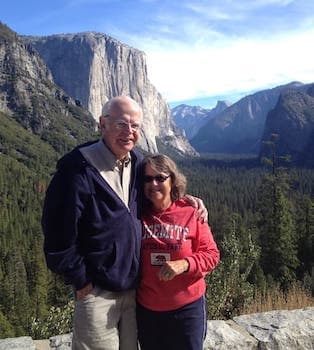
Curated with aloha by
Ted Mooney, P.E. RET
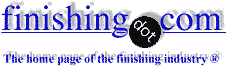
The authoritative public forum
for Metal Finishing 1989-2025
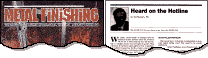
-----
High Electrical Relay Insertion Force
We recently encounter problem with high insertion force when assembly the electrical relays to our electronic modules. The relay has 5 legs (2 made of brass and 3 made of copper)THe copper ones were plated with silver and tin plated for the brass.
Normally, we see the insertion force around 70N, but when using a particular lot date of relay, the insertion force goes up and is above 100N. We swapped the relay on the same part, the result was the same, one is still required higher insertion force than the other. This told us the problem might not be not from mating part. We checked all related dimensions of the relay (such as lead and material thickness) between good and bad relays, but we could not find any difference. We were suspecting the plating thickness were different(thicker cause higher insertion force?) and that is being done at this moment. So could any of experts in this forum let me know any other possible difference between the 2 relays which make one harder to insert than the order. Thank you very much for any of your information and help.
Automotive - Atlanta, Georgia, US
2006
Looks like you already have the root cause, so why wait? You can test the plating thickness of both Ok and not ok parts immediately to begin with or you may want to look at the ductility of unplated parts as well; sometimes non- ferrous parts need to go through a long baking procedure before plating in order to soften up. Your parts incoming to the plating process also need to be of uniform hardness.
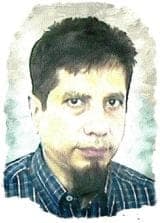
Khozem Vahaanwala
Saify Ind

Bengaluru, Karnataka, India
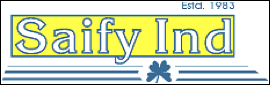
2006
Q, A, or Comment on THIS thread -or- Start a NEW Thread