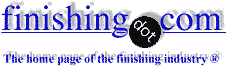
-----
Contaminated 2mm and 4mm drilled holes from machining
2006
I have an aluminum manifold block about 3"x2"x1"
It has several 2 mm holes and 4 mm holes.
The drilling causes a build up of fine metal particles on the walls of the holes, which is difficult to remove.
I have tried ultrasonic, steam, hot water (at mains pressure), air at
120 psi, all of which immediately as soon as the part comes off the CNC.
The only one I've had reasonable success with is ultrasonic, which gets it virtually completely clean if I run it for about 1hr, which is a little excessive.
I notice the particles as a fine grey powder which comes off on the Q-tips
⇦ on
eBay or
Amazon [affil links] that I force down the holes.
These particles come loose over time, and build up inside valves mounted the manifold, causing problems.
Does anyone have any suggestions? Thanks!
Norgren, Pneumatics - Denver, Colorado
First of two simultaneous responses --
If you only have a few types of parts, you could rig up a high pressure jet of water with a very narrow stream and go thru a number of parts in a short period of time with a minimum of automation. Remember in the old days when you would gang drill parts. This would be a number of jets in given pattern for that parts holes. The jets would be lowered a short jet of water would clean out the holes. Raise the jets and move the part to the next set of jets. All behind plexiglas shields and the water filtered.
We did it manually. Also used it to clear chemicals out of holes so that they would not bleed later.
- Navarre, Florida
2006
Second of two simultaneous responses -- 2006
James
Most of the aluminum bores I see prior to anodize appear to be free from the 'contamination' you describe although I have seen some really coarse machinework from time to time. The particulate you describes sounds like the aluminum is tearing rather than cutting. Do you have the same problem on larger bores? Could there be a lack of lubricant due to the smaller diameter restricting access- big bores are easy to flood with a lubricant. Also consider the velocity
(fps)of the outer edge of your cutter.
I think the cutting lubricant, cutter contamination, or feed & speeds could be the cause of your problem.
- Colorado Springs, Colorado
I drill and tap m1 x 0.25 holes in stainless steel and have had to incorporate a solvent flush needle, then air blast to keep tiny particles from clinging to the threading inside the .75mm drill holes. After many methods of trying to remove all the tiny filings from these holes, I found that using isopropanol helps "float" any oils and filings so that the air blast cleans the holes out completely. I use a squeeze bottle designed for methylene chloride for plastic bonding which has a 28 gauge needle on the tip to spray deep into the holes.
Hope this helps ya!-Jeff@HoleJoy!
- Kelowna, B.C. Canada
2006
Q, A, or Comment on THIS thread -or- Start a NEW Thread