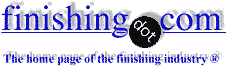
-----
Why do we use 15-18% HCl for pickling
Current posting:
May 4, 2022A. It has often piqued my interested as to why 15-18% appears to be the generally "accepted" or settled at ratio within the industry for HCl in pickling solutions.
However searching and reading papers as to why has lead me to no concrete answer, for a subject so rudimentary I was certain the answer might be somewhere on the internet in black and white. Alas the closest to this subject I find is this discussion thread. Connecting the dots kind of hints to "Gets the job done without having too high of an evaporation rate"
One subject that often is repeated is minimization of fumes, so it appears that the 15-18% area is an acceptable area where fumes are not too bad, and strength of solution is potent enough that it can have a decent amount of use before being too weak.
I have though found a research paper that documented results from experiments on different HCl concentrations and the effect they have on removing material from metal wire across various immersion times. The link is below for those who wish to get the understanding on the basis of this test if I don't summarize it to the letter.
https://ijssst.info/Vol-16/No-5/paper1.pdf
I attach a picture of the graphs of interest:
While the way the paper is worded may sound confusing, it appears each plot on the graph represents the rate of metal removing for that specific immersion interval (e.g from 80-100s, 15mg material removed). So if we were to do some addition and compare how much material cumulatively each HCl concentration removes at say 2 minutes, 4 minutes, 6 minutes etc we can get an idea of the efficiency.
In my opinion, as the concentration of HCl is increased, the onset of material removal right after initial immersion is dramatically increased, however the rate appears to settle down to a median level as time increases and the higher concentrations of HCl somewhat appear to lag behind. The researcher appears to summarize in a comment mentioning that from his observations based on his test, 15-20% is somewhat of an optimal area.
When coupled with the fact that when concentration of HCl is 20% or higher, evaporation rate exponentially begins to get much higher, it does appear like 15-18% seems to be the area that ticks most boxes.
Plater - Perth, Western Australia
⇩ Related postings, oldest first ⇩
Q. Hi. I am a Chemical Engineer who just completed my Masters from SUNY-Buffalo. am currently working with an Indian company who manufactures fume extraction system for the pickling industry. I would like to know, why do we use around 18% HCl for pickling. What will happen if the concentration is too high? How will the finishing be affected if we vary the concentration? Also how was this concentration arrived at, i.e., by experience or experiments or any theory.
Chirag Thakkarfiberglass industries - Mumbai, Maharashtra, India
2006
A. Hi Chirag,
The 18-22% value of HCl in pickling solutions was adopted long ago in the metal finishing industry (not sure of the exact year). My guess would be it was the result of research which involved trial and error. If the HCl concentration in pickling solutions is too high, the metal to be treated could be attacked, worker safety is jeopardized, plant structure and equipment is at major risk. That's where you come in with fume scrubbers!
Best Regards,
process engineer - Malone, New York
2006
Thanks Mark for your answer.
- Mumbai, Maharashtra, India
2006
A. Dear Mr Thakkar,
HCl contains Hydrogen, which leads to Hydrogen embrittlement effect after pickling. Hence For high tensile applications it is generally HCl pickling is avoided, or the concentration is reduced.
Second major reason is Fuming characteristics of HCl. HCl Fumes usually damage the surrounding construction and fabricated structure. To avoid excessive fuming, the concentration is kept on lower side.
Third reason is health related. However the best is your fume extraction system, the fume escapes and creates health hazard. Hence the concentration is kept at lower.
Contrarily, if we keep the concentration too low, then the pickling does not take place, and increases the processing time and cost.
One need to strike a balance between the two and thus this concentration is arrived
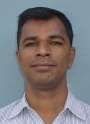
V. G. Rajendran
- Trichy, Tamilnadu, India
2006
A. I agree with V. G. Rajendran and want to add more. Several acids alone or in combination are generally used for pickling. These acids, however, also attack base metal. Thus acid corrosion inhibitors are used. The optimum condition for pickling baths depend on various factors such as concentration of acid, quantity of inhibitor/s, pickling bath temperature, pickling duration etc. A lower acid concentration can be worked out following above parameters.
DANISH JAMAL- Pune, India
2006
A. Dear Mr. Thakkar,
In HCl the chlorine remains in a very unstable form. That why it loses its strength even if it is not in use in open bath.
Being a chemical engineer you understand chlorine in the contact of metal form salts, which act as an electrolyte and promote corrosion.
- New Delhi, India
2006
2006
A. Sir:
If one uses "straight" HCl acid the fumes are extreme for workers and the roof of the factory is quickly destroyed in one year.
If one uses weak HCl then the acid bath lasts only a short time and large volumes of "spent" acid are produced which is very costly.
Good HCl inhibitors reduce fumes for the workers but more importantly protect the base steel after mill scale removal. I published an article in Metal Finishing (magazine) to help people chose a good inhibitor.
The literature indicates that HCl produces less hydrogen embrittlement than sulfuric acid. I have never experienced hydrogen embrittlement with acid pickled steel.
Regards,
Galvanizing Consultant - Hot Springs, South Dakota, USA
Dear Mr.Chirag,
If we use commercial Grade HCl ( 30 - 32 % ) directly for the acid pickling tank for Galvanizing plant, black Materials which is to be galvanized may damages over and above, surrounding area of the Galvanizing plant may with full of Acid fumes and its very difficult to work with this kind of environment. plus structure of the plant may damage. that's why we prefer to use pickling of materials with 18 - 22 % HCl.
Gunatit Builders

Manjalpur, Vadodara, Gujarat
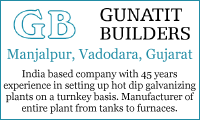
2006
A. Dear's
Chloride containing agent such as HCl, since there is an obvious risk of pitting corrosion, so it is used in that much of 15-18% only.
- TRICHY, TN, INDIA
May 17, 2008
Q. We are manufacturer of steel line pipe and GI pipe. We have a problem with acid fumes. I have heard that there are some chemicals which if mixed with pickling solution reduce fumes. Please guide.
Muhammad Ramzan NoorEmployee - Pakistan
August 25, 2011
Q. I am a trainee Engineer at a cold-rolling complex and looking after commissioning activities at Push-Pull Pickling line of the mill. My pickling line will soon enter into its production phase. 18% HCl will be used for pickling steel strips. I am keen to know what are the factors that effect the pickling time? I.e., the optimum time for which a unit area of the strip should be in contact with acid bath to achieve pickling.
Is there any relation or calculations which can be used, or any thumb rule?
- Karachi, Pakistan
April 23, 2012
A. Time is a function with temp and concentration PLUS metal condition. You may require different times with different lots from the same mfgr.
Typical would be 10 to 30 min with 20 min a common time. It still depends on the variables in the first line.
- Navarre, Florida
April 26, 2012
Q. WHY AFTER INCREASING THE CONCENTRATION OF ACID (HCl), THE Fe CONTENT DECREASES IN PICKLING PROCESS ?
RAM KUMAR Singh- JAMSHEDPUR, India
May 18, 2012
A. Part of the commissioning exercise is to determine the envelope parameters for your process line. You should have an idea of what they are from the original specification, but you need to confirm them under real life conditions. I suggest you run a small pickling bath hold the acid content and temperature constant and run the pickle until the quality of the steel is unsatisfactory. As you do this, I suggest you monitor the total metal content of the pickle acid - remember that pickling HCl often has a base metal content already in it - pure concentrated HCl is about 36%, but industrial concentrated HCl is much cheaper and is 32% and is often contaminated with other metals. I would expect your acid pickle to need regenerating after the metal content increases to between 50-100 g/l and the acid content falls to about 50-70 g/l. You will find that the metal content is more important and this is subject to how free from scale your feedstock metal is. it will also depend on the type of steel being pickled - mild steel will have totally different characteristics to stainless steel. If you are pickling stainless steel, I would suggest using nitric acid and/or hydrofluoric acid.
Increasing the concentration of HCl will cause other issues, for instance, if it is too strong, the fumes will make using it almost impossible unless you have very good extraction. This will of course be complicated by increasing the temperature, as the hotter the solution, the greater the amount of acid vapor...
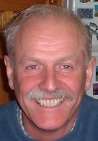
Trevor Crichton
R&D practical scientist
Chesham, Bucks, UK
June 6, 2012
Q. Hello,
I am a new chemical engineer in the metal finishing industry. I would like to know why HCl or sulfuric acid is more preferred over say phosphoric acid for a zinc phosphate coating process for steel.
- Columbus, Ohio, USA
August 16, 2012
A. Hi Kent. I may be misunderstanding you, but I think that is incorrect. HCl or heated H2SO4 are used for pickling because they are more aggressive than phosphoric acid -- but phosphoric acid is used in phosphating processes because the intention is to leave a phosphate conversion coating on the surface.
Regards,
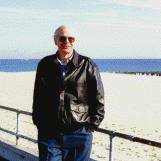
Ted Mooney, P.E.
Striving to live Aloha
finishing.com - Pine Beach, New Jersey
September 2013
Q. Why does HCl acid strength reduce drastically when we pickle mild steel or heat treated angles (example : from 18.5% to 7% in 2 days)
Premprakash Singh- Maharashtra, India
September 17, 2013
A. Hi Premprakash. There are probably two causes, actual chemical consumption and vaporization. HCl is consumed in dissolving rust, so if the components are scaly or rusty, you'll use a lot of acid. The acid also attacks the base steel and is consumed by doing that -- proper inhibitors can significantly reduce that wasted consumption.
HCl also has a very high vapor pressure, that's why it smells so strongly. If quiescent, the evolution of gas will be slower; if sloshed around, the evolution of HCl gas will be extreme. Good luck, and feel free to supply additional details for a more quantitative answer.
Regards,
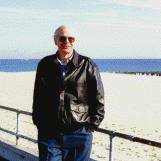
Ted Mooney, P.E.
Striving to live Aloha
finishing.com - Pine Beach, New Jersey
September 19, 2013
A. In addition to the acid consumed in dissolving iron, and iron oxides, and acid lost to vaporization, as mentioned by Ted, there is also the drag-in of water and drag-out of acid into the rinses.
In some cases such as barrel plating or continuous sheet steel pickling, drag-out can be the largest loss of acid.
consultant - Cleveland Heights, Ohio
September 20, 2013
Thanks Lyle. That's something I realized but totally forgot to think about :-)
Regards,
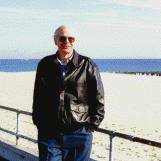
Ted Mooney, P.E.
Striving to live Aloha
finishing.com - Pine Beach, New Jersey
September 23, 2013
Q. Hi
My name is Howard working as Process Technologist for a pickling and galvanising plant.
We are currently using acid life extender and 12% HCl to pickle our wire before galvanising; the problem we are facing now is iron is constantly increasing as the acid decreases. We are running at 100 g/L Fe and 105 g/L HCl -- wanted to find out if we should be worried or we have reached Fe & HCl saturation?
wire industry - vanderbijlpark,Gauteng, South Africa
February 28, 2014
A. It would appear that your pickle inhibitor is not as effective as it should be, either because it is inherently ineffective or it is being used at too low a concentration.
Cal/OSHA is proposing to set an airborne permissible worker exposure level (PEL) of 0.3 ppm time weighted average (TWA) for hydrogen chloride (HCl). If passed, this would be a lower level than 0.4 ppm recently set in California for hydrogen fluoride (HF). Most platers are well aware of the dangers of HF or hydrofluoric acid. This would be a difficult standard for many platers to meet.
For details, see
http://bfksolutions.com/toxic-baby-burp/
which I lifted some of the above text from.
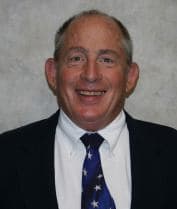
Tom Rochester
CTO - Jackson, Michigan, USA
Plating Systems & Technologies, Inc.

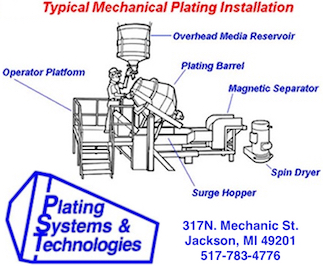
March 5, 2014
![]() |
Why do we want fluorine in HCl pickling acid, and what problems does it causeQ. What is the importance of Fluorine in Pickling Acid such as HCl, and what problems occur when fluorine is present in HCl? Sam Parulekar- Mumbai, Maharashtra India April 3, 2014 A. Hi Sam. Fluorine usually does not belong in pickling acid for steel, although it has some applicability for stainless steel, aluminum, or other metals (usually cast) which contain silicon because fluorine is required for removal of silicon.
Regards, ![]() Ted Mooney, P.E. Striving to live Aloha finishing.com - Pine Beach, New Jersey April 2014 Q. My question was if, in manufacturing of HCl has some fluorine or fluoride content, would it cause any problem to the HOT ROLL COIL or the pickling bath? - Mumbai, Maharashtra India April 6, 2014 A. Fluorides are often used in pickling formulations to remove silica from the surface of the particle being activated or plated. I recently started reading Per Moller's two-volume "Advanced Surface Technology" (https://nasf.org/education/advanced-surface-technology/) -- I haven't finished it yet -- which is quite comprehensive. In Chapter 3, under 'Activation' he mentions that "...iron oxides are complexed with fluoride making it possible for a plated material to be deposited..." ![]() Tom Rochester CTO - Jackson, Michigan, USA Plating Systems & Technologies, Inc. ![]() ![]() April 18, 2014 |
Q. Hi, I am currently looking for ways to reduce or eliminate acid fumes (HCl, H2SO4) from our pickling line. Can I get any suggestion regarding this?
Razin Syamil Zahab- Johor, Malaysia
Fume inhibitor for HCl
Q. Dear !
I am a production GI low carbon wire. Up to now we still don't know a method to inhibit vapor of acid chloride. Please tell me about any commercial chemical that is on sale in world marketing.
We use 12 to 18% HCl (baumé 32)
Thanks
Mr. Lamvo
- HOCHIMINH CITY, VIETNAM
August 22, 2016
A. Hi Mr. Lamvo. I am not familiar with the distribution channels in Vietnam, and we don't print commercial responses in this forum (for one thing, it leads to unmanageable spam), but any of the worldwide plating supply companies like Chemetall, Macdermid, Atotech, Enthone, or Henkel can probably help if a local plating supply distributor can't. Good luck.
I think you should probably have a local fume extraction system (exhaust hoods) and fume scrubber as well as the inhibitor.
Regards,
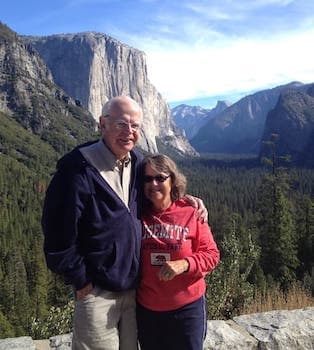
Ted Mooney, P.E. RET
Striving to live Aloha
finishing.com - Pine Beach, New Jersey
August 2016
A. The percentage for 15 to 18% is due to the resulting concentration after regenerating or recovering acid from the pickling process in another process with a fluidized bed regeneration plant or another process. This percent is enough in order to get the result for removing the oxide on the layer. The temperature used should not be greater than 88 °C. If you use a greater concentration with the same temperature, you will face HCl loss by evaporation immediately.
Y Garza- Monterrey Mexico
February 2, 2018
Q. I work in galvanizing department.. which inhibitor may be used to limit the attack on steel.
N m Doshi- Vadodara, India
February 24, 2018
A. Hi Doshi,
If you can't get Dr. Cook's article in the August 2000 issue of Metal Finishing magazine (or at https://www.sciencedirect.com/sdfe/pdf/download/eid/1-s2.0-S0026057600827257/first-page-pdf), you can Google for Rodine, Akzo Armohib (maybe Armohib 28), Columbia Pickle Pal, RI-inhib, Activol 1803, and Stannine LTP for further info. I'm sure there are several other suppliers of pickling inhibitors. Good luck.
Regards,
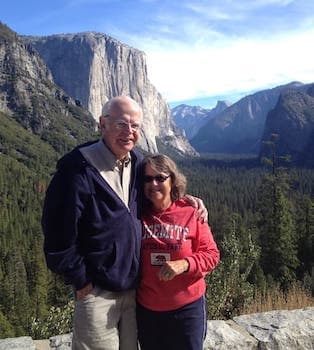
Ted Mooney, P.E. RET
Striving to live Aloha
finishing.com - Pine Beach, New Jersey
February 2018
Q. Hi,
I am Shishir Sable, working for a Fnsteel in the Netherlands. I am busy with optimising our wire pickling lines. We have 5 pickling tanks. The fresh rings comes in the tank with 5% HCl concentration. The rings leaves the fifth tank which has 23% HCl. The HCl % in various tanks are 5, 15, 18, 20 and 23%. Is this type of counter current pickling process advisable? Are there other options?
Recently we did lab trials to add extra FeCl2 in the pickling tanks. That reduces the pickling time by almost 20%. Currently I am busy with upscaling it. What is your opinion on upscaling the lab trials?
best regards
- Rotterdam, The Netherlands
June 12, 2018
A. Hi Shishir! I think this type of counter current can make good results, but I suggest that you, in order to maximize your pickling line productivity, check:
1- Bath temperature: Below 18 °C you will experience reductions of the reaction speed. We have teflon heat exchangers (steam heating system) for that (we have today 4 °C outside so it's a real problem!).
2- Iron content/Concentration: I think all these trials are already made and their results are available in charts. You can check your results with the Kleingarn curve (check https://www.finishing.com/library/campano/kleingarn.pdf). If you have some doubts and an available tank and all you need for your upscaling trial, go ahead!
3- Gap between coils: One of the most difficult problems to solve is the rust between coils. You need to move the coils to make acid clean all the gaps between them, and/or get good wetting agents to improve this.
I think those lines of work, and how you manage to get your best parameters in every one of them, will get you where you want to go in production and quality. They are my three pillars in pickling for our wire process :)
Best of luck! Tell us if you have some interesting results there!
TEL - N FERRARIS - Cañuelas, Buenos Aires, Argentina
June 13, 2018
June 18, 2018
Q. Hi Daniel,
Thanks for your info. I have gone through the Kleingarn curve. My question is validity of this curve at higher temperatures. The curve is designed at 20C. How is the curve look like at 35-40 °C? Does anyone has experience/other literature?
Moreover as I said earlier, we are planning to increase Fe(II) contents in the pickling tanks. I see following options;
1. Pre-mix FeCl2 powder with acid solution is the dosing tanks/buffer tanks which are upstream of pickling tanks. FeCl2 is hygroscopic. So feeding in humid conditions may cause issues.
2. Add Fe powder to HCl dosing tank. It will form FeCl2. But H2 is also formed as a side product.
3. Recycle a part of spent acid. But it contains a number of other heavy elements which are not advisable.
What is the industry practice?
thanks
Shishir
- den haag
June 20, 2018
Q. Hi Daniel,
Thanks for your input.
We do have stable temperature profile between 30-45C in different tanks. My main worry is optimal Fe/HCl concentration in the tanks. The last pickling tank (with fresh acid , 23%) has almost NO Fe in it. The Kleingarn curve suggest that if you start pickling with zero Fe content then you end with sub-optimal pickling till the end of the process.
How do you increase Fe contents of the fresh acid tank? Addition of extra FeCl2 or partial recycle spent acid where the Fe contents are ~150 g/lit? But the spent acid contains lots other heavy metal which may be an issue.
What is your option?
Moreover does someone know how Kleingarn curve behave at higher temp.?
thanks regards
Shishir
Steel - Rotterdam, The Netherlands
June 22, 2018
A. Hi Shishir!
I would recycle spent or acid from the previous tanks to increase iron content. You're worried about other heavy metals, are they alloy elements? If the answer is yes, I wouldn't worry about them.
I would worry if you have large quantities of zinc, if you are doing some rework of galvanized wire, but if you don't I would make this spent acid recycling to increase pickling speed.
About pickling speed around 35-40 °C, they are obviously higher than at room temperature, but optimal concentrations don't change too much. They change with solution activity and I would take this curve as valid with a small correction of speed because of the change in temperature.
This values and curves are measured in laboratory, with controlled solutions and so, and your industrial pickling line, I suppose, has many many more variables in it. Don't take the curve or any other book value as written in stone. You always need to measure what you get and make some experiments in your line to get your optimum parameters, as there are variables not taken into account in these charts.
Sorry if there's something not clearly formulated! It's a complex subject and my technical english isn't good enough!
Best of luck!!
TEL - N FERRARIS - Cañuelas, Buenos Aires, Argentina
Hi Daniel
Thanks a lot for your advise. I am now engineering the recycling option.
Yes all other heavy elements are alloy metals. Cr, Ni and Zn are prominent. We don't rework galvanised products. So it looks like a good solution to recycle a stream from higher Fe content tanks.
I shall keep you update with the results.
Thanks again.
Shishir
- Rotterdam, The Netherlands
July 10, 2018
Q. Please anyone can tell me how many percent of HCl do I use for acid pickling of metal for zinc plating process?
vinay gawade- Mumbai, Maharashtra, India
August 1, 2018
A. Hi Vinay. That's the title and the subject of this page. Please try to digest it and request clarification of any points you didn't understand. And please explain your situation -- have you never done zinc plating before and are in the startup phase, or are you already doing zinc plating and you wish to change the percentage of HCl you are using for some hopefully interesting reason? You say "pickling of metal", but be aware that it can depend on what kind of metal you are pickling or acid dipping. What inhibitor are you using/planning to use? Thanks!
For a deeper understanding you may want to try the search term 'Kleingarn' on this site or elsewhere.
Regards,
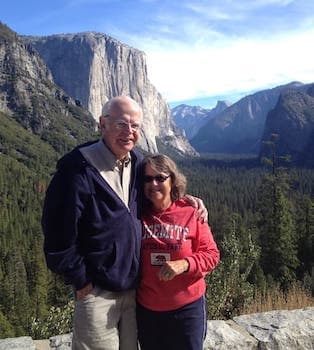
Ted Mooney, P.E. RET
Striving to live Aloha
finishing.com - Pine Beach, New Jersey
August 2018
September 26, 2018
Hi Daniel/Ted,
We did meanwhile many lab scale trials and we could reduce the pickling time by 20%. Great results. We will be carrying out trials in our pickling lines next week.
That brings me to another question on further optimisation. For some of the annealed products we use scale conditioning bath with a solution of KMnO4, NaOH and water. The scale conditioning is then followed by water rinsing and 3 pickling baths. In the new condition, the scale conditioning will become a bottleneck (wrt time). Hence I am looking for options to reduce the conditioning time. My questions is;
1. Is there other chemistry available which is faster and can replace KMNO4 solution?
2. Can we completely discard scale conditioning bath and instead use couple of extra pickling baths (so 5 instead of 3)
Thanks for your advise.
Regards
Shishir
- den haag
A. Hi Shishir!
Scale conditioning bath with KMnO4 and NaOH hasn't so many alternatives. I would try to make this scale removable in HCl, or make the HCl solution more aggressive in order to do that.
We had some problems with some steel grades, but usually we can process without any problem with HCl pickling with some acid degreaser and wetting agents.
Is this an option? If not, you don't have (as my knowledge let's me see) option for this kind of bath.
Best of luck!
TEL - N FERRARIS - Cañuelas, Buenos Aires, Argentina
October 1, 2018
December 12, 2018
Q. Working with one of the largest steel group of India. We are having four acid tanks in our pickling line (Push-Pull type / cascading).
The following is the technical parameters currently being practiced. Is it okay?! Please suggest. We are using acid inhibitor also.
Acid% Iron(gm/L) Acid temp (°C)
Tank 1 (3-8) 200 max 70 - 80
Tank 2 (6-12) 150 max 70 - 80
Tank 3 (10-16) 100 max 70 - 80
Tank 4 (14-20) 50 max 70 - 80
Integrated steel plant - Odisha, India
Recovery of spent HCl
Q. Hi I am Kailash FreeLance Consultant in Steels. Now I am involved with a Project of Recovery of HCl from Spent Acid Pickled Liquor. I am starting from Having A Electro Dialysis Set up for Recovering HCl using an AEM in between SS Anode and MS Cathode. I am starting with 7.47 Amp/cm Sq. Current and Voltage up to 24 Volts. I am using a AEM of Acrylic Sheet of 200 Microns. Has anyone come across this type of Electrodialysis Process, We are planning to Arrive at an Equation for calculation of Equipment Dimensions also from our Prototype. Can I get the know how from any experienced person in this field.
Regards,
Metallurgical Consultant - CHENNAI, TamilNadu, INDIA
September 5, 2019
Q. I am a new chemical engineer. I would like to know why we should test Fe and other elements, and sulphate and sulfide in entrance acid? What problems will happen if those exist in HCl acid that charge in pickling line?
razieh ghgalvanize - Iran, qazvin
September 19, 2019
Q, A, or Comment on THIS thread -or- Start a NEW Thread