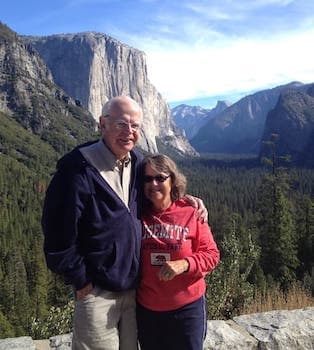
Curated with aloha by
Ted Mooney, P.E. RET
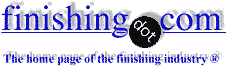
The authoritative public forum
for Metal Finishing 1989-2025
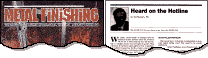
-----
Thin corrosion resistant coating of small pneumatic motor
2006
We manufacture pneumatic tools for a very harsh environment. The tools receive little to no preventative maintenance, let alone lubrication. The air tends to be quite damp and the tools are cleaned daily in a slightly caustic cleaning solution. We're trying to avoid manufacturing the motor in stainless steel and are looking at possible coatings that could be used to help prevent corrosion.
To maintain backwards compatibility of spare parts with existing tools in the field the coating can be no more than 1.5 microns thick. Also it would be advantageous if we were able to prevent coating of certain areas to be able to maintain tolerances.
Any suggestions of possible coats would be greatly appreciated.
Thanks
Food processing equipment - Auckland, New Zealand
2006
What metal(s)?
Any bearing surfaces?
What current finish(es)?
Are you looking for a sealant over present coating, or a coating for bare metal?
Several suggestions.
1) Electroless nickel (mid- or high-phosphorus). 1.5 micron is rather thin, though.
2) Either a solvent-thinned polysiloxane or modified silicone conformal coating. For the latter, I found one with a very low viscosity (for thinness) & the following properties:
DOW CORNING(R) 1-2620 DISPERSION
1-part clear, moisture RTV cure with mild heat acceleration possible, low viscosity, hard slick finish with abrasion resistance, solvent borne, UL 746C (suitable for outdoor exposure): Tested per UL 746C Ultraviolet Exposure, 720 hours of twin-enclosed carbon or 1,000 hours of xenon-arc weatherometer conditioning, and/or Water Exposure or Immersion for seven days at 70 degrees C. The material is tested before and after exposure to these conditions for flammability, mechanical impact and mechanical strength.
For the metal pretreatment, presuming steel: Hot alkaline clean & rinse, optional HCl solution (+ inhibitor) to remove any rust, rinse, dilute phosphoric acid, rinse, hot DI rinse, dry.
Areas not to be coated can be masked with platers' tape.
- Goleta, California

Rest in peace, Ken. Thank you for your hard work which the finishing world, and we at finishing.com, continue to benefit from.
We've been studying the corrosion resistance of several hard coatings deposited by physical vapor deposition. In particular, we've found that ZrN provides rather good protection. As we regularly deposit ZrN on our medical products (scalpel blades, bone saws), the coating is suitable for food processing applications. We are in the process of running tests on various post-deposition processes that we believe will further improve the performance.
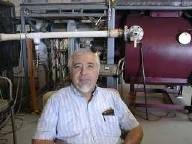
Jim Treglio - scwineryreview.com
PVD Consultant & Wine Lover
San Diego, California
2006
Q, A, or Comment on THIS thread -or- Start a NEW Thread