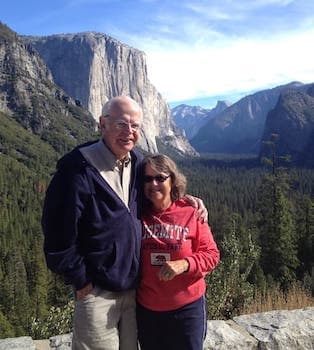
Curated with aloha by
Ted Mooney, P.E. RET
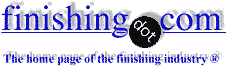
The authoritative public forum
for Metal Finishing 1989-2025
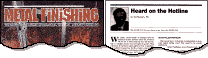
-----
Phosphate contamination in sulfuric acid anodizing
Does anyone out there have a good understanding of how the total phosphate level in a sulfuric acid anodizing tank can affect the performance of the solution? At what level of phosphate contamination are problems seen? Can the solution be saved by any method or is dumping at a certain level the only answer?
Victor Waldmanmetal finisher - Naugatuck,CT.
1999
do you mean build-up of aluminum, not phosphate?
Bill Hemptech svc. w/ chemical supplier - Grand Rapids, Michigan
1999
1999
I knew part of this answer but didn't know the level at which problems occur, but I just found a source that says that above 1000 ppm phosphate a "soft" film is obtained which is difficult to seal. That makes sense, as the oxide is known to be more soluble in phosphoric acid than in sulfuric acid, hence the pores at the surface of the oxide would tend to be conical in shape rather than cylindrical, and as a result would be difficult to plug up by sealing.
Unless the problem is severe enough to invest in ion exchange equipment, it is probably cheapest to dump the solution. If this a recurring problem you need a long term solution, to eliminate the drag-in. If the phosphate is coming from bright dipping, you should have at least three rinses, preferably one still and two countercurrent flowing rinses between bright dip and anodize, and a lot of up-and- down rinsing in each. If you look closely you can often see the viscous bright dip solution hanging on the parts. Rinsing after bright dip in the winter months can be especially difficult in the north, where incoming tap water can be at 40° or less, and the cold temperatures increase the viscosity of the solution hanging on the parts.
Phil Johnson
- Madison Heights, Michigan
Q, A, or Comment on THIS thread -or- Start a NEW Thread