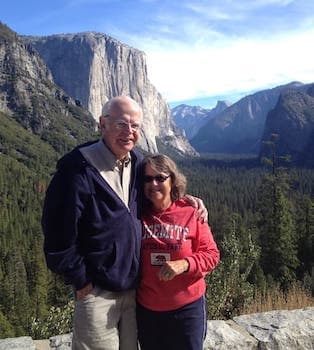
Curated with aloha by
Ted Mooney, P.E. RET
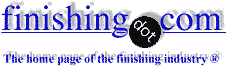
The authoritative public forum
for Metal Finishing 1989-2025
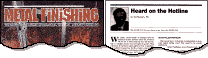
-----
True that cast iron can't be Zinc Plated?
Q. Can anyone advise of a makeup for acid zinc strike solution for cast iron parts, for future plating using alkaline zinc?
Since acid pickle is the first step, won't the acid still leach out of the pores and attack the zinc applied from the strike solution?
Perhaps if advisable could I use an extended time in rinse tank before acid zinc strike.
Thanks.
- Perth, Western Australia
July 15, 2022
A. Hi Boris. Regarding porosity, the best way to plate castings is probably to vacuum impregnate them first, which solves the problem. If that is impractical then rinsing really well will have to suffice. Porosity is just as much a problem with alkaline solutions as with acid solutions -- cyanide bleed-out was a problem long before acid zinc was popularized.
But yes, you should do acid zinc strike before the alkaline plating. Personally, I wouldn't fool with home-brew formulations for the acid zinc; every plating process supplier offers an acid zinc process.
Luck & Regards,
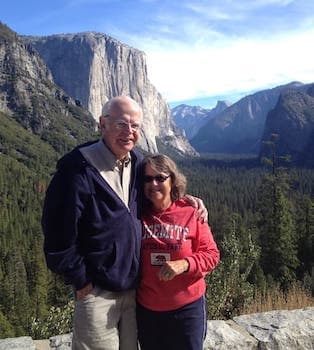
Ted Mooney, P.E. RET
Striving to live Aloha
finishing.com - Pine Beach, New Jersey
Q. The goal here was to see if there is an effective and less arduous way to do a preliminary coating on cast iron parts, so then I can proceed to plate them in my Alkaline zinc tank.
In my alkaline tank, plating with the highest possible current densities do help somewhat with some cast parts, yet still some areas will have badly adhered deposits.
Setting up a separate acid zinc bath may have to be the only way forward before I exhaust all other options. Costs and sustainability rear their ugly head ... that is then more liabilities and maintenance./p>
Boris Siljanoski
- Perth, Western Australia
July 16, 2022
A. Hi again. My question would be: since you need to acid zinc strike them in order to do alkaline zinc plating, why not just acid zinc plate them and be done in one step?
Luck & Regards,
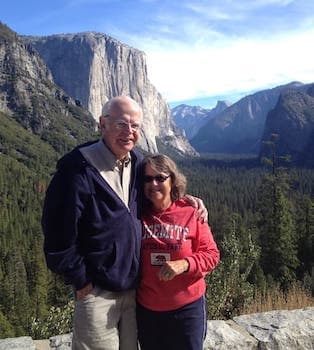
Ted Mooney, P.E. RET
Striving to live Aloha
finishing.com - Pine Beach, New Jersey
⇩ Related postings, oldest first ⇩
2006
Q. Chemistry student at the Budapest Technical Institute working with some plating.
I have heard that you can only plate cast iron, malleable iron and carbo-nitrided steel with an acid zinc plating solution and that you can't use alkaline or cyanide zinc plating solutions. Is this true?
Student - Budapest, Hungary
2006
A. Yes, that's essentially true, Thomas. For reasons which I confess to having never actually studied, the presence of the carbon in alkaline conditions causes the evolution of hydrogen in lieu of the deposition of zinc. According to standard potentials, hydrogen should evolve before zinc deposits, but it doesn't actually happen in acid baths, nor in alkaline baths when no carbon is present. But in alkaline baths with carbon present the "hydrogen over-voltage" is dissipated, and hydrogen evolves instead of zinc depositing :-)
Before the development of practical acid zinc plating in the mid 1970s, such items often would be cadmium plated instead of zinc plating them.
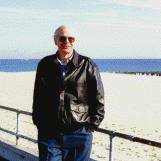
Ted Mooney, P.E.
Striving to live Aloha
finishing.com - Pine Beach, New Jersey
Multiple threads merged: please forgive chronology errors and repetition 🙂
Zinc plating cast iron
Q. In endeavoring to plate cast iron parts with alkaline zinc we are getting good thickness in the high/mid CD but no deposit in the low current density areas.
Can anyone suggest a cleaning cycle, activator or strike to overcome this problem?
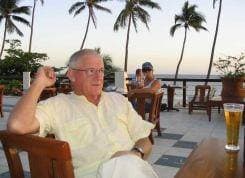
Geoffrey Whitelaw
- Port Melbourne, Australia
2006
A. Hi Geoff. An acid zinc strike should do it, I think.
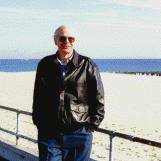
Ted Mooney, P.E.
Striving to live Aloha
finishing.com - Pine Beach, New Jersey
A. A light sandblast will help because after casting it forms a film and at most times it won't plate at low current density areas. Second, you can make up a cadmium strike!
That will definitely work. It covers it immediately!
- South Africa
A. As a zinc plater myself I know the difficulty in plating cast iron especially when using cyanide zinc. But the way I find to get around this is to give it a strike of cyanide copper then use a scotch-brite to rub the surface down and it should zinc plate fine.
Michael Jones- Brisbane, Queensland, Australia
September 29, 2008
Hi again. As we see, although the 3 responders suggested 3 different strikes, they all suggested striking with some other bath because hydrogen is released in lieu of the deposition of zinc where there is carbon; the problem is apparently hard to overcome, especially at low current density.
Regards,
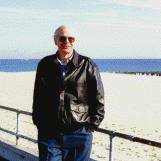
Ted Mooney, P.E.
Striving to live Aloha
finishing.com - Pine Beach, New Jersey
Multiple threads merged: please forgive chronology errors and repetition 🙂
Alkaline Zinc plating on top of Acid Zinc plating for cast iron materials
Q. I am Yamuna from CHENNAI from Plating department . Sir I need a clarification regarding Alkaline zinc plating of the cast iron parts.The above attached component is made of cast iron material MES M - 01 -200 ( FCD450 ).
Kindly let me know Alkaline Zinc Plating Process is possible for the above mentioned component.
My chemical supplier said that Alkaline zinc plating is possible on cast iron by first plating the component with Acid zinc plating then with Alkaline zinc plating .
Please explain.
Thanking You
With Regards
J.Yamuna KanagamPlating shop engineer - Chennai, Tamil Nadu, India
April 24, 2008
A. Dear Ms Yamuna,
It is advisable to use acid zinc before alkaline zinc as cast iron can be attacked easily by alkaline solutions.
Also please do take care of your cleaning process as the job needs to be treated in low concentration of alkaline cleaners.
Maybe two dilute baths instead of a single concentrated one if you need better cleaning.
Regards
All the best,
plating process supplier - Bangalore, India
A. Dear Aurobind Venkataraman,
It is my understanding that cast iron is mainly composed of iron and carbon and neither of these elements are significantly attacked by alkalies. On the other hand, acids attack iron. Could you or someone else please explain to me why or by what mechanism will cast iron be attacked by alkaline solutions and not by acidic zinc? Thanks,
Monterrey, NL, Mexico
A. Hi Yamuna,
Generally Zinc plating on cast iron is done using an acid chloride electrolyte. This is because of the unique leveling property of this bath. Zinc ions from this high efficiency bath try to cover the pits traveling at a greater speed in the first few moments and then start leveling the deposit. So it is advisable to stick to acid chloride Zinc plating on castings. Cyanide/Alkaline bath does not have this property as required to plate cast iron.
Regards
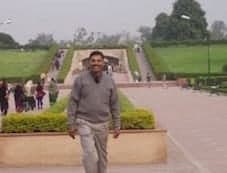
T.K. Mohan
plating process supplier - Mumbai, India
A. Dear Readers,
Since cast iron has lot of carbon the formation of smut is the problem. Further I think Ms Yamuna needs excellent coverage property for her calipers and alkaline zinc is best suited for her.
Regards,
plating process supplier - Bangalore, India
A. Dear Ms. Yamuna,
Acid-chloride zinc process is best suited for cast components like calipers and housings. A few platers give a flash coating of acid zinc and then do alkaline-zinc plating.
Hope this helps.
chemist - Chennai, Tamil Nadu
A. Hi yamuna
As per our experience acid chloride zinc is better than alkaline zinc plating.
The throwing power of acid zinc is high when compare to alkaline.
cast iron is porous component; during acid pickling the acid may get into the gaps of cast iron; because of this the alkaline media won't accept the coating over the cast iron.
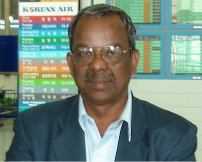
BRIGHT C.MURUGAN
METAL FINISHERS - Chennai, TamilNadu, India
October 29, 2010
Unlike the knowledgable people responding before me, I've never personally plated any such parts; all I have is book knowledge.
I believe that they are all correct in their assessment that cast iron should not be directly alkaline zinc plated, but I think the actual reason is that under alkaline conditions the carbon spots will cause hydrogen to be reduced instead of zinc, leading to poor or no zinc deposition at the low current density areas, and an unsatisfactory porous deposit (if any).
Regards,
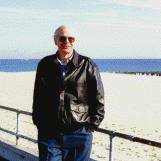
Ted Mooney, P.E.
Striving to live Aloha
finishing.com - Pine Beach, New Jersey
Zinc Plating of Iron
February 7, 2020Q. A request for help from the Finishing.com community.
Background
We are manufacturers of safety critical products which use a high purity iron. The iron is Zinc plated to BS EN ISO 2018:2018. Over the years we've experienced occasional blistering & flaking of the plating. The usual response has been to send the parts back for strip & re-plate.
We've tried other platers over the years, and we've seen similar results, occasional blistering and plating. We've then tried another plater, things are good for a while, then the blistering occurs, we try and work with the plater, nothing gets resolved and we move onto the next. We've been using the current sub-contract plater for perhaps 3, maybe 4 years and it seems the problem has been worse than I have been led to believe. I have been informed by my sub-contractor that the blistering & flaking is now endemic. They cannot guarantee that any plated parts they supply will not blister & flake. Indeed, they are now threatening to not supply parts to us unless we accept that the finish will blister. If I move to yet another plater (if there is another plater left in the U.K.!) no doubt I'll be in the same boat in a few months / years time.
Parts are inspected after plating, they are then held for a minimum of 48 Hrs and inspected again prior to despatch from the plater's premises. When they arrive at my factory they are also inspected. You've probably worked out by now that we are paranoid about blistering & flaking plating.
Questions
1) Is it common for Zinc plating to flake off Iron? Does my high purity (>99.9% Fe) make a difference?
2) What is / are the likely cause(s).
3) What could be done to fully investigate the cause(s)?
4) Is there a body that could assist in any investigation into the causes and eliminate them?
5) Is there another plating I should consider? Nickel?
6) What would be the advantages / disadvantages to for example Nickel or whatever else the community can suggest?
I look forward to hearing the views of the community!
Product Manager - Staffordshire, UK
----
Please also see letter 23909, "Problems in zinc plating of cast iron".
Q. Lots of comments on Iron castings on this and the linked thread 23909.
I'm not getting castings plated, but a pure Iron which has been fully machined, therefore no Carbon to create 'smuts' and no evidence of pores for solutions to leach out of.
There sure is a lot of interesting reading though!
- Staffordshire, United Kingdom
February 10, 2020
February 2020
A. Hi again. I hate that damn word "iron" :-)
It can mean the element, but more commonly it means a metal with more carbon in it than steel, and thus sometimes problematic because of the extra carbon. But apparently it can also mean a metal with less carbon in it than steel, and thus sometimes problematic because of the lack of carbon :-)
I'm not personally familiar with plating of high purity iron and would not expect it to have special plating issues that steel doesn't have -- but again I have no actual knowledge of it. So I think the usual problem of inadequate pretreatment is the issue, but would consider the possibly that the pretreatment requires somewhat stronger acid activation, or a very quick trip from the activation to the plating tank due to pure iron's corrosion resistance. I'd like to hear from someone with specific experience.
Regards,
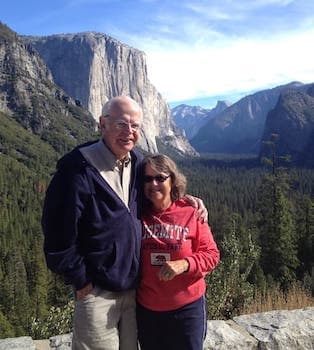
Ted Mooney, P.E. RET
Striving to live Aloha
finishing.com - Pine Beach, New Jersey
February 13, 2020
" I hate that damn word "iron" :-) " Love it Ted!
<0.05% Carbon in our Iron for best magnetic properties. It makes it a devil to plate, but even worse to machine.
Interesting what you say about stronger acid activation. We've just started experimenting with that. I'll also pass on the tip about a faster trip from activation to the plating tank.
- Staffordshire, United Kingdom
Q, A, or Comment on THIS thread -or- Start a NEW Thread