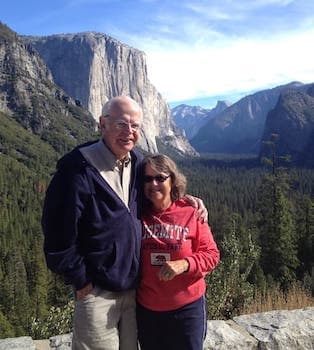
Curated with aloha by
Ted Mooney, P.E. RET
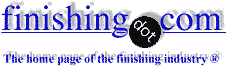
The authoritative public forum
for Metal Finishing 1989-2025
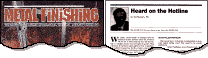
-----
Phosphating salt spray life
Q. We have been asked by a client to zinc phosphate a steel bar that should at least resist 72 hours of salt spray. The process we have at our facility is as follows: soak clean, rinse,electroclean, rinse, zinc phosphate (45 minutes), rinse, chromic seal (30 seconds), rinse and soluble oil (1 minute) as a final step. With this process we have no problem getting 72 hours of salt spray, but now our client wants that the parts not to feel greasy or oily to the hand touch, and this can be achieved in two ways: by spinning the parts or baking them, but after either of these two processes the salt spray resistance drops below 72 hours.
Do you have any idea of what are we doing wrong, what can we do to get the correct resistance?
Thanks in advance
Guillermo Luna- Mexico City, Mexico
1996
A. Hi, Guillermo. You can try other brands or types of oils or waxes to try to find one that doesn't feel greasy to your customer. But it is the oil/wax that imparts the corrosion resistance.
Whether you bake it off, spin it off, or remove it some other way, if you remove it you are not going to pass the salt spray test. In real-life, the nice crystalline structure of the zinc phosphate coating will absorb corrosive water if you don't let it absorb oil.
Regards,
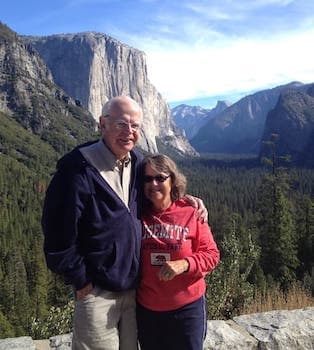
Ted Mooney, P.E. RET
Striving to live Aloha
finishing.com - Pine Beach, New Jersey
A. Please give a thicker zinc phosphate coating hot and passivate and do not heat more than 80-90 degrees.
Harish Chitkarasynthetic polymers - Chennai, Tamilnadu, India
2006
Multiple threads merged: please forgive chronology errors and repetition 🙂
Phosphate coating salt spray specification
Q. I would appreciate if anybody can suggest a salt spray specification for an iron phosphated component having a coating weight of 30 mg/sq. ft to 60 mg/sq.ft.
This will be a great help to me, thanks.
Sivakumar Balasubramanian- Hesston, Kansas
2002
![]() |
A. Hi S.B., Are you talking about the salt spray resistance of phosphated, unpainted metal? If so, then the expected exposure time before the entire surface is completely corroded will be on the order of minutes. The amount of coating does not matter. George Gorecki- Naperville, Illinois 2002 A. The more important factor is what type of coating will be going over the phosphate. With a chromic seal and a good powder coat, you can get 1000 hrs. Dan Brewerchemical process supplier - Gurnee, Illinois 2002 |
Phosphate & oil salt spray performance
Q. Having trouble with corrosion protection with phos/oil. Coating Gr. C prevailing-torque locknuts and nylon insert locknuts with .00025 zinc then 1000 mg/sq ft phos oil but parts will not pass ASTM 72-hr salt spray. Is phos/oil supposed to give that strength of corrosion protection? Past experience in locknuts industry (40 yrs) have had OEMs use phos/oil as lubricant on bearing retainer applications for transmissions, but now having trouble getting parts to pass salt spray test. Would appreciate info as to whether this type of coating is supposed to withstand 72-hr salt spray or is spec asking too much?
Bob Jarman- Niles, Illinois
2003
A. It sounds to me like a combination of poor phosphate coating and an inferior oil sealer. With your specified coating weight, you should be able to get well in excess of 100 hrs with a good oil. Make sure your metal finisher is giving the specified coating weight, and then shop look for a better oil.
Dan Brewerchemical process supplier - Gurnee, Illinois
2003
A. Hi,
I've same thought as the previous comment. Phosphate, in nature, has pretty poor corrosion resistance. It's a little difficult for phosphate to withstand SST of an hour or two. The protection to the metal substrate is highly depend on the oiling/greasing apply on the phosphating.
Good luck.
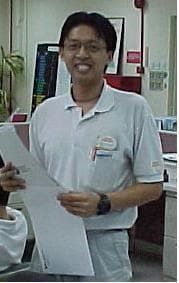
Chee Hong, Lee
- Singapore
2003
Salt spray test of CR steel with only iron phosphate coating?
Q. Could anyone tell the normal hrs of salt spray test on CR steel with only iron phosphate coating? We are producing steel tubes where I.D. could not be powder coated.
Stanley B- Hong Kong
2005
A. Hi Stanley,
The exposure time for unpainted, phosphated CRS before the onset of massive corrosion can be measured in minutes. Your phosphate coating is meant to be used as a pre-paint treatment, not as a stand-alone treatment.
- Naperville, Illinois
2005
Q. Hi, George,
Yes, I understand. We will powder coat the tubes after pre-treatment. But the inner wall of the tubes won't be coated. Therefore, I am trying to find out the maximal protection from phosphating. I am also looking for a low cost treatment to the inner wall to minimize corrosion.
- Hong Kong
2005
Salt spray life of manganese phosphate
Q. If we do 5 micron thick Mn-Phosphating on steel part, what should be the Salt Spray Test Life in hours for the part ?
What is the alternate method to check whether the Mn-phosphating is Okay?
auto industry - Noida, UP, India
2006
![]() |
A. Tarun, Aerospace - Yeovil, Somerset, UK 2006 A. Dear Sir, - New Delhi, India 2006 |
Q. Dear Sir,
What is relation between coating thickness and surface finish in Mn Phosphating? Also for 10-20 micron thickness, what would be coating wt (grams/square meter)?
- Mumbai, Maharashtra, INDIA
2006
A. Phosphating without post treatment, i.e., rust preventive Oil/Grease/Paint, has very little salt spray life. Based on end application post treatment to be carried out. Please refer ISO 9717: phosphate conversion coating on metal for application, salt spray life requirements.

Hemant Shah
switchgear industry - Vadodara, Gujarat, India
April 11, 2012
Phosphating Salt spray test vs. actual performance
Q. One of our customer end OEM's, found the phosphate coated clip rusted on vehicle. The salt spray test requirement given by customer is 6 hours to red rust . The supplier says phosphate coating can never give assurance more than 6 hours.
So my Question is, is it true that salt spray test and actual rust life are anyhow related; and what can be the reason behind such rust?
- pune Maharashtra India
July 8, 2015
![]() |
A. Hi Deepa, Aerospace - Yeovil, Somerset, UK July 8, 2015 A. Deepa, ![]() Ray Kremer Stellar Solutions, Inc. ![]() McHenry, Illinois ![]() July 8, 2015 |
Q, A, or Comment on THIS thread -or- Start a NEW Thread