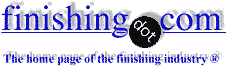
-----
Peel off problem in (lead-free) tin plating on copper
Q. Our plating line recently had a peel off problem on a single kind of device. We are actually plating 4 kinds of devices (transistors, etc.), of course one kind at a time. The other 3 devices did not have any peeling off problems. The frames of these devices are basically the same, copper.
What could possibly cause the peeling off of plating in only one kind, while the others don't seem to have the same problem?
Please teach me, generally, what are the main causes of peeling off on Lead-free electroplating process?
Semiconductors - Binan, Laguna, Philippines
2006
A. Hi,
Check the acid etch process which removes the copper oxide making the surface receptive to plating. The base material is C-194 or C-7025 ?. In C-7025 you may get black smut due to overetching which may cause such peel-off's. At what stage the peel-off was identified ?. If it is in the Form and Singulation stage excessive strain from the tools may be the reason. Any surface contamination may also lead to such problems and try to concentrate also in the deflashing process.
- Chennai,Tamil NAdu, India
2006
A. Hello Melchor,
Considering the substrate metal is exactly the same (copper) on both parts, the problem most likely lies in the pre-clean cycle. What is your pre-clean cycle, and what type of tin plating chemistry are you using? Was this just a one load failure or repeated failures? Please give us more details regarding your process so we can better help you. Thanks
process engineer - Malone, New York
2006
A. It would be worth finding out if that particular copper contained any lead in it that is not reacting to a normal cleaning cycle for starters. There is bound to be a difference in the copper alloy.
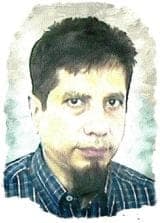
Khozem Vahaanwala
Saify Ind

Bengaluru, Karnataka, India
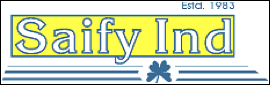
2006
2006
To all,
Thanks for those who responded. Your opinions and suggestions will be taken for consideration.
I agree with what most of you have said that the problem lies on the cleaning process. Our lead-free process (SnBi or Tin-Bismuth) usually have these following stages, in order:
1. Electroclean
2. Descale
3. Acid Dip
4. Lead-free plating
5. Neutralizer
6. Drying
All of the stages have agitation, and rinse in between.
That's basically the flow for all our devices, then we will be surprised at one time, of all the devices that were processed on the same day, one lot of a single kind will have this peel off problem.
We are really bugged by this for so long now.
And just as the same as what you have suggested, improper cleaning of the frames could be the primary cause. And that is what we will be concentration upon.
We even thought of current fluctuation in the plating bath as the possible cause of this peel off, may I ask if it could really happen?
Semiconductors - Laguna, Philippines
A. Hi,
If it is a random failure in bulk, in some acid etch chemicals the dissociation of the catalyst like Hydrogen peroxide may be the reason. As the concentration level of the catalyst goes down, the etch rate will also go down resulting in poor precleaning. Also the dissociation rate is directly proportional to the amount of Copper content in the bath, chemical temperature, agitation. Check the dumping frequency of the bath.
With regard to the peel-off due to current fluctuation, the resultant low thickness will lead to solderability issues only and not peel-off.
Regards,
Semiconductor plating Engineer - Chennai, Tamil Nadu, India
2006
Q. What reason of Tin Plating peel off on Brass material product?
Krishna Sarkar- NOIDA, U.P, INDIA
November 18, 2014
A. Hi Krishna. As you probably know, and as you can see from the dialog which you responded to, troubleshooting such a problem is difficult. Offering a problem with little background information probably won't prove productive, so please try your best to phrase your question in terms of the earlier dialog.
But if you just want the single most common cause of peeling, it's probably inadequate cleaning. Best of luck.
Regards,
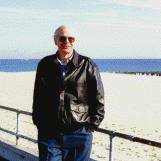
Ted Mooney, P.E.
Striving to live Aloha
finishing.com - Pine Beach, New Jersey
November 2014
A. Ted is right, the most common reason for poor adhesion is poor or inadequate rinsing. However, with brass there is another possible reason -- using a leaded brass. Lead is added to brass to make it more easily machined, but it smears over the surface and makes it difficult to plate. I would recommend a very quick acid etch in ~10% fluoboric acid to remove the lead.
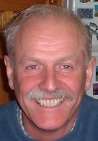
Trevor Crichton
R&D practical scientist
Chesham, Bucks, UK
February 16, 2015

this text gets replaced with bannerText
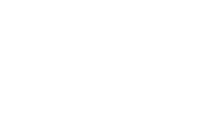
Q, A, or Comment on THIS thread -or- Start a NEW Thread