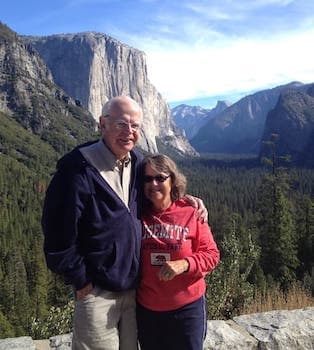
Curated with aloha by
Ted Mooney, P.E. RET
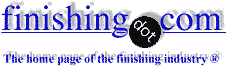
The authoritative public forum
for Metal Finishing 1989-2025
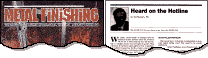
-----
Metal chips
I'm handling copper nickel barrel plating somewhere in Philippines. Our prevailing rejection is metal chips that occurred mostly on the inside portion of the emboss/air pocket. we've done so many countermeasures such as cleaning of copper and nickel tank, electrotreatment, renewed the degreasing solution, conducted ultrasonic cleaning and controlling all standard parameters . any idea where this metal chips come from and how it was formed?
Redford OlanPlating - Phil.
2006
Are your parts going through an acid bath after the copper plate? If so what type/concentration of acid.
Brad StandiferBarrel Line/ Rack Line operator - Knoxville, TN, U.S.
2006
Yes..We are using Activation Iron prior to copper plating...we are using HCl with 50ml/L as concentration...
Redford OlanSurtec Phils. - Muntinlupa
2006
Q, A, or Comment on THIS thread -or- Start a NEW Thread