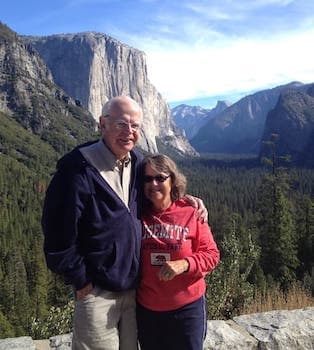
Curated with aloha by
Ted Mooney, P.E. RET
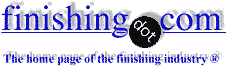
The authoritative public forum
for Metal Finishing 1989-2025
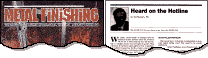
Thread 395/96
Corrosion Resistance for Conversion Coat (MIL-C-5541 Class 1A)
2006
Hi, I am process engineer for aerospace industry. Recently, I have failed to pass salt spray test for colored chromate conversion coat per MIL-C-5541 Class 1A. We are using Alodine 1200S for this process and I think all of our parameters are reasonable (i.e., solution chemistry, immersion time, operating temperature) and meet the requirements for our customers.
I really want to know what kind of variables are affecting corrosion resistance of this process. For your reference, the appearance of processed parts or specimens are very good.
Have nice days !
Aerospace - Busan, Korea
publicly reply to D.Y.Yoo
Just like with making plating stick, the pretreatment has to be reasonable and suited to the alloy being treated. As with most aerospace firms, most of the parts are made from 6061 or 7075 alloys and thus our pretreatment lines, etches, desmuts, etc. are designed to handle those alloys. However, most specs call for the corrosion resistance test panels to be made from high copper 2024 under the premise that if you can pass salt spray on this alloy with known poor corrosion resistance, all other alloys are a snap. The problem is that one needs very specific desmuts (and little if any etching) in order to pass 168 hour salt spray! Stop looking at the chromating solution and what the panels look like coming out - it's all in the prep!
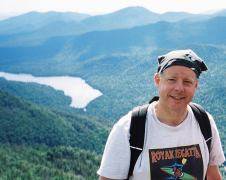
Milt Stevenson, Jr.
Syracuse, New York
2006
publicly reply to Milt Stevenson, Jr.
2006
Very difficult to give you a clue if we do not know what these operating parameters are.
Various influences on corrosion resistance that I have found include drying temperatures and times, concentration of dissolved Aluminium in solution, quality of etching prior to coating, solution pH, general quality of pre-cleaning, state of test panels prior to processing (i.e. corrosion already present) etc.
You haven't told us what you have looked at as potential causes so we can really only talk in generalisations at best.
Aerospace - Yeovil, Somerset, UK
publicly reply to Brian Terry
2006
Hello, everybody! Thank you for your ideas and for your further review,
1. Our operating parameters are;
Concentration of Alodine 1200S : 1~3 oz/gal
pH : 1.3~1.8
Immersion Time : 1~3 minutes (80~90 seconds, actual)
Solution Temperature : 60~100ยขยต
Dry Temperature : 160ยขยต max. and,
2. Pre-treatments are;
Vapor Degrease with Trichloroethylene,
Alkaline Clean with Turco 4215NCLT medium soak cleaner for 10~15 min.,
Deoxidize with Amchem 7-17 deoxidizer for 10~15 min.
Thanks again !
- Busan, Korea
publicly reply to D.Y.Yoo
First of two simultaneous responses --
The single most frequent reason for failing salt spray is the panel itself. First inspect the panel with a 10X loop. Every pit you see is a failure. The copper in 2024 migrates (walks) to the grain boundaries. Old 2024 will NEVER pass salt spray. Find some fresh new perfect panels.
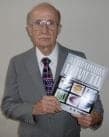
Robert H Probert
Robert H Probert Technical Services

Garner, North Carolina
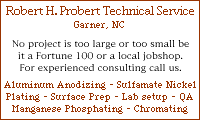
2006
publicly reply to Robert H Probert
Second of two simultaneous responses -- 2006
My first thought is that your drying temperature is far too high. You should not dry chromate coatings above 140F, and preferably not above 130F. The heat at 160F will dessicate the coating, thus rendering it ineffective as a corrosion resistant coating.
I would also look at your Alodine pH range. It may be that a pH nearer 1.6-1.8 would be more effective.
The rest of your parameters look typical for a chromate conversion coating line.
Only one other thing that can commonly cause a problem and that is the condition of the test pieces before processing. If there is corrosion in the test piece before you start then more than likely the test pieces will fail corrosion resistance. The deoxidiser is not enough to kill off the corrosion so you are left with initiation points even before you are in the Alodine tank.
Aerospace - Yeovil, Somerset, UK
publicly reply to Brian Terry
Q. I want to ask to Brian Terry,
what is the max. acceptable concentration of dissolved Aluminium in Chemical conversion coating solution?
Aerospace - Turkey
May 16, 2012
publicly reply to D Deniz
Q, A, or Comment on THIS thread -or- Start a NEW Thread