NiP has come a long ways lately. Please see the papers presented at NASA Advanced Material Symposium Clevland, OH May 2002, Nashville SurFin (2001?), Patent
6406611, SurFin Orlando, 2004, SurFin Louiville, KY, 2008 and Plating & Surface Finishing Feb 2009.
Thick deposits of high phosphorus are readily achieved for diamond turning etc. at 115 - 120 F, no crashes, no equipment plate-out, pore free, pit free and any desirable thickness.
- Madison, Alabama, USA
Q, A, or Comment on THIS thread -or- Start a NEW Thread