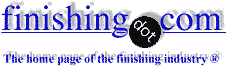
-----
Corrosion caused by incorporation of drag-out?
2006
Greetings.
I'm trying to troubleshoot an apparent plating problem manifested on a tubular bellows-type electroform produced in a commercial shop. the part consists of a nickel-copper-nickel laminate with an exterior gold layer. My understanding is that the nickel is produced by the sulfamate process and the copper is an acid solution. The entire part is roughly 0.0015" thick and roughly 0.180" diameter. The original aluminum mandrel is removed with hot hydroxide. Some time after completion of the part (typically weeks or months) we see the occasional formation of tiny spots (on the order of 0.001") of translucent green material
which is apparently exuding from the interior of the laminate through pores in the exterior gold. elemental analysis suggests that this material contains nickel, chlorine and oxygen. Empirical comparison suggests that it might be a hydrated nickel chloride, and I can only hypothesize that this would be the result of dehydration of entrapped plating solution, perhaps in areas of anomalously high porosity. I'm asking if anyone has experience with this phenomenon or something similar, and if my hypothesis is reasonable, what can be done to minimize the entrapment?
medical device OEM - San Diego, California
----
Editor's apologies! The following photo was provided by Steve with his original posting but was misfiled until ++++++. So, many of the replies below were offered without benefit of seeing the photo the readers are now seeing:
First of three simultaneous responses --
More likely corrosion of the underlying nickel through porosity in the gold. A somewhat thicker gold layer may solve the problem.
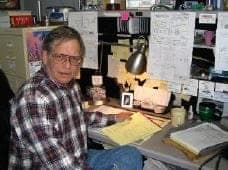
Jeffrey Holmes, CEF
Spartanburg, South Carolina
2006
Second of three simultaneous responses --
Hello Steve,
It sounds as though you did your homework on this problem. Yes, I have seen solution entrapment cause this very problem. The plater I was working with at the time had to install air agitation spargers in the bottom of the 2 rinse tanks after Ni plate and drag out rinse. They then went into a Ni activator, double cascade rinse, pure Au strike, then Au plate. It's important that the post Ni rinses are of a cascading type to minimize Ni concentration. Low current density areas on the bellows shaped part may also be low in Au plating thickness causing a porosity problem. Are the spots confined to one specific area on the parts, or are they sporadic? If they are sporadic I would suspect rinsing practices. Good luck!
process engineer - Malone, New York
2006
Third of three simultaneous responses --
Dear Steve,
This may be due to diffusion.Increase thickness of Gold layer. If it is economically viable,try to plate a flash under coat with palladium as a barrier layer.
If you think it is due to entrapped Ni soln., then try to introduce a final DM water rinse with continues flow and vigorous air agitation. Also increase the rinse time in this tank
Regards
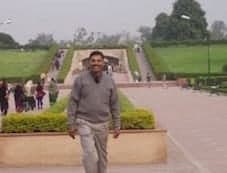
T.K. Mohan
plating process supplier - Mumbai, India
2006
Thanks for all the insights. if I'm looking at incorporation of drag-out (i.e. particularly the low pH chlorinated nickel solution), is it possible that porosity of the nickel could be reduced such that the
only significant drag-out is superficial and easy to rinse off? how does one increase density / reduce porosity in a sulfamate nickel?
- San Diego CA
2006
First of two simultaneous responses --
Hello again Steve,
Incorporation of a Ni dragout rinse couldn't hurt. To answer the second part of your question, as long as you are not co-depositing contaminant metals on the Ni deposit and rinsing practices are adequate, corrosion should be nonexistent. The porosity you are experiencing is coming up through the Gold layer. The least expensive way to tackle this is to improve rinsing, and as mentioned already by respondents, is to increase the gold thickness to reduce porosity. In the unlikely event that none of this works, a pure gold strike under the final gold plate will help reduce porosity as well. Good luck!
Process Engineer - Syracuse, New York
2006
Second of two simultaneous responses --
Steve
It is not that the nickel layer is porous but the gold layer is porous. Please read and understand all the answers carefully.
Regards
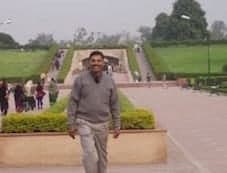
T.K. Mohan
plating process supplier - Mumbai, India
2006
The nickel is in fact porous. I've seen it. Pressurizing this part without the external gold yields a pin-cushion effect ... hundreds of tiny holes. Adding a gold layer seals the part, apparently by plugging the holes in the nickel. What has yet to be addressed is the possibility of incorporation of low pH chlorinated plating fluid within the apparently open lattice of the nickel layer, and whether any resulting reaction between this fluid and the metallic nickel can produce hydrous nickel chloride on exposure to air. Secondarily, what process changes (e.g. additive / current density) might yield a denser nickel without the intragranular spaces which (hypothetically) might be trapping plating fluid?
Steve Yon- San Diego
2006
2006
Hi again Steve,
You speak of hydrated Ni Chloride in the lattice. Firstly, Sulfamate Ni does not contain Ni Chloride. What type of bath is used for the bellows type electroforming? If it is sulfamate Ni, keeping the pH on the low end will improve ductility of the deposit, but the current efficiency drops off some. Get the facts from the Ni bath supplier regarding the use of leveling and wetting agents. You are not giving us accurate information on the plating chemistry that is used, so it is difficult for us to help you.
uses of leveling agents, wetters, etc
Process Engineer - Syracuse, New York
The manufacturer tells me that small amounts of chlorine are added. this is to aid dissolution of the anode material. Additionally, Schlesinger and Paunovic clearly state (pg. 173) that without chlorine, a sulfamate solution requires sulfur-containing anode material to avoid anodic oxidation of sulfamate anions. I've had enough materials experience to know that sulfur incorporated into the electroform produces undesirable mechanical properties. The 'nickel plating handbook' published by the OMG group states (and this is mirrored in Schlesinger and Paunovic) that HYDRATED NICKEL CHLORIDE can be present at up to 10% of the sulfamate concentration. If you don't know the answer to this question, fine, but please don't impugn my understanding of the chemistry or physics.
Steve Yon- San Diego
2006
Nobody impugned your knowledge of chemistry or physics, and your response to a stranger trying to help you is way out of line, Steve. But at least four electroplating experts are telling you that, based on the facts on the table, your understanding may be wrong but that there aren't enough facts on the table yet. Nickel sulfamate plating baths often have no chlorine in them and rely on sulfurized nickel anodes for anode corrosion without any of that sulfur being incorporated into the deposit.
Plato talked of the futility of a man trying to deduce the nature of reality solely from the play of shadows on a cave wall, and it is indeed difficult to deduce the nature of a plating problem solely from a description of some of the features of the finished product.
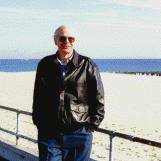
Ted Mooney, P.E.
Striving to live Aloha
finishing.com - Pine Beach, New Jersey
2006
First of three simultaneous responses --
Very well put Ted, thank you.
Steve, I respect the knowledge that you have and the material you have resourced. When you mentioned hydrated Ni chloride and "low pH chlorinated solution", this leads me to believe it was a nickel sulphate solution that was being used. I admit I don't have all the answers, I just try to help fellow platers utilizing the information that is furnished in the inquiry. I hope you solve the problem.
Process Engineer - Syracuse, New York
2006
Second of three simultaneous responses -- 2006
Steve/Mark/Ted
Steve wrote
Quote
"What has yet to be addressed is the possibility of incorporation of low pH chlorinated plating fluid within the apparently open lattice of the nickel layer, and whether any resulting reaction between this fluid and the metallic nickel can produce hydrous nickel chloride on exposure to air. Secondarily, what process changes (e.g. additive / current density) might yield a denser nickel without the intragranular spaces which (hypothetically) might be trapping plating fluid?
Steve Yon
- San Diego"
Unquote
Steve,
I do not think you can possibly incorporate low pH(other than the pH of the plating bath,in the plating bath)plating fluid.If at all it is possible,then you have to incorporate it on the outside of the plated surface.It can be Nickel chloride and HCl mixture which will give lower pH.As such a reaction is probably not possible to produce hydrous NiCl2 on exposure to air to fill in the pore.
All these sound good as hypothetical answer to your hypothetical question.
regards,
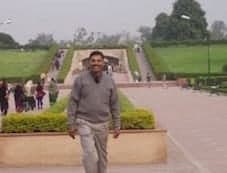
T.K. Mohan
plating process supplier - Mumbai, India
Third of three simultaneous responses --
As another followup, although I am not familiar with gold/nickel/copper/nickel electroforms, I am familiar with single layer nickel electroforms that are helium-tight. So it occurs to me that it is probably a problem indicating faulty electroforming if these bellows are like pincushions until the gold plating.
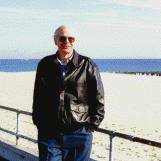
Ted Mooney, P.E.
Striving to live Aloha
finishing.com - Pine Beach, New Jersey
2006
adv.: Supplier of Copper Anodes, Nickel Anodes, Bismuth Metal, & Other Metal Products for Industry & The Arts
Q, A, or Comment on THIS thread -or- Start a NEW Thread