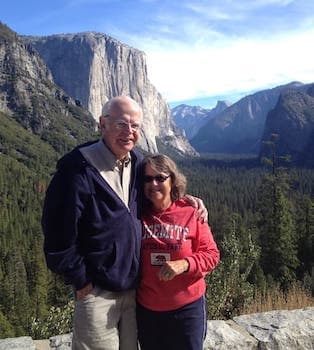
Curated with aloha by
Ted Mooney, P.E. RET
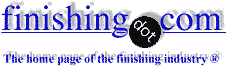
The authoritative public forum
for Metal Finishing 1989-2025
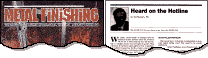
-----
Insufficient ni plating thickness on hole interiors
2006
Dear all, I am looking for fresh perspective to my issue.
I am currently tasked with the assignment to improve on a nickel-plating process which consist of:
1. Inside of several through hole of Dia. 0.45" (total hole length is
2", up to half of the
up to half of the hole length is to be plated.
2. coating thickness of 0.030"approx.
3. Parent material is standard steel.
Currently, large deposits of nickel is deposited & concentrated on the edges of the hole. Insufficient plating thickness is a common occurrance. I was told that due to the small dia. of the hole, current density as well as the thickness requirement, there is nothing much we can do to improve on the process to make it more efficient or improvement. Any one with some ideas to contribute?
Thank you for your time in reading this mail.
best regards and a happy new year!
Plating facility employee - Singapore
First of three simultaneous responses -- 2006
The ultimate answer is to use a secondary anode in each hole. This can open another can of worms as inert anodes can spoil some plating solutions like sulfamate nickel. It is also a serious pain to have the anode located exactly in the center of the hole.
Typically, you can only get some plate to go as deep as the diameter of the hole.
to reduce the major buildup on the hole edge, you could use a shield, but this is a major pain also.
A help is to reduce the extremely high current density area at the hole edge by putting a generous radius on that edge. A chamfer is not as good, but it is better than nothing. Here again bigger is better and a double chamfer is better than a single. Note, this is an improvement, not a cure.
- Navarre, Florida
Second of three simultaneous responses --
Hi Anthony,
There are some things you can do to improve the situation. You can bring your current density and Ni metal down to the low end of your bath tolerance. Higher current densities favor the higher current density areas. Keep your ph low. If you run a standard Nickel sulphate solution, I like the ph at 3.8. Set up a front to back (rocker) cathode agitation system, if tank dimensions allow. This will force fresh solution in and out of the holes, thereby introducing fresh Ni ions, even if a portion of the hole is plugged. How is your solution agitation? You should see a slight ripple at the top of the solution. Do you have solution spargers in the tank? You want to make sure your wetting agent is added to the bath when called for. Let me know how you make out!
process engineer - Malone, New York
2006
Third of three simultaneous responses --
You may need to use either a higher throwing nickel or try a shaped anode. The shaped anode should be positioned centrally in the hole and this will assist in the required plating profile
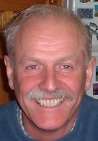
Trevor Crichton
R&D practical scientist
Chesham, Bucks, UK
2006
2006
Hi guys,
Thanks for taking the time to suggest possible solutions or minimize problem actions.
I guess I am mainly on the right track to tackle this problem as my side conclusion also suggested the trial out by
(1) Placing a anode into the hole to improve the plating. I will explore using titanium rods, any suggestions for a better material? One Question, is there a guideline such as the min diameter of the rod for it to be functional? The holes are 0.45" Dia., the rod will be at least half or 0.20" to prevent shorting of circuit if the rod were to contact with the nickel buildup.
(2) The current mode of solution agitation is using air agitation in the form of a rectangular profile tubular ring with holes drilled in placed at the bottom of the tank. when air is pumped through tubes, the air bubbles serve to displace the solution fluids out of the holes. I was thinking the effectiveness of using a pump to pump in fresh solution fluids through the holes. using a pump seem like the direct approach as I am constrained by the size of the tank due to facility space. Do you guys think it is worth a try to have a significant improvement in results?
Will keep you guys updated on my progress but the response will not be that fast as I am bundled with other projects as well. Thank you again and feel free to suggest any areas you think might help.
I am very grateful to you guys for taking the effort to reply.
Thank you!
Plating Facility Employee - Singapore
The rocker arm suggestion given by Mr. Watts can give great benefits; I second that suggestion. If a moving cathode assembly is not workable, a simple alternative you can try is to use more vigorous mixing while constantly varying the applied amperage above and below the normal static amperage (± ~20% would be a decent starting point for an initial trial and error test). This can be affected manually for test purposes and if it does provide a benefit, you can then invest in automated equipment to provide dynamic amperage control in the production setting.
This "trick" mimics the undulating current the part would experience if it was being moved back and forth between banks of anodes and by increasing the mixing rate you assist in maintaining fresh solution at the part surface.
Good luck with your efforts,
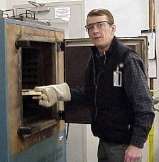
Thomas Hanlon, Materials Engineer
aerospace finishing - East Hartford, Connecticut, USA
2006
Q, A, or Comment on THIS thread -or- Start a NEW Thread