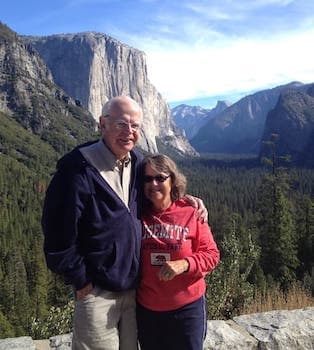
Curated with aloha by
Ted Mooney, P.E. RET
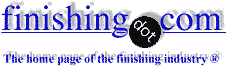
The authoritative public forum
for Metal Finishing 1989-2025
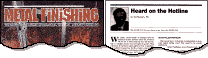
-----
Starting in Electroforming
Q. I have recently discovered Electroforming as a viable alternative to metalcrafting. Since some of the objects are large, tubular or dished in shape and can range up to 36" diameter; Electroforming seems to be a great way to fulfill the gap that was always present in what I was able to do with casting, etc. These pieces are more sculptural in nature and meant to be functional.
I have been trying to consume every bit of information I can find. While I AM RESEARCHING EVERYTHING BEFORE DOING ANYTHING, I did have some softball questions. I am aiming for Nickel, later plated in Bronze or Copper electroforming. The pieces I create will need to be fairly sturdy, could experience some light bending or manipulation and would need to be about 1-2mm thick.
Would Nickel or Copper be best for these applications? There seems to be a fairly standard bath for Copper but the Nickel has a number of baths. So if the answer to the previous is Nickel, which solution for Electroforming will yield the best quality deposit for my application? I am not so much concerned with time to deposit so thick a layer as I have lots of other things to sit around and do while I tend the pot. But the deposit will need to be inherently sturdy with as little pitting as possible.
I know better than to mess around with chemical bottles and try to backyard this stuff but I don't want to spend money twice either. So any straight forward answers to these curiousities can be a huge help in narrowing down the information I need to get in order to start. There is a lot of information out there and I always find links to this forum. So you guys are the answer men. Any help is appreciated.
Spartan Creations - Tucson, Arizona, USA
2006
A. In almost all cases sulphamate nickel is the best solution for nickel electroforming because it can be deposited at zero stress. But copper is softer and may be best if there will be any post electroforming mechanical work.
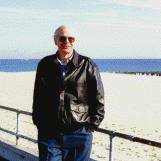
Ted Mooney, P.E.
Striving to live Aloha
finishing.com - Pine Beach, New Jersey
2006
A. Hello Michael,
I agree with Ted's input. Because the electroformed product may be subject to slight bending and manipulation, copper has better properties for post fabrication. If there are a lot of recessed areas that would need close to equal plating thickness as flat surfaces, your copper bath should be formulated with a lower copper metal/ higher acid concentration. I have set up a few sculptors and copper electroformers in the past and found it's best that your prospective copper bath supplier visit you to view exactly what you plan to electroform. They can advise you on the formulation of chemistry, equipment, and share their experience with you. I could give you some tips, but working closely with a experienced tech rep that knows the bath they sell inside and out is the way to go. Good Luck!
process engineer - Malone, New York
2006
Q. Hi. I have been trying to grow 1-2 mm copper composites using electroforming. I am using Nomex (an insulator) as the filler. The filler is form of a felt which is pressed against a copper plate (cathode). I operate at currents ranging between 200 mA/cm^2 - 500 mA/cm^2. After carrying out the process for 10-12 hours using a solution containing copper sulphate ⇦ this on eBay or Amazon [affil links] (200 gm/L) and sulfuric acid (50 g/L) I am able to only deposit up to 30-40 microns of copper. Is it normal? Are there any ways to improve the rate of deposition?
Abhimanyu Bhat- Austin, Texas
April 7, 2013
A. Hi. Faraday's Law of Electrolysis says that at 100% efficiency you'll deposit one gram equivalent weight for every 96,485 Ampere-seconds. The Metal Finishing Guidebook offers a chart that combines some of the constants like valence, density, atomic weight, etc., to conveniently tell us that it takes 17.8 Ampere hours per square foot to deposit .001" of copper from a copper sulphate bath.
You are plating at 200-500 mA/cm^2 for 10-12 hours, which is 186-464 A/ft^2 for 10-12 hours, which is 1860-5570 A-hrs/ft^2, so you could expect a thickness of 2640-7950 microns at 100% efficiency. Yes, plating at 1% efficiency rather than 90%, something is very wrong with your plating arrangement.
Regards,
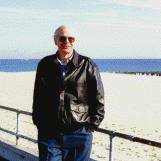
Ted Mooney, P.E.
Striving to live Aloha
finishing.com - Pine Beach, New Jersey
April 10, 2013
A. Just a thought - what is the volume of your solution - have you depleted the solution of the copper and what is your anode?
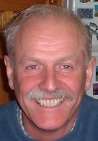
Trevor Crichton
R&D practical scientist
Chesham, Bucks, UK
April 18, 2013
Q, A, or Comment on THIS thread -or- Start a NEW Thread