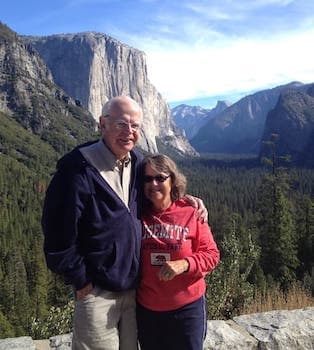
Curated with aloha by
Ted Mooney, P.E. RET
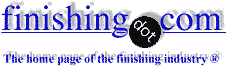
The authoritative public forum
for Metal Finishing 1989-2025
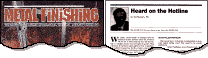
-----
SS got burr after stamping
After stamping, our SS product facing a serious burr problem. How can I remove it and maintain it below 10 micron? Chemical polish ? passivation? any suggestion?
Leonard YongHardware - Singapore
2006
2006
There are several possibilities, all with drawbacks.
Get a better die.
Manual abrasive removal.
One of several forms of abrasive (mass) finishing.
Possibly coining.
Thermally deburring.
Electropolish.
- Navarre, Florida
Thanks for giving me the suggestion.
May I know why chemical polish can not be used in SUS400 series to remove the burr problem? the appearance become dull after the process. Is there any other effect that I haven't detect but will occur?
Hardware - Singapore
2006
Most chemical polish solutions will attack iron and there is a lot of iron in 400 series SS. Add to that a rapid attack it it contains chlorides, even at a low level.
Years ago I saw steel washers that had a chemical polish that looked great, so there may be something that works but may have some unknown limitations. It was made by a rather small chemical firm in Texas, but I can not remember the name.
- Navarre, Florida
2006
Thanks for your information.
Currently, we did using the chemical polisher from Japan to run the precision. This type of chemical polisher is formulated for SS and is to brighten the part as well as electropolishing. For part that is
300 series SS. The result is ok. But it just makes the 400 series SS dull.
For the previous suggestion, we already change the new die but still remain the same. As for abrasive method, it will lead to scratches. It is the most unwanted defect for us as it is a precision part for hardware.
We did try using lubrication oil during stamping, the burr is more serious. Tumbling method is used too but end up with deform defect as the thickness of the part is just 0.01 mm.
Kindly help me brainstorming for the burr issue.
precision hardware - Singapore
2006
If distortion is a problem, I 'd suggest dry organic treated media in a mass finishing system. I've done a lot of critical dimension parts in a small vib at low amplitude with our 6A media for deburring. If you need a mirror finish, follow-up with our 6E for polishing; however, you are talking about long time cycles.
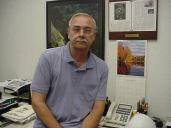
AF Kenton
retired business owner - Hatboro, Pennsylvania
2006
I think beside tooling is very important to produce good SS parts, you may consider asking some good stamping house that beside good tooling, the correct oil use for stamping SS is very important.
You should look at what oil are you using now.
I can see same tooling , which use two different oil.
at the end when correct oil being use, the production can run very well.
- Singapore
2006
Q, A, or Comment on THIS thread -or- Start a NEW Thread