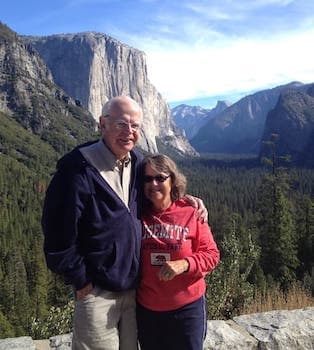
Curated with aloha by
Ted Mooney, P.E. RET
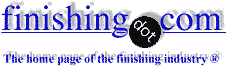
The authoritative public forum
for Metal Finishing 1989-2025
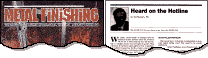
-----
Corrosion after passivation, 17-4 H1075
2005
We currently passivate a variety of stainless steels including
303, 304, 440c, etc. Just recently we've run into a problem with 17-4 H1075 showing signs of corrosion after "sitting on the shelf" for as little as 3 days. This came to our attention two weeks ago when one of our customers reported a problem with corrosion showing up on parts we manufacture and passivate in house. By the time the sample part arrived, it was covered in "blotches" of red corrosion, and was quite thick as viewed under 10X magnification. Has anyone had this problem passivating 17-4 stainless?
Sincerely,
Machine Shop - Bainbridge, New York
Let me guess. You glass beaded it with used bead or cleaned it up with a 410 stainless wire wheel.May not have been in the process sheet, but did a helpful operator do some extra to make it look good. (machine shop in particular)
James Watts- Navarre, Florida
2005
This is not an unusual thing to happen with 17-4PH parts, but there are ways to prevent this with good passivation. We have developed a new process that works extremely well with all 17-4PH parts including the difficult investment castings. We plan to publish a paper about this in the very near future. If you still need help with this please give us a call.
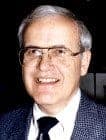

Lee Kremer
Stellar Solutions, Inc.

McHenry, Illinois
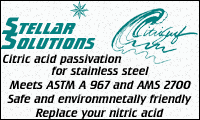
2006
2006
We solve problems like this daily with vapor corrosion inhibitor
(VCI) impregnated plastic bags. Once placed in the bag and sealed the part can sit on the shelf until needed. If the patrs are to large for bags we either use VCI plastic sheeting or water-based VCI coatings.
Regards
Grady
- Colville, Washington, USA
Q, A, or Comment on THIS thread -or- Start a NEW Thread