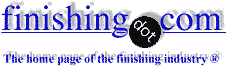
-----
Alkaline Zinc Plating Q&A's, Problems & Solutions

"Plating slows at higher temperatures"
"Yellow chromate is stained, dull, inconsistent"
"Blue works, but green chromate turns blackish"
"Groove/gouge line caused by plating"
"Brown spots develop in storage"
"Iridescent passivation peels off"
"Yellowish zinc deposit"
"Effect of Temperature"
"Part is smaller in diameter after plating"
"Burning"
"Shiny edges and dull centers"
"Chemical flow in welded area"
"White Tarnish, White Corrosion"
Q. Hello
I have a wire drawing workshop and I had bought basins for continuous electro zinc coating because our market is limited. I decided to use non-cyanide alkaline zinc and I did an experiment in a plastic basin using sodium hydroxide 120 grams per liter and I used distilled water and 10 grams of zinc and I experimented on a low carbon wire with a diameter of 2 mm
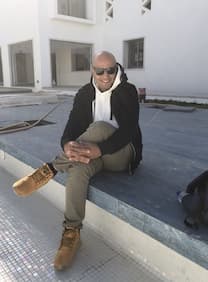
Yahya saleh
Shop - Iraq/erbil
June 7, 2023
A. Hello Yahya.
You didn't ask a question, but apparently you are showing us unsatisfactory plating.
I have never heard of continuous alkaline zinc plating of wire myself, although hopefully other readers have. Even so, the idea of doing satisfactory plating at all, let alone in continuous fashion, using just a zincate solution doesn't sound promising, let alone easy.
If possible, I think you should try to get access to Geduld's "Zinc Plating" [on
Amazon,
AbeBooks affil links], perhaps through a university library, and meet with someone familiar with alkaline zinc plating and someone with wire plating experience. There is sometimes a tendency to believe that plating can be learned in 15 minutes, and solutions made up from raw commodity chemicals, but in truth it's probably roughly as complex and demanding as wire manufacturing and drawing :-)
Luck & Regards,
Ted Mooney, P.E. RET
Striving to live Aloha
finishing.com - Pine Beach, New Jersey
Q. Hi
It's like this
8m HCl
2m water
12m electroplating
2m dryer
I was going with acidic zinc solution
But the materials are not available in my market
So I'm going now with alkaline non-cyanide bath
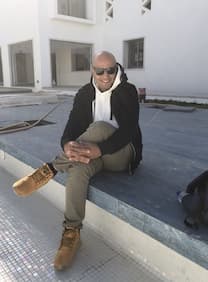
Yahya saleh [returning]
- Iraq/erbil
June 7, 2023
A. Hi again. What about alkaline cleaning before the HCl? What about chromate conversion coating after the plating? Those 2 things are conventional.
8 minutes in HCl sounds excessive to me.
Luck & Regards,
Ted Mooney, P.E. RET
Striving to live Aloha
finishing.com - Pine Beach, New Jersey
Surface Roughness in Alkaline Zinc Electroplating
Q. We are running an in-house Alkaline Non Cyanide Zinc Electroplating plant to plate on Hardware Goods.
We are facing issues of surface roughness on 99% of the processed parts.
We have performed a detailed zinc dust and carbon treatment to remove any metallic or organic impurities. The finish produced is absolutely uniform and bright but upon touching the parts, roughness is felt.
Plating bath have following parameters :
Zinc Concentration : 11.5 gram/litre
NaOH: 130 gram/litre
Temperature : 28
Hull Cell
⇦ huh?
analysis show that brighteners are well in balance which is confirmed by the beautiful finish produced by the tank too.
We are running continuous filtration using disk type filters prepared with a layer of PP cloth and filter paper with approximately 4.5 turnover per hours.
Note: we have not changed our chromate conversion/ passivation bath in last 3 years as we are running an ion exchange system to remove the iron and zinc from it.
- Kaithal Haryana
March 4, 2025
A. Hi Shrey
Can we assume that there is no roughness in the Hull Cell panels that you run?
Can you pull a few parts after plating and before chromating to determine whether they come out of the plating tank rough or acquire the roughness in the chromating?
Luck & Regards,
Ted Mooney, P.E. RET
Striving to live Aloha
finishing.com - Pine Beach, New Jersey
Thank you for your reply Mr. Mooney. Yes we have pulled out some parts after plating and tried chromating in a separate small bath where there was no difference in roughness.
Also we tried to pull a 30 Ltr solution from the tank and tried plating in a bucket outside the results of which are absolutely similar with Hull Cell.
Regards
- Kaithal, Haryana
March 8, 2025
A. Hi,
If the roughness appeared on Hull Cell panels at all current densities and before chromating, it sounds liker perhaps your filter is defective in some way. You should be able to filter 275 ml for a Hull Cell test through a Wattman filter in your laboratory to see if particles are causing the roughness and can be removed.
Luck & Regards,
Ted Mooney, P.E. RET
Striving to live Aloha
finishing.com - Pine Beach, New Jersey
A. Hi Chaudhary, alkaline zinc bath roughness, Try to put potassium hydroxide replace sodium hydroxide, Sodium carbonate buildup in bath Na carbonate buildup cause roughness. Fish the tank falling from rack to the tank. Need to pull out ASAP, run the filter & change filter bag every day.
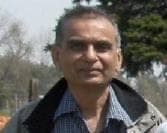
Popatbhai B. Patel
electroplating consultant - Roseville, Michigan
⇩ Related postings, oldest first ⇩
Q. Has anybody got information about alkali non-cyanide electroplating of zinc onto steel? We have tried the process unsuccessfully so far. Cleaning seems to be a critical factor in the process as the operational window for plating is far less tolerant than the cyanide based process.
Paul Hickeyplating shop
1998
A. Paul,
Electrolyte NON-CYANIDE ZINC ON STEEL PROCESS STEPS
1.SOAK CLEANER
2.ELECTROCLEANER
3.RINSE
4 RINSE
5.HYDROCHLORIC ACID DIP
6.RINSE
7.RINSE
8.NON CYANIDE ALKALINE ZINC
9.RINSE
10. RINSE
11.SEALER REQUIRED BY CUSTOMER OR NOT
12 DRYER
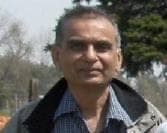
Popatbhai B. Patel
electroplating consultant - Roseville, Michigan
March 16, 2025
Q. I have problems with alkaline zinc - hanging. He refers to very badly. Content of zinc is 8,5 g/l and NaOH 135 g/l Has perhaps who experience with Protolux 3000?
Vlasta Baùiè- Maribor, Slovenia
2005
A. Protolux solutions don't cope well with high concentrations of Sodium Carbonate. If the concentration is above 60 g/l you would expect quite a drop in solution efficiency.
Dougie Lightfoot- Fife, Scotland
![]() |
A. Try to maintain 1:10 ratio Zinc:Sodium Hydroxide. ![]() T.K. Mohan plating process supplier - Mumbai, India A. It sounds to me that your having problems keeping your metal content up. 135 g/l sodium hydroxide is ok but 8.5 g/l sounds a little low. - East Sussex, England |
Yellow chromate is stained, dull, inconsistent
Q. I have problems with alkaline zinc plating because the performance of its product (plated) is not bright, and yellow stains. About the clear coat/top coat's hardness is less, or easy to be broken and the colour is yellowish/yellow stain. Do you have any advise for me about it? Maybe the properly timed oven, or kind of clear coat, and chemicals/treatment used in plating? Thank you very much.
Regards,
plating - Indonesia
2006
A. Dear Ms. Anggraeni,
Have you checked with "Hull cell" the performance of the solution whether is it okay or not?
Your problem can be the additive system or lack of control of the additive and has other contamination like water hardness, do you use Demineralized water for the plating solution and might be rinsing before entering plating bath?
You did not tell properly what kind of Chromating that you are using now, either Hex-Blue or Trivalent Blue.
In my opinion, Trivalent Blue is more sensitive to be yellowish blue and non uniform for Alkaline Non-cyanide Zinc (I presumed) that has Iron contamination inside the solution.
Try to treat the solution by using zinc dust
⇦ on
eBay or
Amazon [affil links]
treatment and consult with your local supplier.
Good luck.
Best regards,
- Jakarta, Indonesia
A. Dear Anggraeni,
You have not given any details about your process and other details about what kind of items you plate.
Kindly give details:
Process used: Alkaline Zinc, Cyanide or non cyanide:
Vat or Barrel plating:
Bath capacity:
Work being plated:
Metallurgy of the product plated :
amperage per sq. ft. applied:
Plating time:
Details of addition of all additives:
Details/intervals of regular maintenance carried out:
Details of regular treatment carried out:
Do you analyse your bath:
From your letter I think your bath is not properly treated or maintained. The additives and the constituents are imbalanced. Please give clear details to get clear suggestions.
Regards,
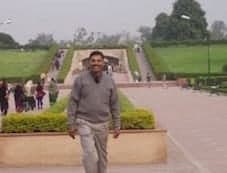
T.K. Mohan
plating process supplier - Mumbai, India
Q. I am using alkaline zinc plating ,
I use raw water only,
if use continue raw water which type of problem will come,
I need clarification about impurities in the raw water.
Plating shop employee - Chennai & India
April 15, 2008
A. Hi, Guna. What problems would come if you made coffee or soup with this water? :-)
Lots of people use raw water if it is not terrible. But the best path is to keep moving forward and to decide that you need RO or DI water because this junk doesn't belong in your plating tanks. It is difficult to say exactly what problems would result from use of water of unknown quality; excessive calcium, chlorides, iron, and the other things in raw water are contaminants that eventually spoil the plating solution. You would have to study what contaminants are in the water and in what concentration, and whether this is close to or far less than the technical data sheet suggests as troublesome.
Sorry that I don't have a "real" answer for you.
Regards,
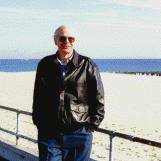
Ted Mooney, P.E.
Striving to live Aloha
finishing.com - Pine Beach, New Jersey
A. Dear Gunashekaran,
Raw water if not really good say not of good quality will give a yellow tint to plating and this will continue to show if blue passivated. Generally supply houses will supply a conditioning agent to deal with such impurities from water.The best is as Ted said, invest in a DI/DM water generating equipment. But make sure you give a sample of water presently used to the equipment maker.
Good luck
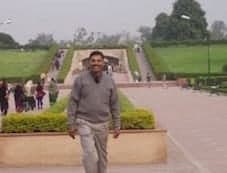
T.K. Mohan
plating process supplier - Mumbai, India
A. Dear Friend,
Using DI/DM water is advisable. But if you hardness is moderate, in some cases you can use water softening chemicals in your bath.
Hope you are in Chennai and it is difficult as the hardness is more in your case.
Please opt for DM/DI water.
Thanks
plating process supplier - Bangalore, India
Blue chromates work well, but green chromates turns blackish
Q. I'VE HAD A 2000 LTR NON-CYANIDE ALKALINE ZINC BATH RUNNING FOR THE LAST 6 MONTHS. I AM FACING A REGULAR PROBLEM THAT AFTER PLATING COMPONENTS IN THE BATH AND THEN DIPPING IN HEXAVALENT OLIVE GREEN PASSIVATION BATH. I'M GETTING A DARK & BLACKISH FINISH. BUT WHILE DIPPING IN HEXAVALENT BLUE OR TRIVALENT BLUE PASSIVATION SOLUTION I GET AN EXCELLENT FINISH ON THE COMPONENTS. WHAT IS THE POSSIBLE CAUSE BEHIND THIS? HOW TO SOLVE IT?
BHASKAR CHAKRABORTYELECTROPLATING - Kolkata, West Bengal, INDIA
March 26, 2012
A. Hexavalent olive green passivation is dark green with blackish shade, which is okay. If you still want green, then change pH to higher side this will work.
Ramchandra Talwande- India
Groove/gouge line caused by plating
Q. Deep like marks up to 4 micron observed on the non-cyanide alkaline
Zn electroplated steel article. The article is a case hardened and tempered 16MnCr5 steel processed through sheet metal stamping route.
Plating is done by Rack method and there are no such marks observed on the article before plating. Hexavalent Cr passivation is done on the article.
Plating thickness is evidenced over the line mark and there is no discoloration observed.
Request the experts in guide me how this kind of deep mark is possible?
Srinivasan Rajagopalan- Bangalore, India
July 14, 2013
A. Hi Srinivasan. I certainly don't claim to have seen everything, and I cheerfully welcome a contrary opinion . . .
But having never seen a problem like that resulting from a plating operation, I tend to disbelieve the evidence that the mark was not there before plating. I suppose it's possible that parts were racked in such a fashion that an interrupted contact could cause a bipolar effect that dissolved the component along this line . . . but again I have to doubt it.
Can you tell us anything about frequency, whether the line runs the same direction each time, etc.?
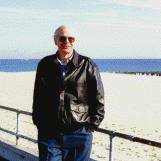
Ted Mooney, P.E.
Striving to live Aloha
finishing.com - Pine Beach, New Jersey
Q. Thank you for the feedback. The frequency of defect is 3 to 10 percent in every batch. The direction of loading is always in the same way. Find attached the jigging photograph.
Request your feedback.
- Bangalore, India
Brown spots develop in storage
Q. Zinc plating with surface discoloration after storing for a period of time. Hi, I am Peter, a plating chemical supplier. Recently my customer faced a big problem. He plated iron parts with non-cyanide alkaline zinc + iridescent passivation (no sealer). The parts originally show iridescent color after plating but would discolor and show brown spot when stored for a period of time (about 2~4 weeks). Not all of the parts discolor, but only a small portion of the parts. And it would happen randomly and continuously perplex him. He has plated the parts for 4 years and discolored in the last three months. Anyone have same experience and know what happened? Thank you!
Chemical supplier - Hsinchu, Taiwan
June 12, 2013
Q. Hi,
My site also facing the same problem too.
- Klang, Malaysia
A. Hello Peter and Jeremy,
Please give some information:
Passivation (Chromate conversion coating): Hex chrome or trivalent chrome?
Bath: Jeremy, you have the same problem with an alkaline or acid zinc bath?
Thickness: Is it uniform? Is it above 5 microns? Are there scratches or chipping of the surface?
Storage conditions: Is it humid? The parts could be exposed to fogs or sprays?
Well, this is all I recall as important now. If you can give some more information, we may be able to help you both! Regards and good luck!
- Cañuelas, Buenos Aires, Argentina
Q. Hey Daniel,
Mine is alkaline zinc bath, trivalent yellow, thickness is 8-15 micron. Discoloration happens after 2-3 weeks later. After analysis chromiting bath: Fe 27 ppm, Zn 12-15 g/l and pH 1.6 -1.8! (new chromiting bath 3 months). Thanks.
A. Hi Jeremy,
Jeremy, the trivalent chromating bath generally works from 0 to 8-10 g/l zinc concentration. 15 g/l is very high, and the chromate must be very thin in this condition. I would suggest you to change, at least partially, the chromating bath.
Then, if this effect (discoloration) has always been there, I would see if the storage is done in humid conditions, if there could be some spray or fogs in the storage room or near the packaging, if the parts are exposed to light...
So, I hope we can help you too! Regards,
- Cañuelas, Buenos Aires, Argentina
Q. Trivalent iridescent chromate, zinc<9g/L
thickness : 5-15µm
storage condition: 25-33 degree, sometimes raining, but it has stored in same condition for 4 years.
I analyzed the part with EDS and found higher carbon and oxygen in the surface compared to normal part.
I also found they used water with unstable pH and flow out resin fragment randomly. This water is also used to make up passivation solution.
I have asked them to stop using the water recently.
Do you have any suggestions for this situation?
Thank you!
Chemical supplier - Hsinchu, Taiwan
A. Hello Peter,
First, if the storage hasn't changed, it isn't the cause... But you should keep the parts away from the rain!
On the EDS result, if has some more oxygen and carbon I cannot say that it is different, they are elements present in dust and in sample preparation could be some variations that could increase the carbon and oxygen proportion. If you have iron content, then you should worry!
I didn't understand the water situation, with the flow and resin. Could you explain what you mean? pH in the chromate process is very important, you should maintain the pH value in ± 0.5 points from optimum pH value for a good corrosion resistance, and trivalent chromates need a good quality water for preparation. If you define your process with more detail we could help you more!
Good luck!
- Cauelas, Buenos Aires, Argentina
Q. Hi Daniel
Thank you for your concern.I have checked the EDS of the discolored parts again and found no difference compared to normal parts. I use tap water now and still found discoloration happened randomly. The tap water pH around 6.5-7.5, current conductivity<10us/cm, TOC<2 59205ppm iC
Chemical supplier - Hsinchu, Taiwan
A. Hi Peter,
Do you control the pH in your chromate conversion bath? It is very important to maintain this value stabilized. The nominal value (in standard chromates, you should ask your vendor in this case) is 2,0. Please check this up! If the chromate has 2 steps, check both steps have controlled pH.
I haven't understood the resin situation yet, what did you mean with "flow out resin fragment randomly"? The chromate has a resin part?
Good luck!
- Cañuelas, Buenos Aires, Argentina
Q. Hi,Daniel
Thank you! I have checked the pH and this was fine. My customer's pure water system contains resin and follow out. But now they have fixed it. Will discoloration come from zinc solution? I have tried every possible parameter after zinc solution tank and now I focus on zinc solution. My customer has tried other supplier's water purifier (to reduce Ca, Mg) and said it seems it can reduce discoloration. But the plating line has regularly added the conditioner (reduce Ca, Mg) already. I think this should not be the course, What do you think? Thank you!
Chemical supplier - Hsinchu, Taiwan
A. Hello Peter!
Ca and Mg are a problem in some chromate formulations and are a problem in zinc electroplating bath always. For alkaline baths you have some conditioners that improve bath performance with the presence of Ca and Mg by getting them out the way, but you should try to avoid to replenish your bath volume with this "hard" water.
You should try preparing your chromate with another water (not hard, maybe demineralised) and see if you have some change in your process. If this improves your result of "discolored" parts, you have some problem there. If there is no change, then you have some problem elsewhere...
Hope you can solve this issue! Keep us informed and maybe we together can sort it out :)
Regards,
- Cañuelas, Buenos Aires, Argentina
Q. Hi Daniel:
Recently, my customer find a way to detect the discoloration in two days and no more have to wait for two weeks.They put plated parts into high temp/moisture oven and enhance the aging. So, we found the discoloration always happens on Monday. They will maintain the plating line on sunday. The maintenance include change rinse water and wash the tank. Besides, the zinc solution also be pending during maintenance. Will the pending cause any organic crack or metal be absorbed on anode? I think it would be something wrong during the maintenance or pending zinc solution. Please give me some suggestions.Thank you!
Chemical supplier - Hsinchu, Taiwan
A. Hi Peter,
That the zinc plating solution is still and not working during maintenance is not a problem. Is this what you refer as "pending"?
If they always do maintenance on Sunday and you have problems with the parts plated on Monday, there must be a connection between the maintenance routine or the Monday startup and this. I can't tell what could be wrong in this, but if you know what is the routine for maintenance, startup and normal work, the differences between them are possible causes...
Hope you can solve this! If you do, please share what you found with the community :)
Regards,
- Cañuelas, Buenos Aires, Argentina
Q. Dear Sir,
We have alkaline zinc plating tank, and we use the HNO3 for yellow dip approx. 2-3 ml/ liter , and also we use the H2SO4 for color maintaining. Now it's improved.
We are facing a problem in cleaning now; we are doing pretreatment (cleaning) process in HCl , but component shine is not coming, so please give us the cheap and good suggestion so that we can get shining on component.
Regards,
- Delhi, India
September 18, 2013
A. Hello Sanjeev,
That your parts shine, or your parts brightness, could depend on how you clean your parts or how you plate your parts... If you have a cleaning problem, you should see if you are loading fully degreased parts, that your HCl is in correct concentration, if you use or not a wetting agent (if you don't, you should, I think it is very helpful, and cheap), if you use or not an electrolytic degreaser...
If you answer most of these questions with "yes", then you must tell us more about your process in order to help you. If not, you should see if you can make that happen.
We (at least I) can't say anything else to help you if you don't specify more what is the defect, what are you doing, and in which conditions.
Hope this helps! Best regards,
- Cañuelas, Buenos Aires, Argentina
(you are on the 1st page of the thread) Next page >
Q, A, or Comment on THIS thread -or- Start a NEW Thread