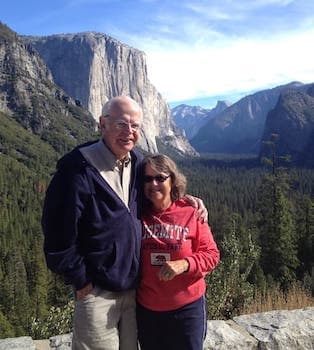
Curated with aloha by
Ted Mooney, P.E. RET
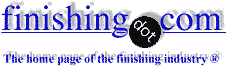
The authoritative public forum
for Metal Finishing 1989-2025
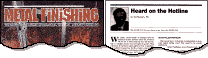
-----
Seismic compliance for plating line installation
We are installing a small scale plating prototyping facility in Carlsbad , S.California.
Tank sizes are 2'x2'x3' deep and some 4'deep. I have planned for a conventional in line manual operated plant , but have been informed that OSHA requirements are that we need to brace the tanks to comply with our being in an earthquake area.
At every 4th tank we would need a brace running diagonally from tank side to floor level.
This would mean that after every 4th tank in the line the operator would need to step back to clear the brace (or trip over it!).OSHA don't seem to think this is a hazard!
If anyone has suggestions as to alternative methods of bracing which would be OSHA compliant we would appreciate your input.
- Carlsbad, California
2006
I am responding without the benefit of knowing your layout or existing tank set-up.
Assuming the diagonal brace requirement is to prevent movement of the tanks during a seismic event would it be possible for you to use a common brace (angle, or channel) for the length on the line and then diagonally brace to the floor at each end?
What is the reason for OSHA requesting the diagonal brace at every fourth tank?
Process Design Group - Hickory, North Carolina
2006
Raymond
I'm guessing your tank height to footprint ratio is what is triggering OSHA's concern. If you were to secure the tanks together (mechanically attach using the tank ribs), you could achieve a structure that could not tip or fall.
In San Jose during the Loma Prieta earthquake, our 6'L x 3'W x 4'D rinse tanks lost about 25% of their volume from the earth movement. The chemical tanks were covered with a plastisol'd tarp and had virtually no loss. Portable dye tanks (55-gallon round) on castered dollies had the ground move underneath them- they lost no solution. You might consider covers while you're at it -- heat savings as well.
Best of luck
- Colorado Springs CO
2006
What is probably required is proactivity--recognition of seismic dangers and the need to design for them--rather than relying on an inspector to spot a danger and react with his first thought about how to address it.
I, too, have not seen your layout but am aware of the need for seismic bracing in California. Usually this can consist, per my recollection, of just bolting the tanks down securely. You bolt a tank base to the floor and then you bolt the tanks to the base. Seismic bracing is about preventing damaging vibration like the tanks shaking off the bases, falling over, tearing up the piping, etc. Buildings that stand hundreds of feet tall do not require triangulation back to the ground as long as they are sound steel structures which are tied into the earth, and I wouldn't think that tanks require triangulation to the ground either if they are tied securely to the ground. The "every fourth tank" is probably an interpretation related to a general building code that every fourth bay of a structure requires lateral bracing. Get a good book on seismic bracing, look at the applicable pages, plan accordingly, and I think OSHA and other inspectors will be happy to have the design onus back on you rather than them.
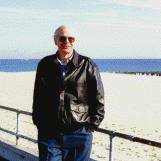
Ted Mooney, P.E.
Striving to live Aloha
finishing.com - Pine Beach, New Jersey
2006
Thanks to all who responded. Essentially we have ended up with Rick Hall's suggestion and have diagonal bracing at each end.
The previous would have been "overkill".
- Carlsbad, California
2006
Q, A, or Comment on THIS thread -or- Start a NEW Thread