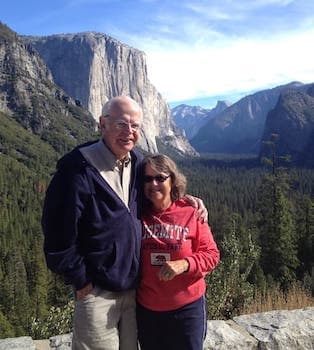
Curated with aloha by
Ted Mooney, P.E. RET
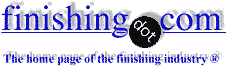
The authoritative public forum
for Metal Finishing 1989-2025
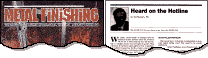
-----
Hard Anodize problems with 6061
I am having difficulty hard anodizing .002" thick on 6061. It doesn't happen on all 6061 parts, only some. We are anodizing at 36 ASF, and normally get .002" thickness in about 40 minutes, with somewhere around 50 volts. When we have the problem, the voltage rises quicker than usual, without forming the expected coating thickness. We only get about .0018" thickness after about 45 minutes, with an ending voltage of 70 volts. Has anyone experienced this problem? Does anyone know the cause? Does anyone have a fix?
Kent KesslerPlating Shop Production Manager - Seattle, Washington, USA
2005
First of two simultaneous responses --
Kent
Over the years, we have seen varieties of 6061 aluminum that have shown the same symptoms you mentioned. Typically, those parts that were 'difficult' to achieve the 2-mil thickness were manufactured from a thinner stock of material (< .5" thick), and were almost exclusively from plate stock- the only exceptions were bar stock lapped parts.
We also experienced variations in 5052 aluminum where our target thickness was 5-mil. One heat lot would take 3.5 hours and the next took 8 hours- yes, we charged accordingly.
My guess is the temper is the root cause.
Our solution was the parts took longer to run. Same amp-hours per run, but after max'ing out on voltage, we'd continue to run as the CD cropped off until we hit the amp-hours required.
Best of luck, and Happy Holidays!
- Colorado Springs, Colorado
2005
Second of two simultaneous responses --
It sounds like you are using titanium racking (a no-no for hardcoat) and you may have an oxide on your rack points. A little more info would be helpful.
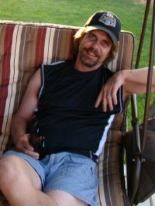
Marc Green
anodizer - Boise, Idaho
2005
Thank you for your responses - we will take a look at running a a lower current density, running a longer time.
A little more information - we are using aluminum racks (mostly 6061, with some components of 6063). The parts we are having problems with are cylindrical (close to 3" in diameter).
- Seattle, Washington, USA
2005
Hi Kent,
1. Its better to mask the unwanted areas of the racks(other than contact points), if not masked. Else the rack may draw more current.
2. Strip the rack at the end of the every batch/cycle,racks, if not following this.
thanks,
- Chennai, India
2006
Q, A, or Comment on THIS thread -or- Start a NEW Thread