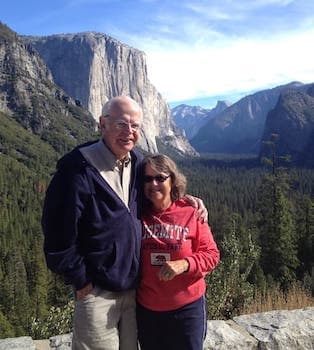
Curated with aloha by
Ted Mooney, P.E. RET
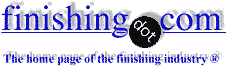
The authoritative public forum
for Metal Finishing 1989-2025
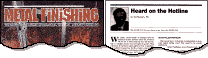
-----
Plasma Nitriding on Steel Tubing
2006
We're trying to achieve a hardness of 65-70 Rockwell C on the outside of a set of steel shafts approximately 40" long for a pneumatic-knife cutting application. The shafts range from 1"-4" in diameter and must weigh less than 40 lbs., so the trick on the larger OD ones is they have to be hollow to make weight. The hardness depth isn't necessarily important, but it has to hold up to a 55 Rockwell C knife-edge cut in 25 places across the length of the shaft.
We looked into thermal spray, but the process and all the machining before and after treatment was very costly. It seemed like the most logical solution was plasma nitriding: it's cheap, the low temps prevent distortion across the long length and thin wall (about 3/16" on a 4" hollow shaft), and it doesn't require a finish grind after treatment. We tried a set using stainless at the hardener's recommendation. The shafts held true in nitriding but hardness was spotty-some spots failed on the first use, and follow-ups revealed that the hardness wasn't there and stainless probably was the wrong material to use. The heat treater's next recommendation to achieve better hardness was a material called Nitralloy, which is apparently made with nitriding in mind, but to get a piece of tube it seems we have to buy expensive solid rod and gun drill it to get the weight down. That's very expensive and wasteful, but I can't find Nitralloy in a tube....
Is there any other material that might work that's more readily available or less expensive? Is nitralloy available in a tube anywhere? Should we be looking at a different process entirely? Any suggestions would be appreciated. Thank you!
paper tubes & cans - Chicago, Illinois, USA
You say that the hardness depth isn't necessarily important. A PVD coating such as TiN would be very uniform and its hardness above your goal. But less than half a ten thousand thick. Thin dense chrome is about 10 times thicker. Still not enough? Thickness is one of the most important parameters to choose a hardening process. Among many variables, it is specified according to the exerted forces, hardness and size of the elements that will try to cut through it and the expected surface quality and life. If there's a possibility of subsequent dressing or lapping, the dimensional tolerance needed and the average depth of damages define the number of reworks for a total life. Hardness layers can be put on top or built into the substrate.
Guillermo MarrufoMonterrey, NL, Mexico
2006
2006
Thank you for your comments.
By the thickness of the hardened surface not being important, I mean this: The only parameters are that the coating stand up to an air-pressurized knife blade (approx. .005" thick) at 40-60 psi and not crack, chip or otherwise wear. If that can be accomplished with a TiN coating at .00005", then that's great. If TiN is prone to failure under pinpoint pressure, then we'd need to look elsewhere.
I assume at that minimal thickness the TiN coating is applied without any subsequent finishing? Would we expect to see the same type of finish as on, say, a TiN-coated drill bit? We don't need an ultra-smooth finish, but something on the order of a stock Thomson shaft--we can't have any tangible roughness.
- Chicago, Illinois, USA
Jonathan,
Both TiN and TD Chrome will replicate the initial surface finish with accuracy. Even mirror polished surfaces are coated with minimal or no post finishing. Now, your pinpoint pressure concern is a good question. Adhesion of TiN or TDC to most metals and alloys is excellent so it will not flake if properly done. But don't forget a hard coating is like a sheet of glass. Put it on a flat floor and it will stand several people on it, but if you put it on a bed it'll break easily. Base metals must have enough hardness to take advantage of a coating's higher hardness. Otherwise, pinpoint loads will break through it no matter how hard. Good luck,
Monterrey, NL, Mexico
2006
Tried the TD chrome and the knives broke through within the first 50 cycles of the machine. Maybe it's too thin... it didn't hold up long at all. On to try a sprayed WC-12%Co coating that should be thicker....
Jonathan Dudlak- Chicago, Illinois, USA
2006
You'll have to find a reliable vendor and your process of choice has to be the new generation of HVOF (anything above 0.003" effective thickness). Unbeatable for your application. Well, only beat by sophisticated electroless nickel with dispersed diamond particles and only when comparison is made against same thickness. But HVOF can go higher. Best luck.
Guillermo MarrufoMonterrey, NL, Mexico
2006
Q, A, or Comment on THIS thread -or- Start a NEW Thread