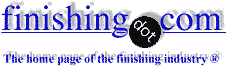
-----
Galvanizing is Peeling
Q. Dear sir,
My problem is peeling on galvanized steel profile (80 mm and up) while testing our products with hammer. Sometimes there is no problem but sometimes there is. I changed the bath temperature 435-455, but I did not find any solution. What is the cure? Please help me.
galvanizer - Ankara, Turkey
2006
2006
A. Sir: There are generally two types of hot dip galvanizing peeling problems: (1)The peeled coating is bendable and the cause is improper cleaning or fluxing of the steel. (2)The peeled coating is brittle (snaps if one tries to bend it to a right angle) and the cause is reactive steel that is too long in the zinc at too hot of temperature. Often too long in the zinc is caused by bad flux (especially one with sodium chloride in it). Any zinc coating thicker than 6 mils (152 microns) is quite subject to strike impact peeling. For reactive steels (containing silicon and especially phosphorus) at usual galvanizing temperature the growth rate of zinc is about one mil for each minute the product is in the zinc. Thus longer than 6 minutes gives more than 6 mils and strike impact causes peeling. I think in the USA the hammer test has been discontinued.
Regards,
Galvanizing Consultant - Hot Springs, South Dakota, USA
A. You should try with higher concentration of Al in Zn bath.
>From 0.16 to 0.20%.
steel- Skopje, Macedonia
2006
2006
A. Sirs:
This is in response to Zarco's advice to increase aluminum to 0.16% to 0.2%. In galvanizing profiles I assume they are done the same as any other product after fabrication with a zinc ammonium chloride flux. If this is the case (unlike continuous sheet and hydrogen/nitrogen cover) the MAXIMUM aluminum in the zinc can only be BELOW 0.007%. Otherwise the aluminum interferes with the flux and great quantities of white aluminum (III) chloride smoke results with many, many "black" (bare) spots. I believe that Zarco's advice may not be accurate in this case.
Regards,
Galvanizing Consultant - Hot Springs, South Dakota, USA
Galvanizing Sandelin steel
Q. Dear Dr. Cook (and others):
Sirs, I'd like to ask a follow-up question regarding "reactive" steels. How reactive really is a reactive steel? Almost always from literatures and references reactive steels are being referred to as steels with high silicon content (and sometimes with phosphorus). I also came across of others naming it "sandolin" ^sandelin steels which I presumed to be coined after sand which contains silicon or silica for that matter.
Based on the physical properties of silicon (Si) and Silica (SiO2) either present naturally in the ore or used to deoxidize or "kill" steel, they are quite thermally stable at the zinc bath's normal operating temperature range of 440 to 460 °C with respective melting points of 1,414 °C and 1,665 °C (for silica as fused quartz). They also have Mohs hardness of 7 and 5.3 - 6.5 respectively. Steels therefore having these element/compound are basically unreactive. This inert characteristic is then thought to cause dull gray appearance of the coating, black or bare spots, and even peeling perhaps when present in excessive amount.
It is my belief therefore that the term "reactive" could have mean something else and that would be the presence of "detrimental impurities" phosphorus (P) and sulfur (S). These two elements have low melting points of 44 °C and 115 °C with respective Mohs hardness of 0.5 and 2. They must and should be the reason for the mottled appearance of steel after galvanizing due to zinc's pattern of diffusion/attachment and should be kept as minimum as possible to avoid peeling of the coating or corrosion if we apply it to zinc's action on the kettle wall in time aggravated by high kettle temperatures. By all means this is also the reason why aluminum comes important in high amounts (>0.02 % w/w) not only as a brightener but as a "filler" to suppress extended reaction of the zinc however its oxide on top of the zinc bath will inhibit galvanization.
Coherence cannot be applied to silicon with these two elements if steel is silicon killed however may be true if occurring naturally in the iron ore.
With your valuable inputs on this discussion, I am hoping that what seems to me a misleading terminology would be given its righteous meaning.
Kind regards.
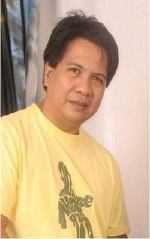
Barlow Campano
galvanizing chemist - Jeddah, KSA
November 9, 2010
November 13, 2010
Dear Sirs:
My apologies, it is "Sandelin" and not "Sandolin"; that explains why I am not seeing many facts/writeups about it on the net or other resources. I understand the steel reactivity profile was coming from a curve plotted by a metallurgist, Dr. Sandelin, way back in the 1940's(?) showing zinc coating thickness plotted against silicon mass in steel. I am assuming that during his era silicon-killed steels were not that predominantly manufactured or the technology (most likely borne in search for cost-effective products) might have not existed yet. I had the notion therefore that his presentation was deeply related if not very much reflective to what I call the real culprits behind steel's "reactivity" that are phosphorus and sulfur present with silica in the iron ore. My sources for these "detrimental impurities" dated back to 1959 (Leicester Hamilton and Stephen Simpson of Talbot's Quantitative Chemical Analysis).
and they have not written anything about silicon steel or silicon killed steel in the book.
Regards.
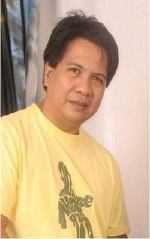
Barlow Campano
galvanizing chemist - Jeddah, KSA
Causes of galvanizing peeling
Q. Dear Dr. Cook:
Kindly advise me about more reasons of flaking and peeling besides long time in air before cooling in water, the phosphorous ratio more than 0.003%, long time inside the kettle, and poor cleaning in acid.
Thanks my friend.
Yours sincerely,
- Yingkou, China
December 8, 2012
A. Sir:
There are basically two types of peeling:
(1) The product is not properly pickled and properly fluxed. In this case the peeling comes off as a flexible sheet. This type is rare and I saw it once. The steel was re-phosphorized and aluminum semikilled steel.
(2)The other type relates to "reactive steels" and thick zinc alloyed coatings form (above about 6 mils (150 microns)). The zinc coating is brittle and easily breaks with a "snap". Thus knowledge of what makes a reactive steel is important. The following is my list which I consider to be reactive elements that cause a steel to be reactive:
(A) Silicon between 0.05% up to about 0.15% and then silicon above about 0.3%,
(B) Phosphorus above about 0.015%.
(C) Aluminum semikilled steels (likely above about 0.06% aluminum).
(D) Various cast irons.
(E) Copper (as in Cor-10) above about 0.1%.
There are others and other combinations, but I do not have at hand the galvanizing book by Heinz Bablik (1940) or a recent article on this subject.
Galvanizing Consultant - Hot Springs, South Dakota, USA
A. I've seen galvanize peeling on several different substrates, and some unexplained cases.
In addition to the above:
On 3 mm sheet steel, where the zinc peeled off. Not a thick coating, probably not reactive steel, but shotblasting prior to pickling solved this one.
On 10 mm wall 100 x 100 SHS, where a <100µ coating peeled. No explanation, and no cure found.
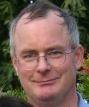
Geoff Crowley
Crithwood Ltd.
Westfield, Scotland, UK
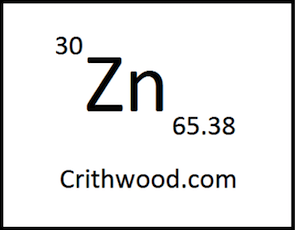
A. Please tell me whether you are quenching the material after galvanizing or not? If yes, what is the process and with what?
This will solve your problem.
- Mumbai, India
February 23, 2013
Two million pounds of galvanized coil is delaminating when bent
July 3, 2014by NACE
[only rarely available]
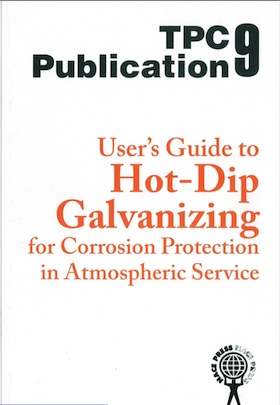
on eBay or Amazon
or AbeBooks
(affil link)
Q. Dear Experts,
We are faced with a problem in our products:
More than 1000 tons of our products have delamination. When we bend the strip with hand, to less than 180 degrees, we are faced with delamination. I really do not know if it is peeling or flaking. Our QC controllers could not see this defect on line. However, when we send products to customers we are aware from this situation. We just know that Hot Rolled of this products have stain.
Now, if you let me, I would like to know the reason of delamination in galvanizing coil?
- Tehran, Iran
Hi Ehsan. This forum can often be helpful and I hope it helps you. But sometimes it takes days or weeks before everyone sees it, and even then not all are willing to freely share their knowledge. And even if they did, they probably don't have enough info.
What I am getting at is that while you are very welcome to post here, if I had 2 million pounds of product at risk I would do my best to retain a world class galvanizing consultant immediately :-)
Regards,
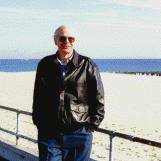
Ted Mooney, P.E.
Striving to live Aloha
finishing.com - Pine Beach, New Jersey
July 2014
July 3, 2014
A. Sir:
For a flux do you use zinc ammonium chloride solution or a gas flux with 5% hydrogen and inert gas? Do you use caustic? Do you use HCl? Does the delaminated zinc coating bend easily or is it brittle? How thick, in microns, is the zinc coating? What is the steel composition? What is the zinc composition (additives like Al, Sn, Bi, Pb) etc.?
Regards,
Galvanizing Consultant - Hot Springs, South Dakota, USA
Q. Dear Mr. Mooney & Dr. Cook,
First of all, I really would like to thank you for your attention.
Our line is Hot-Dip Galvanizing and we do not use Flux in our line. In addition, we do not use caustic and HCL in our line. we just have used HCl in pickling line and we sure it would be cleaned at the end of line. Delaminated zinc coating bends easily and thickness is about 8 microns in each side.
St12 is steel composition, and zinc composition is: Al= 0.21, Pb= 0.12, Fe= 0.0047
- Tehran, Iran
July 5, 2014
A. Hi,
In order to help you, I need some more information.
Does the problem happen in hot rolled strip only, or both hot and cold rolled condition? In which thickness range?
Does it flake all over the width or just near the edges?
Best regards,
- Porto, Portugal
September 4, 2014
A. Sir:
I have worked for only three sheet line galvanizing companies (North America, Panama, and Istanbul). In each case they had a zinc ammonium chloride water solution flux with high baumé and an ACN between the monosalt and the double salt. I am aware of sheet lines that use hot gas of 95% nitrogen and 5% hydrogen as a flux, but I have not seen them. I do not think sheet galvanizing can be economically accomplished using only HCl.
You are using 0.2% aluminum in your zinc to prevent zinc/iron alloy build-up on the surface of your sheet. As I remember the past (quite some time ago), they may have used closer to 0.15% aluminum for this purpose. Your observation of only 8 microns of zinc is quite thin indeed. I do not understand your use of 0.2% lead in your zinc, perhaps it is to give you a slight spangle in the coatings. I recommend that you review your process and look more closely in the literature to have a properly functioning sheet line.
Personally I do not believe you can galvanize in a sheet line without any flux at all.
Regards,
Galvanizing Consultant - Hot Springs, South Dakota USA
September 10, 2014
November 17, 2014
A. Interestingly, letter 13235 is about copper immersion deposit onto the pickled steel strip if Cu is present in the pickle liquor above the threshold limit. There is a possibility that there is a connection between Cu deposited on the steel strip and the galvanized strip adhesion failure. Has anyone experienced this before?
By the way, Ehsan, we are waiting for your response to Mr. Joao Pires's question.
Best regards
YKVoo
- Shah Alam, Malaysia
March 24, 2016
Q. Hi everybody, I've experienced some peeling or flaking with a customer's product - cable support system. My main problem is when the goods were here in our yard (after galvanizing), there was no problem with the coating condition. It was during installation at site in which the zinc coating peeled off. How can this issue be addressed or prevented? I have attached some photos for my fellow enthusiasts to view.
(Hi rez versions of first 3 photos are available by clicking on them)
From my understanding if the steel was not thoroughly cleaned and fluxed, wouldn't there just be black spots or wouldn't the steel just be uncoated? Please could you give some expert advice or comments. Best Regards, John
TC KhooGalvanizer - Shah Alam, Selangor, Malaysia
![]() |
March 24, 2016 A. This is a relatively rare issue. Its hard to tell from the image, but the steel looks quite thin, perhaps 3-5mm thick? ![]() Geoff Crowley Crithwood Ltd. Westfield, Scotland, UK ![]() March 25, 2016 A. Sir: Galvanizing Consultant - Hot Springs, South Dakota, USA |
A. Dear all, some years ago, our customer had similar problem, and reason was high acid drag-over in the flux solution. After pH adjustment with ammonia ⇦ on eBay or Amazon [affil links] solution, zinc flaking problem disappeared.
Ihor Krupa- Budapest, Hungary
April 12, 2016
A. Dear Mr. TC Khoo,
Your problem of zinc flaking is because of High coating on very smooth surface.Pl, try to minimize immersion and withdrawal time and dip in quench tank as soon as possible.
- Vadodara, India
July 26, 2016
A. Material is peeling off
1. Please ensure the quality of the steel which you are Galvanizing.
2. If steel is Ok. then in Zinc Bath do not add anything even Aluminium.
3. Keep the Bath Temp 445-450 Max.
Galvanizers & Consultant - Delhi. India
August 4, 2016
Q. PLEASE CAN SOMEONE ADVISE WHAT HAS HAPPENED ON THIS GALVANIZED MATERIAL?
Architectural Facades - Dubai, U.A.E.
June 12, 2017
A. It's a bit hard to tell from the picture. Both incidences seem to be on the same face, and both black. Is it on top of the zinc? Or is there bare steel underneath the black and no zinc?
This could be bare patches caused by insufficient cleaning in pre-treatment, possibly as a result of paint or other contamination on the steel. It would result in such a black sooty deposit.
But that's a guess based on a single image and not much info.
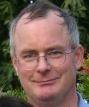
Geoff Crowley
Crithwood Ltd.
Westfield, Scotland, UK
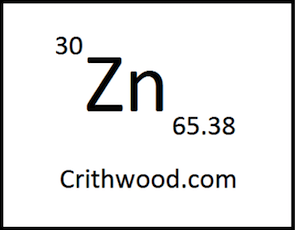
June 16, 2017
June 23, 2017
A. Sir:
Looks like incomplete pickling or bad flux to me.
Regards,
Galvanizing Consultant - Hot Springs, South Dakota, USA
A. Dear
Pictures are not telling true story. What I can say:
1. The work is not properly cleaned.
2. The Zinc Coating is not proper. Peel off Zinc coating can be easily identified.
3. Before further alkaline painting the Galvanized surface is treated with etching chemicals. So that the Paint can stick with GI surface properly.
Regards,
- New Delhi. India
June 27, 2017
Q. Hello everyone, we just ran into some adherence issues ourselves. We have fixed a couple items on our furnace but still have sporadic issues with adherence. We can run several days with no known issues and suddenly start pulling zinc off during our impact test on one order. I know, must be steel chemistry but we have ran this alloy for years without issues.
First, when we encounter bad adherence the base metal is clean. No black soot or film is seen on base metal. I assume this would not be a oxidation issue then or dirty strip entering bath?
Second, we do have a leak at the jet cool to hot bridle transition just before the snout. I have abilities to measure furnace pressure in several locations. We run at .5 in wc and at the location of our leak we measure .3 in wc. So, I am reluctant to believe this is the source of our problem since it is still positive. Would this belief be correct? We have plans to seal this leak during next shutdown, but don't want to get my hopes up assuming this will cure our issue?
Any advice would be greatly appreciated. Thanks.
Scott
- Fort Wayne, Indiana
January 25, 2018
A. Zinc peeling problem is because of two reasons the first one is improper flux chemistry. The second one is if the material has not been pickled properly. This should not be possible n your case. Flux seems to be the problem.
Vishal AgarwalIndana steel pvt.ltd - Mumbai, Maharashtra, India
March 19, 2018
Q. I am not sure what is mean in regards to improper flux chemistry. I assume you are referring to our hydrogen/nitrogen mixture? We run quite high with a hydrogen percent of 20%. We do not have a flux solution, but rather a direct fired section into a radiant tube heat section, and last through our rapid jet cool section. I have checked dew points and ppm of oxygen in each of our eight jet coolers with everything checking within range. Any additional details or potential causes are greatly appreciated. Thanks
Scott Scanesti [returning]- Fort Wayne, Indiana
May 31, 2018
A. This thread suffers from misunderstanding.
Some parties are talking about continuous strip galvanizing, and others are speaking of post fabrication batch galvanizing.
The arrangements of the two processes are quite different.
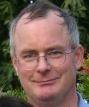
Geoff Crowley
Crithwood Ltd.
Westfield, Scotland, UK
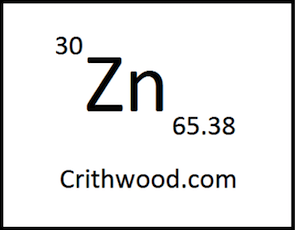
August 15, 2018
Q. Does sulfur content in rolling oil composition affect the galvanizing? Can elemental/bonded sulfur from sulfurized vegetable oils react with steel during cold rolling, and can it be reason for galvanizing defects?
Ganesh Pore- Mumbai, India
May 16, 2019
A. Hi cousin Ganesh. Please tell us what has led you to raise this question? Do you have other 'galvanizing defects' in mind besides peeling?
Please tell us your own situation, and maybe your hypothesis, rather than casting your question in the abstract. As previously noted, our helpful readers repeatedly tell us that they don't want us to post hypothetical questions which ask them to speculate open-endedly while also covering a dozen "if, ands, & buts". They want to straightforwardly try to help you with your individual situation, not to write white papers or lecture the world. They are far more likely to respond to you if you introduce your own particular situation. Thanks for your understanding!
Regards,
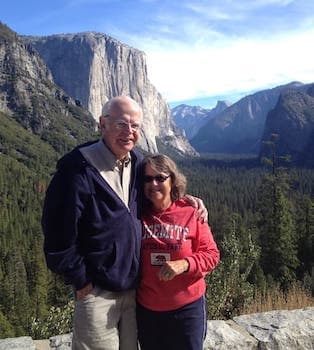
Ted Mooney, P.E. RET
Striving to live Aloha
finishing.com - Pine Beach, New Jersey
May 2019
September 11, 2019
Hi,
I am a steel fabricator and I have a problem with a lot of galvanised steel bars and plates (from 3/4" to 1" thick). My customers need more resistant coating than standard specified (ASTM A123).
We select with high precaution our steel to be on the sweet spot to galvanise. Silicon is ranging between 0.17-.22, carbon is less than 0.15, phosphorus is under 0.01 and Mn is under 1.3.
All contours are machined and chamfering is done on the edges. But when I test with an hammer on the edge, the coatings are blowing out.
Is it possible to know if the pickling and flux are made correctly by my galvaniser?
Lawrence Martin- Quebec, Canada
A. Sir: To learn more about flux see the on-line library on this website. Also check the 20 second dynamic flux test also in the on-line library.
Regards,
Galvanizing Consultant - Hot Springs
September 15, 2019
September 25, 2019
Lawrence.. what thickness of steel plate is this (hard to tell from image)?
How is it cut? Gas? laser? plasma?
I have found that gas cut changes the chemistry of the steel for a few microns into the steel from the cut. Grinding or blasting that cut surface changes the galv thickness on that surface. You mentioned machining. That would also remove this effect of the cutting method.
Is there any measurable zinc alloy thickness in the part where the galv peeled? If not this looks like very unreactive steel (too low in Si).
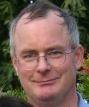
Geoff Crowley
Crithwood Ltd.
Westfield, Scotland, UK
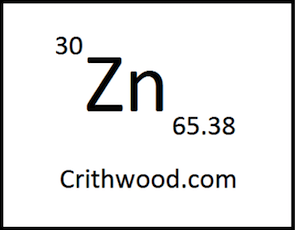

Q, A, or Comment on THIS thread -or- Start a NEW Thread