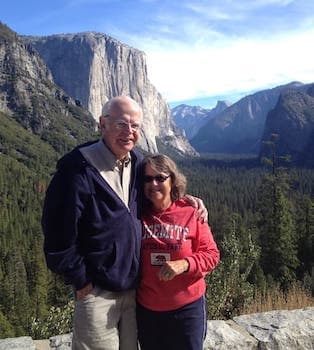
Curated with aloha by
Ted Mooney, P.E. RET
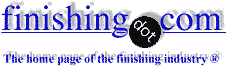
The authoritative public forum
for Metal Finishing 1989-2025
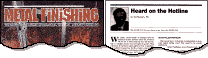
-----
Brass plating defects
Q. We have received brass plated steel wire parts from two vendors. One has a normal smooth mirror-like finish while the other has a leather-like appearance when viewed at 10X magnification. Both started with parts from the same manufacturer so differences in the wire substrate is not thought to be a factor. What plating problems would cause this finish difference?
Royce Sorensen- Eau Claire, Wisconsin
2005
A. Happy Holidays!
I would assume these wire products are reel to reel plated. Because of extreme high current densities used to keep step with high speeds the cleaners, activators, and plating solutions have to be titrated more often than lets say, a rack plating solution. Plating cells and sump tanks are generally so much smaller and conditions more severe. Is your plater close enough to visit? If not give them a call and let them know of your concern. It's hard for us to see into a shop and know what kind of operation they run. Good Luck!
process engineer - Malone, New York
2005
A. The plating looks okay on both samples, however one sample appears to have extensive mechanical damage, possibly from having been dragged over a non-rotating guide.
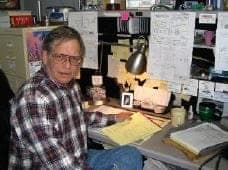
Jeffrey Holmes, CEF
Spartanburg, South Carolina
2005
Q. Thanks for the responses. I need to add information to re-direct the thinking a bit. These parts were fully assembled, deburred and cleaned prior to plating.
Royce Sorensen [returning]- Eau Claire, Wisconsin
2005
A. Now that I have seen the samples, and have noted your last response, I would have to agree with Jeff Holmes regarding the manner in which the wire was manufactured, possibly through a non rotating guide. In functional or even electronic plating mirror brightness does not always mean the plating is better.Thickness, adhesion, purity of the deposit should be a concern. Does your incoming inspection dept. ensure these qualities? If the part is going on Donald Trump's chandelier than yes, looks are everything. Not trying to be smart, just to let you know destructive testing is the way to go. This way you have documentation for your customer. Have a few extra parts ordered from the same lot for testing. Hope this will help you.
Mark Bakerprocess engineer - Malone, New York
2006
A. A simple way to rest this case would be to partially strip each wire, after carefully masking the unstripped portion to prevent spoiling during stripping and examine them under the microscope again. It is very unlikely that plating could produce such different results, the difference is from base metal itself.
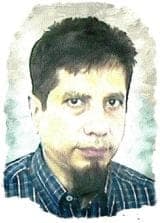
Khozem Vahaanwala
Saify Ind

Bengaluru, Karnataka, India
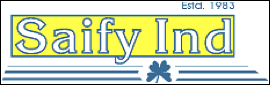
2006
Brass plating Qualification
Q. How to qualify the parts after Brass plating?
Any standards will help/guide more about the information for the brass plating on steel or any materials.
1. How to define the thickness for different environment/application?
2. How to define the testing after the plating parts?
- Salem, Tamilnadu, India
May 12, 2016
A. Hi Kannan. That is a tall order, but we can probably make progress if you can tell us what kind of parts you are plating and why, and what environment they will see. Brass plating is used for many different decorative and functional needs, often with under-layers of other metals, or overcoats of lacquer or other clearcoats.
Regards,
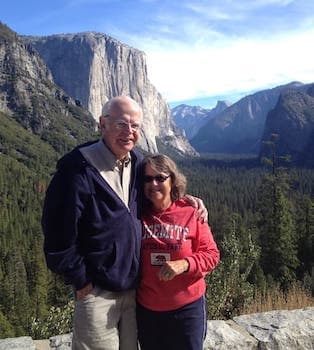
Ted Mooney, P.E. RET
Striving to live Aloha
finishing.com - Pine Beach, New Jersey
May 2016
Q. I am planning on hardware parts (Screws, Nut, washer) for the Switch, socket products.
This products can be used mostly in Indoor application.
- Salem, tamilnadu, India
July 26, 2016
A. Hi. This will be a decorative rather than functional application, so there may be no good applicable standards.
Can we assume that you are looking for a bright reflective yellow brass look? If so, you will (almost) surely want to do nickel plating before the brass plating, and lacquering or clearcoating after it. Rather than the three separate layers, some people would opt to do a brass-tone lacquer or electrophoretic lacquer on the nickel plating, which saves one step and eliminates the need for the cyanide-based brass plating step.
Since you will do doing two or more layers on what I picture as very small threaded screws, the plating will not be thick, probably a couple of ten-thousandths of an inch (5 µm) each layer. You can do salt spray testing, but it's best to do real-world testing first, so you know how many hours a good coating will survive (the lacquer is probably the most important layer). For adhesion testing you could consult ASTM B456, but many adhesion tests are rather informal (baking the hardware before lacquering to look for blistering, bending the flatwashers in half, crushing the nuts, grinding the screws or breaking them in half to look for flaking, etc.)
It would be a good idea to retain a plating consultant, or at least an experienced head plater because starting from nothing and trying to specify, then implement, then test a complete plating process is quite a big job, and you may not know how to proceed on each of a thousand steps.
Regards,
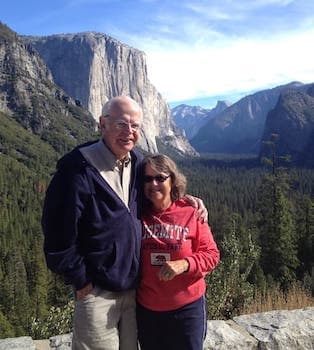
Ted Mooney, P.E. RET
Striving to live Aloha
finishing.com - Pine Beach, New Jersey
July 2016
Q, A, or Comment on THIS thread -or- Start a NEW Thread