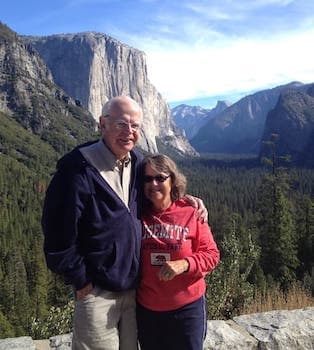
Curated with aloha by
Ted Mooney, P.E. RET
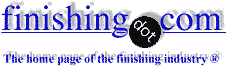
The authoritative public forum
for Metal Finishing 1989-2025
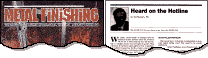
-----
Corrosion Resistance Needed for Steel Stampings with Tight Flatness Requirements
My company provides millions of stamped components to the automotive industry every year, both OE and Aftermarket. We provide mostly a flat product that is 1/4" thick and the weight ranges from 0.5 to 2.0 lbs per part.
Our customers typically powder coat our products for corrosion resistance (they are considered a "wet" part of the vehicle), but there has been a shift to having us supply the parts pre-plated or pre-coated.
In the aftermarket side, we have been supplying zinc dichromate for years, but the hexavalent chromium is a huge obstacle on the OE side. We have tried trivalent platings and trivalent platings with sealer, but have not been very successful due to durability issues (scratches, dings, etc.).
We are now investigating gaseous ferritic nitrocarburization, not so much for the surface hardening, but more for the corrosion resistance and the flat "grayish" color/appearance. However, this process seems to be costly and is very labor intensive (racking/unracking, etc.). Flatness is a very important feature on our products, so right now we are avoiding any processes that involve any type of quenching operation.
Since we are most interested in the protective layer to avoid corrosion, can anyone suggest an acceptable alternative? We are looking for corrosion protection in the 90 to 100 hour range.
Volumes on a single program could be as small as 250,000 per year, or as high as 3 million pieces per year. Volume if we could go across the board on multiple programs could be as high as 25 million pieces per year.
Automotive Stamping Supplier - Toronto, Ontario, Canada
2006
2006
Hello Mr LeRoy;
Your experience with trivalent goes to show that you haven't used the right products yet; there are a lot of wannabe trivalent passivations out in the market admittedly but a lot of very good decent products available as well. A few more trials of trivalent over any zinc alloy will see you cross your very mild requirement of 90 -100 hours.
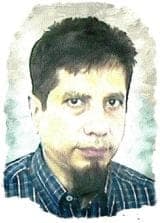
Khozem Vahaanwala
Saify Ind

Bengaluru, Karnataka, India
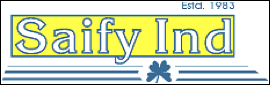
Q, A, or Comment on THIS thread -or- Start a NEW Thread