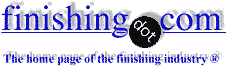
-----
Need Inexpensive Process to apply Mil-A-8625, Type III, Class 2 Anodize to Interior A356 Aluminum
Hello,
I am looking for an inexpensive process / technique to apply
MIL-A-8625 / MIL-PRF-8625
[⇦ this spec on DLA] black anodize to the interior of a sand cast aluminum chassis made of A356 aluminum. Need to prevent coating of exterior for thermal performance reasons.
Chassis is about 36 inches long by 10 inches wide by 8 inches deep.
Target cost is less than $15.
Thanks very much for your help and consideration.
Electronics - Minneapolis, MN, USA
2006
I wish you the best of luck, sir!
You are asking for a HARD black anodize, and what sounds like some detailed masking of the external surfaces. This will probably cost you a bit more than $15 for the part as you simply describe it.
metal finishing - San Jose, California, USA
2006
First of two simultaneous responses --
Depending on the racking AND the masking, I somewhat doubt that you can get dyed sulfuric for that price on the East Coast either. Do a lot of checking and have a few sample parts done before you jump in with a big contract. It can be well worth spending a couple of hundred dollars to have a good idea of what you are going to end up with.
James Watts- Navarre, Florida
2006
Second of two simultaneous responses --
That's quite the tall order, Jim. You've got fairly large part made out of an alloy that's difficult to anodize, and you have what sounds like some extensive masking involved. Under $15 for anodizing just isn't feasible. For that price, I'm thinking the best you'll be able to do is spray paint the areas you'd like anodized. To have something like that professionally anodized will probably cost a minimum of around the $150-$200 range (just a rough estimate).
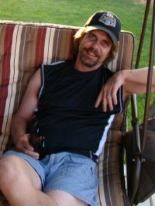
Marc Green
anodizer - Boise, Idaho
2006
First of two simultaneous responses -- 2006
Thanks to everyone for your responses and opinions.
I very much appreciate it!
Best Regards.
- Shakopee, Minnesota, USA
Second of two simultaneous responses --
My company does quite a lot of anodizing of 356 castings. If your product can tolerate significant variation in the finished product and you can find someone who can meet your price point, then you have a chance for success. Otherwise, my advice would be as follows:
1. Explore another method - I'm sure the part can be painted more cost effectively if paint can meet your needs.
2. Castings as a class of materials are notorious for inconsistent results when anodizing. You can experience significant differences in the final finish from lot to lot, part to part, and often even in different areas of the same part. These differences can be visible even before application of the dye which will tend to accentuate those differences even more.
3. The inconsistent finish is generally a result of two phenomena - the grain structure left behind as a result of the casting process and variations in the amount of silicon distributed on the surface of the casting. A356 has a very high silicon content relative to other commonly used aluminum alloys. An aggressive etch applied prior to the anodizing step containing fluorides can help with the silicon problem and may help to "even out" the finish. Unfortunately, aggressive etching of any aluminum alloy can also accentuate the grain structure which may have the opposite effect. - One more note - sand castings display the worst problems with regard to this problem, in my opinion.
I hope this has been of help - anyone who has fought the problems of anodizing castings, particularly dyed castings, can testify to the inherent problems with the process.
Defense Contractor - Dallas, Texas
2006
Q, A, or Comment on THIS thread -or- Start a NEW Thread