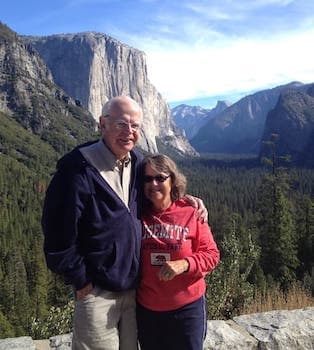
Curated with aloha by
Ted Mooney, P.E. RET
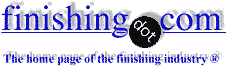
The authoritative public forum
for Metal Finishing 1989-2025
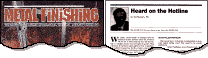
-----
Stripping plastisol from plating racks
Q. I was looking into burning off plastisol from racks but a lot of sources say that this creates very toxic fumes. What are you doing with the fumes while it's in the oven if you are burning off plastisol?
Katie OrtegaEngineer - Green Bay, Wisconsin
November 12, 2024
A. Hi Katie.
I think these folks are talking about burning it in an enclosed oven with an exhaust stack such that people in the factory are not exposed to the fumes. I worked for a plating equipment manufacturer in the 1970's who did plastisol coating and then used this process to remove it when the time came. However, times change ...
I'd be pretty confident that the air quality regulators will not accept this today without "controlled pyrolysis" burn-off ovens which use afterburners to destroy the volatile organics. I don't know if PVC products are okay in such ovens or not.
I think the best way to remove plastisol these days is probably by immersion in liquid nitrogen. Such freezers are widely used in the food industry but I haven't personally seen the equipment and don't know what mods, if any, are needed to employ them as plastisol stripping machines; but there are a number of European manufacturers who employ the approach to strip plastisol. Google "remove plastisol with liquid nitrogen" for a quick review, then if your studies reveal any details, please come back and fill us in.
Luck & Regards,
Ted Mooney, P.E. RET
Striving to live Aloha
finishing.com - Pine Beach, New Jersey
⇩ Related postings, oldest first ⇩
Q. What are advantages and dis-advantages of the different methods for removing the plastisol coating from plating racks?
Which is the best method?
shop owner - Ontario, California, USA
2006
A. Hi, Francisco. Please tell us what you presently do and any issues you have with that method? We find that when posters present their situation and findings they usually get a good response -- probably because readers can learn something from it; whereas when abstract questions are posed, few readers are interested enough to try to help. Thanks!
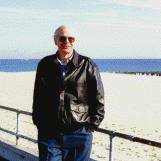
Ted Mooney, P.E.
Striving to live Aloha
finishing.com - Pine Beach, New Jersey
Q. I currently use a burn-off oven to remove the plastisol. Years ago, I used the Methylene Chloride process, but it was too "messy" and since it was harmful to the operators, it was decided to use the burn-off method. The issue that I have is that some of my customers are concerned about the potential degradation of the copper material because of the exposure to high temperatures. After burn-off the racks do not present any visible damage and the copper does not appear to get annealed. We are currently having an independent lab test the behavior of copper under different temperatures and timing to prove the capability of the process. Prior to the testing being complete I wanted to get some feedback from people that have had experience with plastisol removal.
Francisco Cervantes [returning]- Ontario, California, USA
A. Nothing you have said so far would give your customers a cause for concern, unless it is their racks.
Copper is the opposite of steel for annealing or hardening. If you take copper to a high enough temp and cool it very fast, it will go dead soft. If you bring down the temp moderately slowly, copper will harden. So, if you do your burn off in the afternoon, you can turn off the heat and let the furnace coast down and, depending on the temperature reached, it will actually harden.
- Navarre, Florida
! Jim:
I'm not so sure about your explanation of copper annealing.
I have annealed lots of copper by heating to moderate temperatures, say 450 °F, followed by slow cooling.
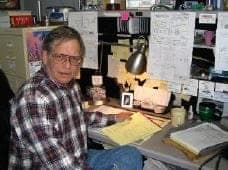
Jeffrey Holmes, CEF
Spartanburg, South Carolina
A. I do not have heat treat books anymore, so do not know the temperatures involved. I was referring to taking it to dead soft, which took quite a bit higher temperature. How much hardness change did you get with a 450 °F anneal cycle?
I thought that most burn off ovens went to above 600 °F, but have zero direct knowledge.
- Navarre, Florida
Q. I set the oven temperature to 490 °F so that it will not exceed 500 °F. The process takes approx. 4 - 5 Hrs.
I do not see any physical changes to the material and it does not appear to be "soft". But I have one customer in particular that claims that copper looses some of its current carrying capabilities and hardness after being heated to ? degrees.
- Ontario, California, USA
A. While there will be some change in the electrical properties of copper after heat exposure, it will be so small for your application as to be irrelevant. Most plating racks are designed to carry more current than they will be used for to prevent any unnecessary temperature rise and thus increasing resistance.
Think about it -- The bulk of the rack is in the process tank, so it cannot rise in temperature but slightly above the tank temp (vs. current carrying capacity in air). Exception is the hook and a small part of the vertical spline(s). A very minor increase in the size of that part of the fixture will more than compensate for any change in the copper.
The customer has far more to worry about the cleanliness of the buss bar and the rack contact points than they would ever find in soft vs. hard copper.
If the plated part meets spec, what is their problem?
- Navarre, Florida
Tip: Readers want to learn from Your Situation 🙂
(little can be learned from abstract questions, so many readers skip them)
Q. I am interested in finding out which is the best way to take plastisol off plating racks. I heard people using nitrogen and some burning it off.
If burning it is easier, what is the temperature? Thanks; whatever info you can send would be appreciated.
Roger
- Waterbury, Connecticut, USA
April 6, 2014
Characteristics, Uses and Safety Concerns"
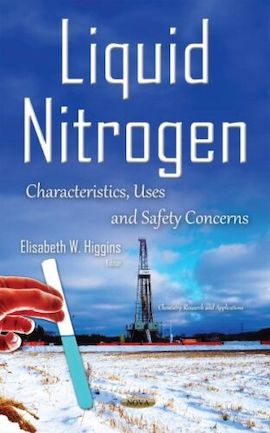
on eBay
or AbeBooks
or Amazon
(affil links)
A. Hi Roger. I haven't heard of using liquid nitrogen personally but it sounds feasible. Have you tried any approaches yourself?
Regards,
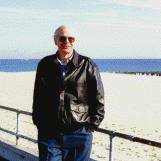
Ted Mooney, P.E.
Striving to live Aloha
finishing.com - Pine Beach, New Jersey
Q, A, or Comment on THIS thread -or- Start a NEW Thread