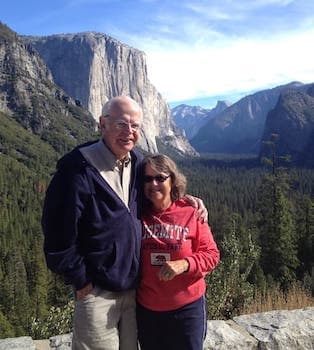
Curated with aloha by
Ted Mooney, P.E. RET
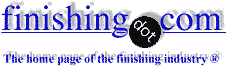
The authoritative public forum
for Metal Finishing 1989-2025
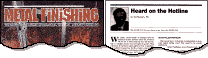
-----
Prevention of electrolysis in agriculture & oil fields
2006
Q. We are a mid-sized company with screw machines, manual machines and CNC machines. We manufacture primarily manifolds and fittings which are used in the propane industry, the agricultural industry as well as in the oil fields. We are in the process of expanding our enterprises world wide with new plants currently operating in Mexico and China and are adding new machines yearly.
We have approximately twelve vertical CNC mills here in the States, each equipped with two pallets which can hold up to four vises each. In addition, we have three horizontal mills, also equipped with two pallets each.
We have run into the age-old problem of "corrosion" in many of the new vises we have been implementing on our mills which are made out of various materials, but we think the problem stems from electrolysis occurring from the use of different metals, specifically aluminum (used for the jaws; the base cavity, which is hard anodized on the exterior; the "jaw slides"), and various types of steel, both hardened and unhardened (used for the cover plate, lead screw, nuts, bolts, pins, etc.). In addition to all of these metals are the metals of the work we are holding which are made out of everything from stainless steels, hastelloys, Inconels, carbon steels and so on.
The "corrosion" is taking place inside the aluminum base cavities (aluminum being the highest metal on the "Galvanic Corrosion Chart" that is present in our set-up) and inside the aluminum jaw slides, which have a steel lead screw running through them.
After consulting with a coolant sales representative, who seemed to understand our problem completely and who suggested a different type of coolant with a higher percent of oil base, but also admitted that we were not really fixing the problem, merely "putting a band-aid on the wound", we've committed to finding a better solution.
In an attempt to address this challenge, we are proposing to use slivers of Zinc alloy bar stock (approximately quarter inch slivers of one inch diameter ASTM B418 type II) to act as sacrificial anodes to draw the electrolysis away from the aluminum.
It has been suggested by a fellow colleague that we glue these
"anodes" inside the vise for both ease of locating them in strategic locations and for conservation of the Zinc material, rather that drilling holes through the Zinc which would also include drilling and tapping inside the vises.
Therefore, my questions to the industrialist community are; if we glue the Zinc "anodes" into the vises 1.) Dose the glue have to be conductive? 2.) And if so, can anyone recommend glue that is both conductive and that will sufficiently hold the Zinc to the aluminum?
Other questions might include; 3.) What would be the best location for the "Zincs"? 4.) And dose anyone have a better solution to this problem?
Respectfully yours and thanks in advance for you thoughtful input.
- Houston, Texas
Q, A, or Comment on THIS thread -or- Start a NEW Thread