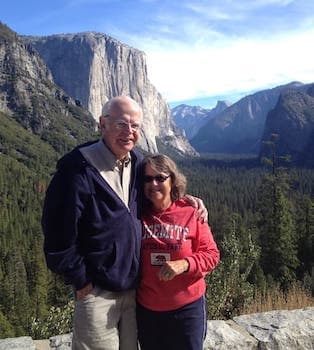
Curated with aloha by
Ted Mooney, P.E. RET
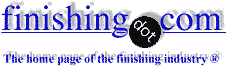
The authoritative public forum
for Metal Finishing 1989-2025
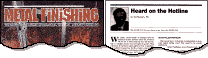
-----
How could I get a flat finish to hard anodized aluminum parts
2006
I will be having intricately machined aluminum parts hard anodized in a natural color. I have gone to great pains to machine the parts with machine tool marks that are pleasing to the eye. The parts are going into a consumer product. The machine tool marks are too shiny for my taste. I want to find a way to dull the surface of the aluminum just slightly before it is hard anodized. The goal is to end up with a flat gray color.
Blasting and sanding are too aggressive and not what I am after. I need the surface dulled but not changed to the extent that the machine cutter marks are not visible. I am wondering if here might be an etching process with an acid that would do the trick. Any thoughts?
Sincerely,
machine shop manufacturer - Quakertown, Pennsylvania, USA
Aluminum is often, if not usually, caustic etched to a matte finish before anodizing. You probably will need to run a series of test parts to determine how much etching you want to do.
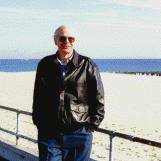
Ted Mooney, P.E.
Striving to live Aloha
finishing.com - Pine Beach, New Jersey
2006
I tried etching the aluminum myself and it worked very well to dull the shine. Thank you for your recommendation. However I have another complication. The part I etched went in to the anodizer with another part I did not etch. The anodizer etched both parts (their normal etching process) and returned the completed parts to me. Well the crystalline grain in the aluminum showed through on both of them. It is such a strong effect that it is completely unacceptable. I was told I have received cheep aluminum (6061) and should report the problem to my aluminum supplier.
Meanwhile, I have 150 of these parts that I can't have etched as part of the anodizing process. I do not mind that so much as they will be usable even if they are not etched to reduce the shine but, can they be anodized without the etching step?
- Quakertown, Pennsylvania, USA
2006
2006
David
What we have found to alleviate most of the 'crystalline grain' is as follows:
1] Degrease/clean the parts
2] Refinish desired surfaces with green scotchbrite pad and orbital sander
3] acetone
⇦ this on
eBay
or
Amazon
[affil links] Warning! highly Flammable!
or IPA wipe
4] Normal clean without the etch (soap & deoxidizer)
5] Anodize as normal
This has minimized the characteristic to a minimum for us. You can also perform the refinish operation (in addition to) after anodize to further hide.
This does not work well on high luster parts, and you can play with different grades of scotchbrite to achieve different results.
Unfortunately, this is a reactive approach. Best would be to get the
'good stuff' to start with.
- Colorado Springs, Colorado
Acheiving a matte finish on aluminum is done either mechanically or chemically and done daily at my anodizing firm and many others. Abrasive blasting with either glass bead or aluminum oxide works. Hand scratching with an abrasive pad or sandpaper (similar to timesaving or belt sanding) can do the same. Chemically, there are acid-based MICRO-cyrstalline etchants that will give a matte finish as opposed to the widely used, caustic MACRO-etch which brings out the grain structure of the aluminum. "It's in the metal" is an old ploy of most metal finishers - it shifts the blame from themselves and places it back on the material supplier or machinist. I'm not about to say it's always incorrect, but most "metal" problems can be dealt with provided the anodizer is given clear alloy and temper designation and enough information on what the parts should look like following anodizing. Work exhibiting the grain structure is not that uncommon and not always foreseeable. I'd be more than willing to look at what you're getting and discuss alternatives.
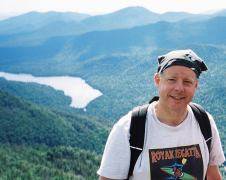
Milt Stevenson, Jr.
Syracuse, New York
2006
While I agree with most of what Milt stated (that there are cures, or work-arounds, to material issues) it's impossible for the anodizer, or the machining facilty for that matter, to know what the material is going to do during processing, untill its processed. All aluminum is not created equal. My company manufactures its own parts that I anodize, and we only use 1 source for our aluminum, the one we've found that puts out the most consistent product.
Most anodizers have process specifications that they follow.The parts are racked, then degreased, caustic etched, ect, etc. If a problem is going to show up, its normally during the etching process. By that point, the damage has been done, and the coater has to either continue the process, or the parts must be desmutted, dried, and re-finished...THEN, the coater can make tweaks to the process.
It's normally pretty easy to solve an anodizing material problem, but forseeing one is an entirely different matter.
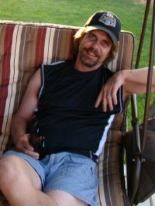
Marc Green
anodizer - Boise, Idaho
2006
I did send six test bodies to the anodizer to be run without the etch process. It went very well. The bodies came back shiny but the marks from the crystalline structure in the aluminum were greatly subdued. It will get me though.
Willie
You can bet I will be using 7075 from now on. Thanks for the ideas. However, I can not physically touch the surface before it is anodized because it has to have the cutter marks intact so it looks like a machined part. It all has to do with the aesthetics I am shooting for.
Milt
What exactly is an "acid-based MICRO-crystalline etchant"? How does it not bring out the grain structure of the aluminum?
- Quakertown, Pennsylvania, USA
2006
Q, A, or Comment on THIS thread -or- Start a NEW Thread