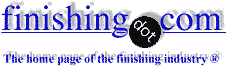
-----
Porosity problem
I have running a aluminium parts for tumbling 20 minutes and after finish tumbling then proceed to prewash 10 seconds with 15 KHZ, then proceed to ultrasonic tank with 68 KHZ (3 minutes)and then DI hot water (3 minutes), after DI hot water will proceed to air blower 60 °C (3 minutes)and also oven with 80 °C (3 minutes).
after completed these process, we have found that porosity problem on the parts. may I know that what is the root cause? thanks,
PIC - Malaysia
2006
2006
Are these die castings? Check for casting porosity by x-ray or cross-sectioning.
Usual causes of porosity are dissolved hydrogen in the melt [need improved degassing] or entrapped air in the mold [need better gating and venting].
- Goleta, California

Rest in peace, Ken. Thank you for your hard work which the finishing world, and we at finishing.com, continue to benefit from.
Porosity in my experience derives from UN controlled oxidation of the aluminum. ie: weathering from storage of stock outside in the elements. I as well am having this problem with some of the parts I am plating. we usually sand down the "porosity ridden" areas of the part in question and strip and replate. this takes care of MOST of the problem, but some porosity remains.
Best Advice: Store all raw material indoors, and purchase from a vendor that does the same.
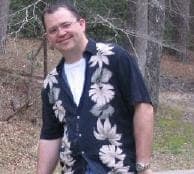
Ryan Cook
Toccoa, Georgia
2006
Q, A, or Comment on THIS thread -or- Start a NEW Thread